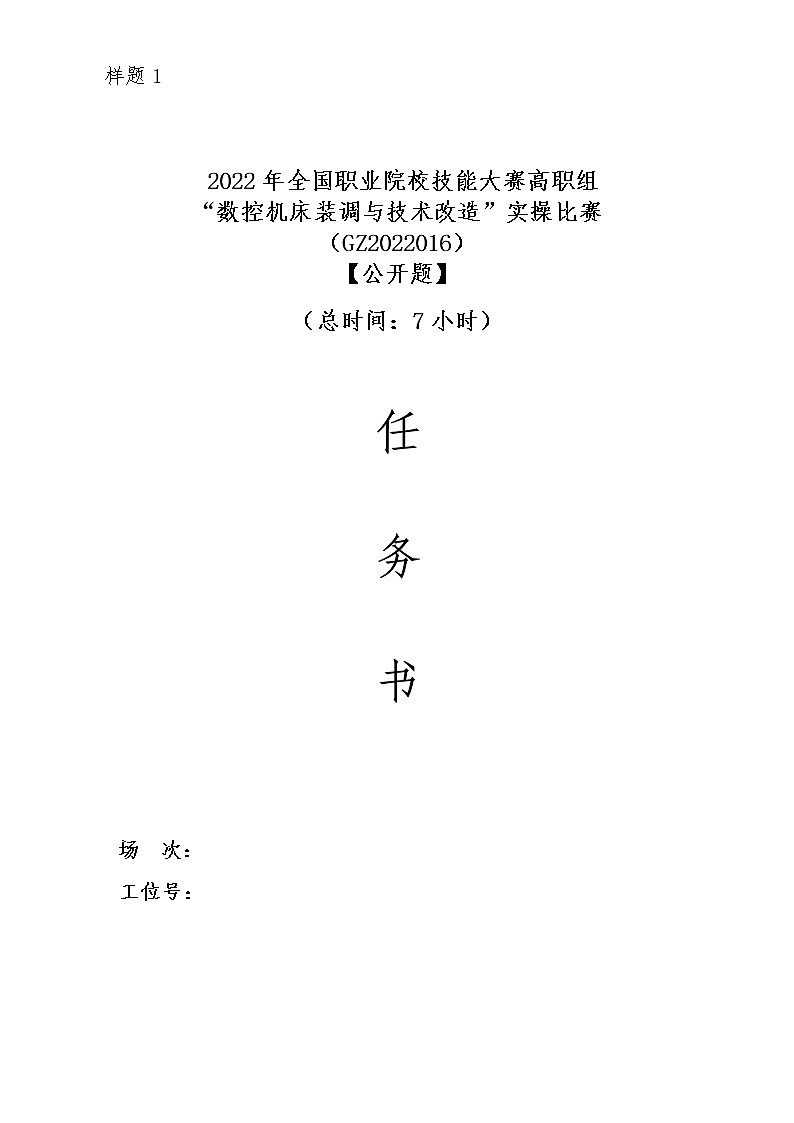
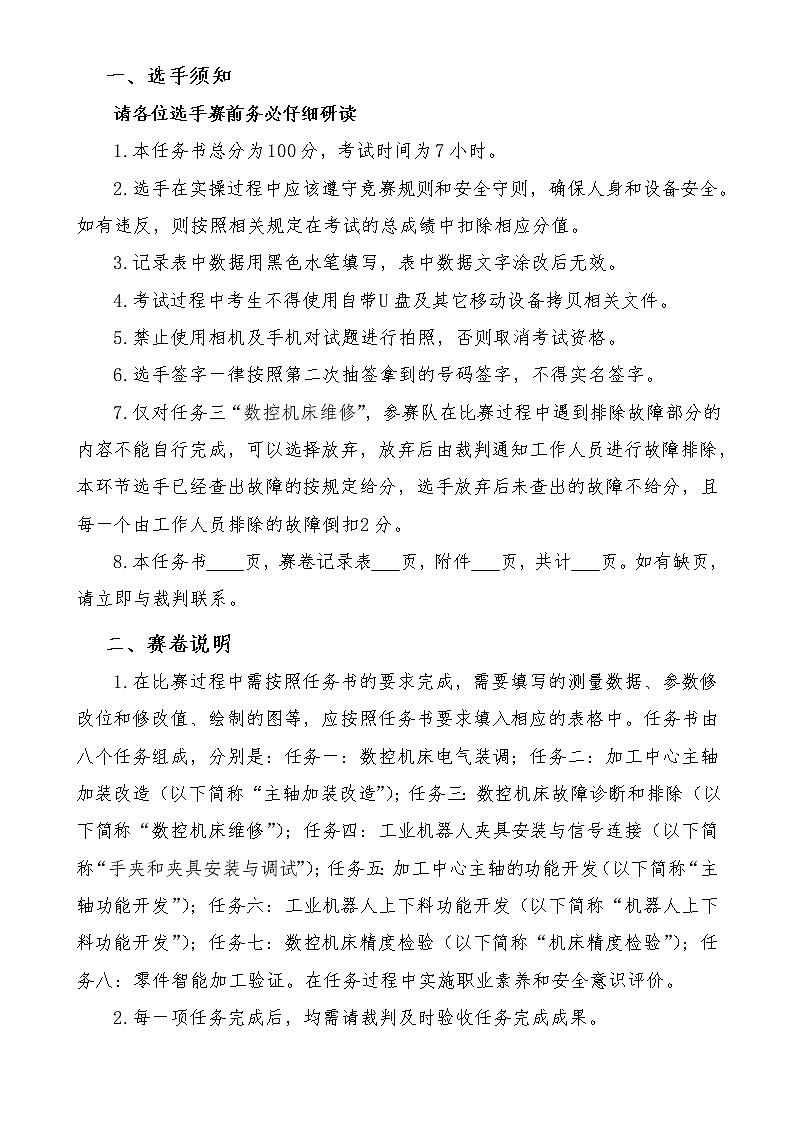
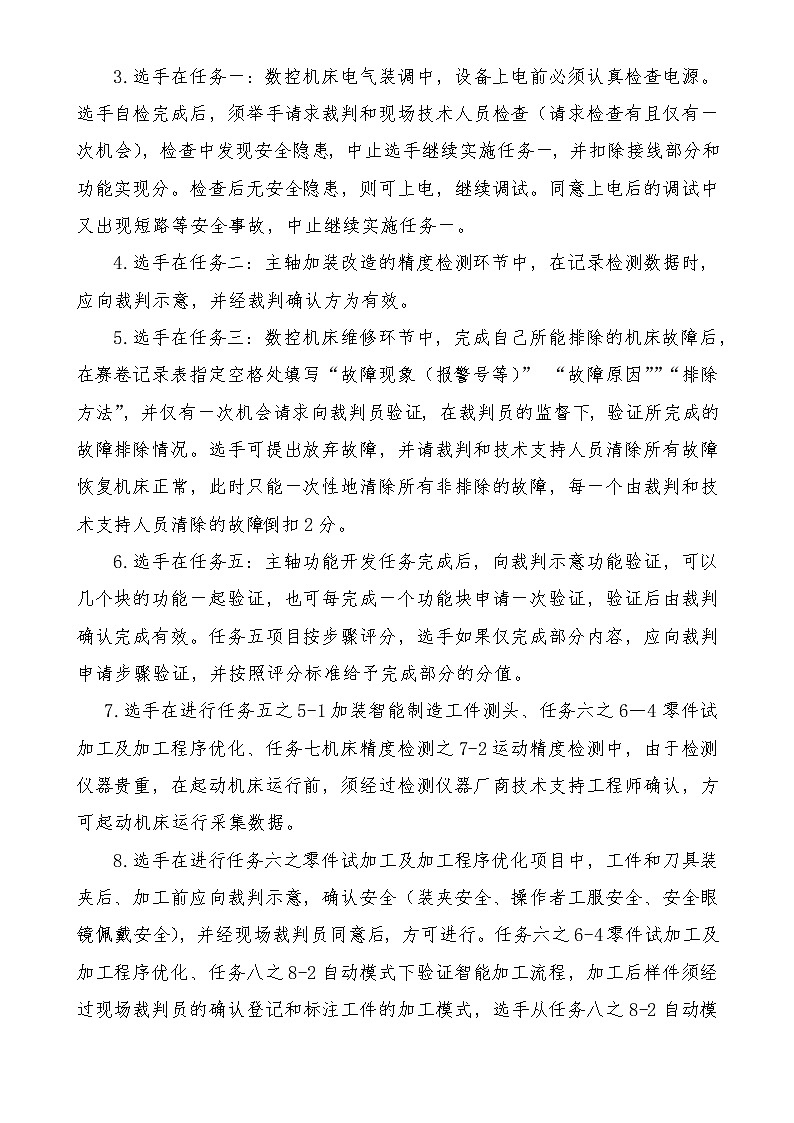
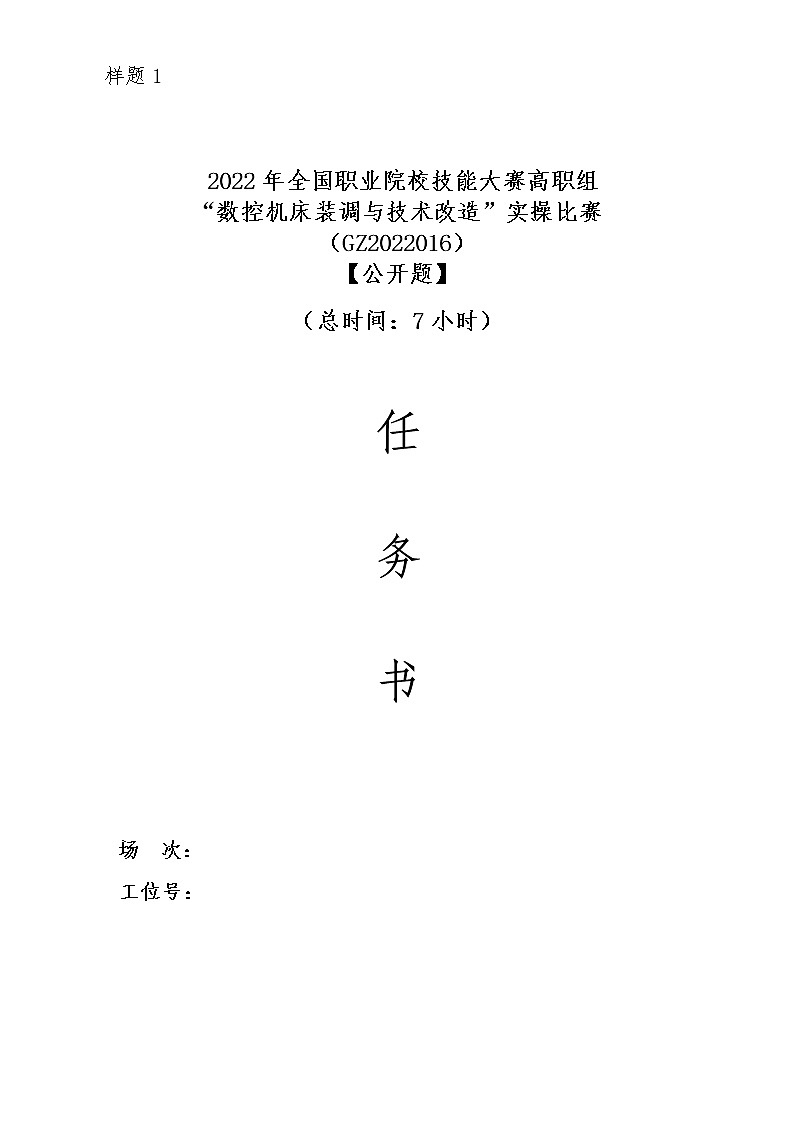
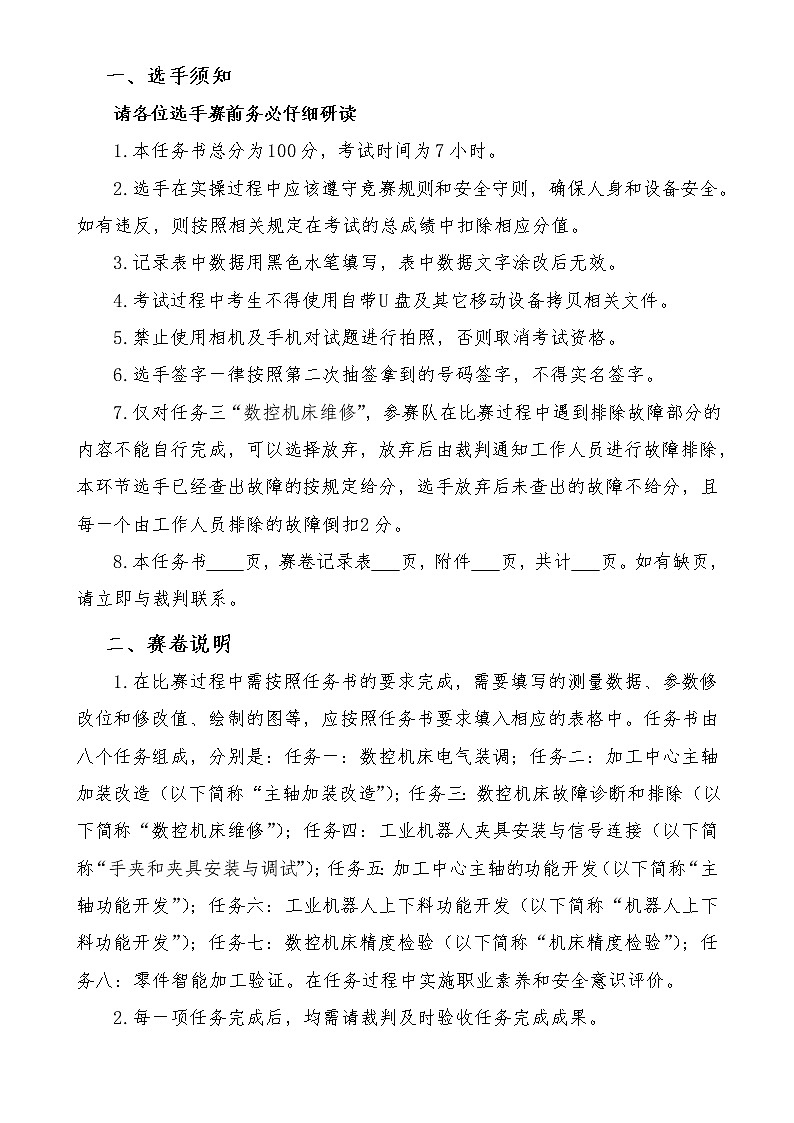
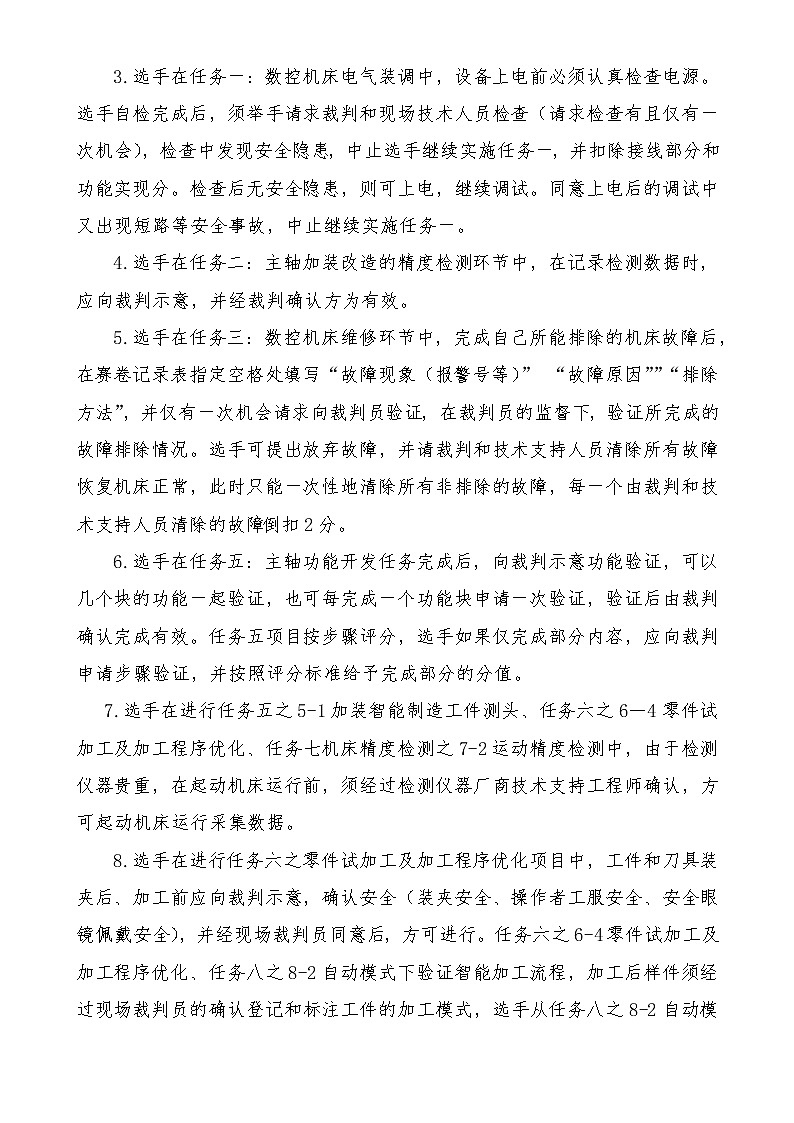
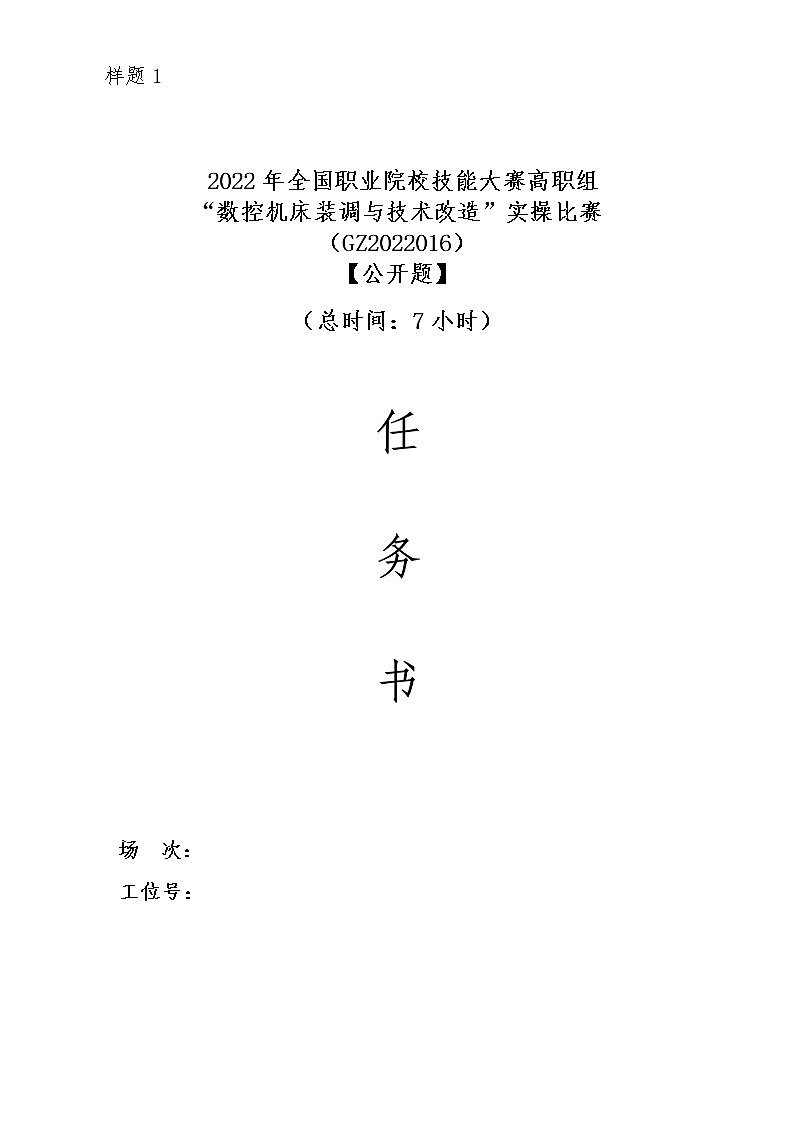

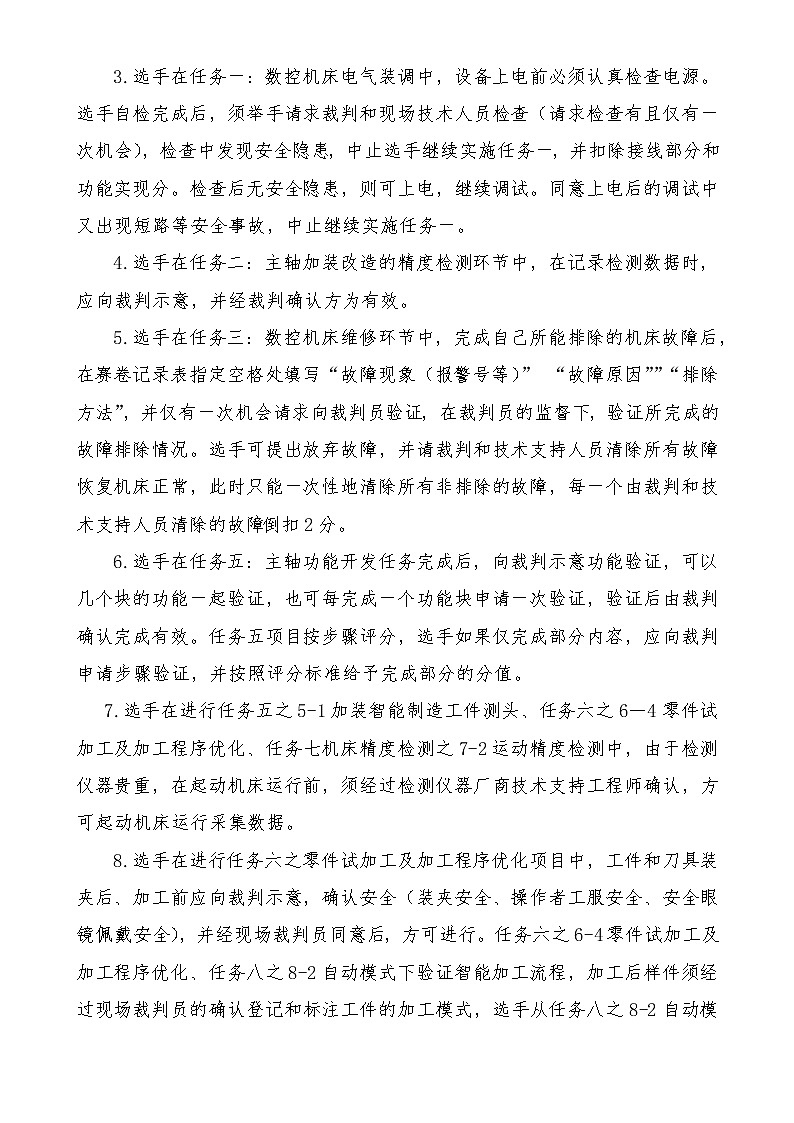
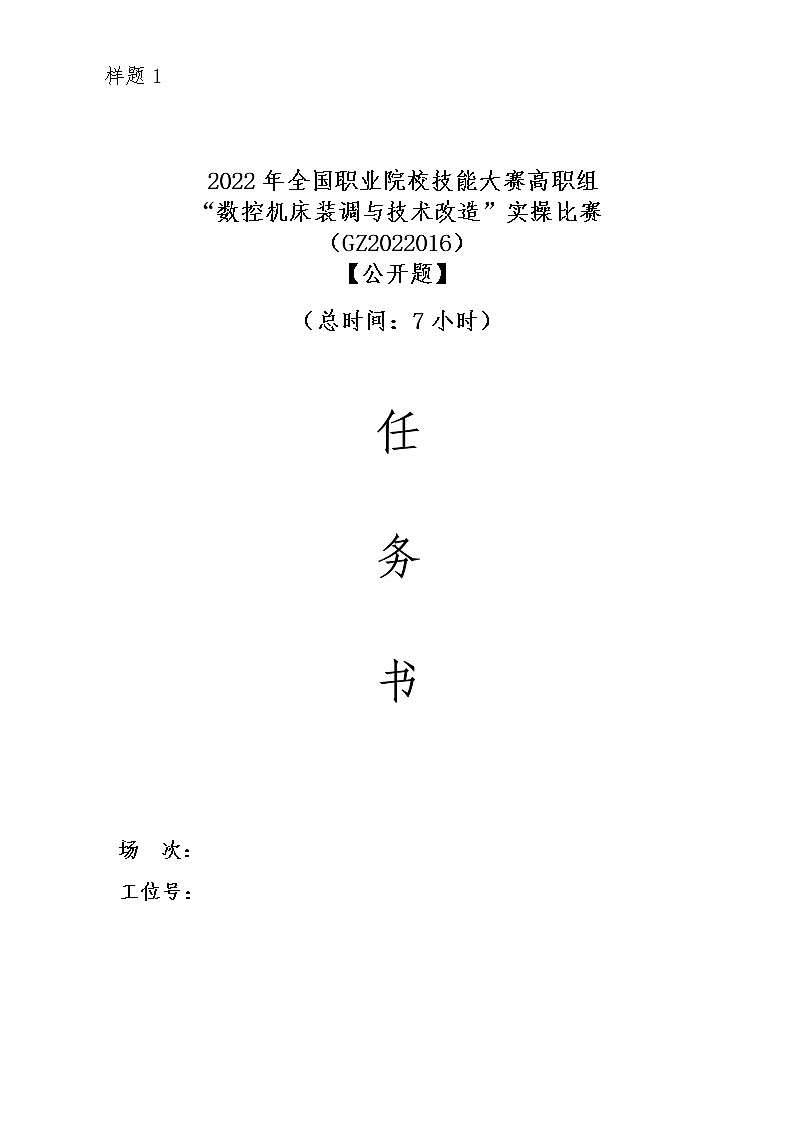
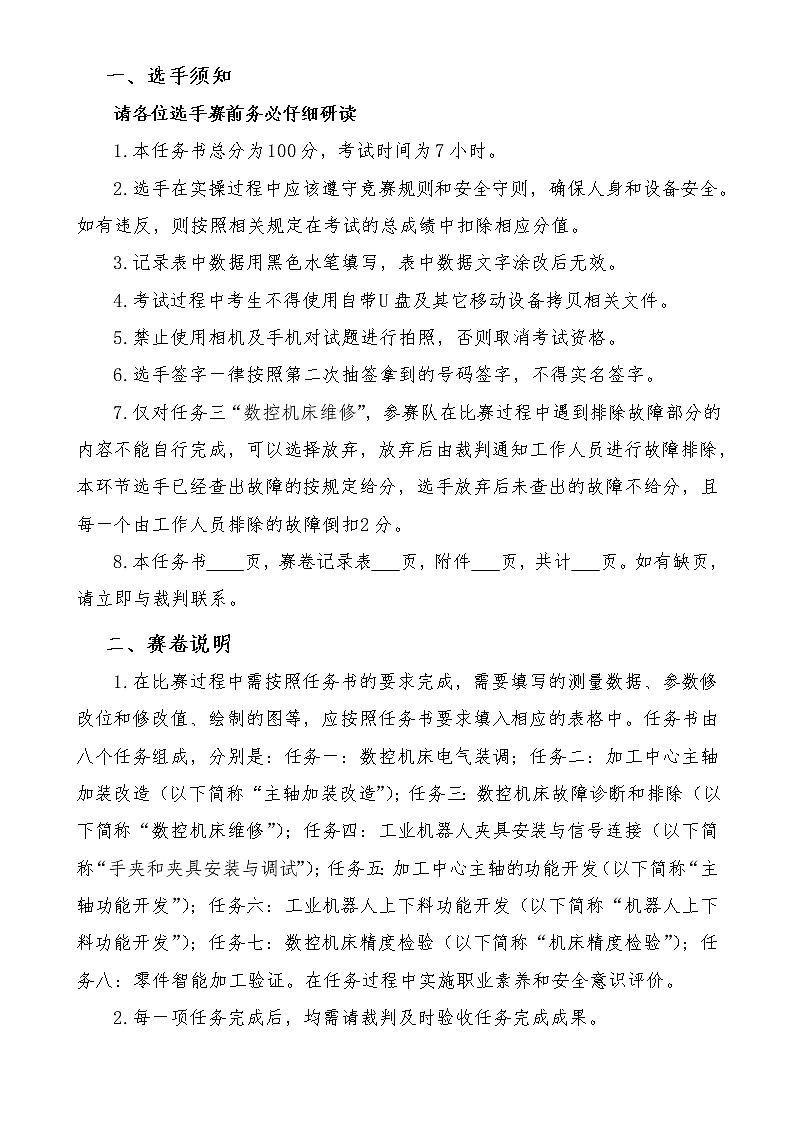
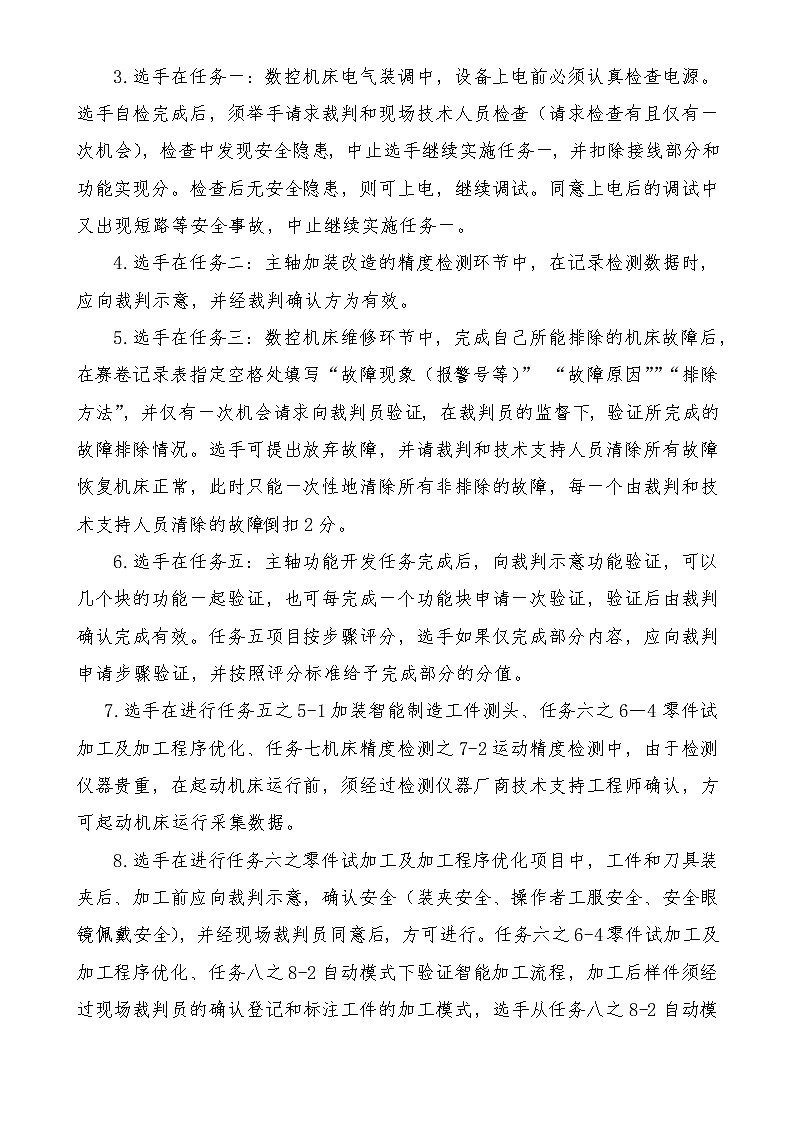
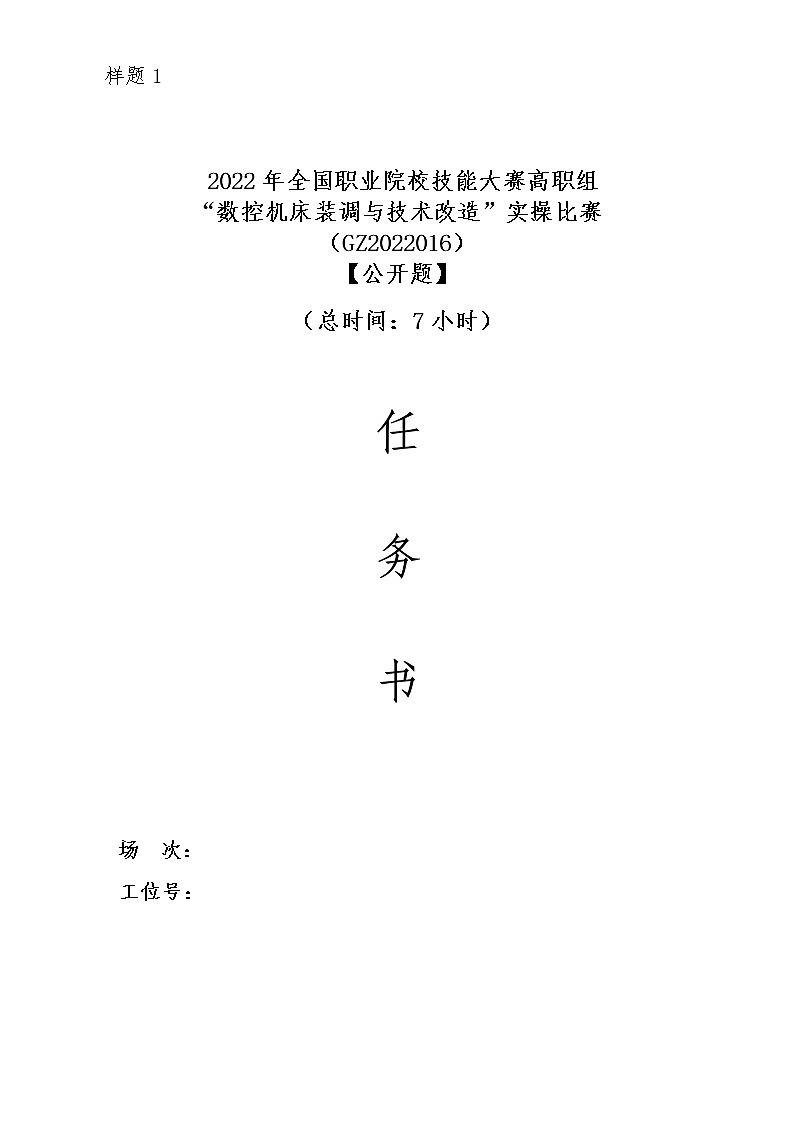
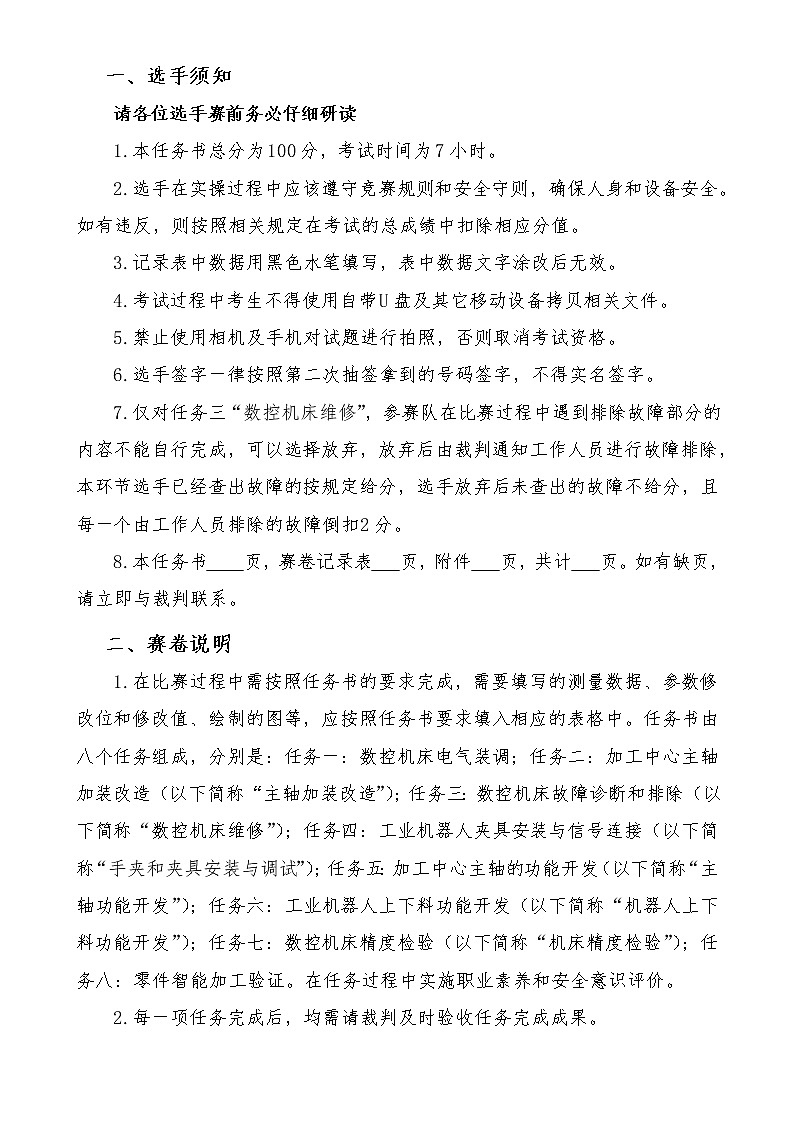
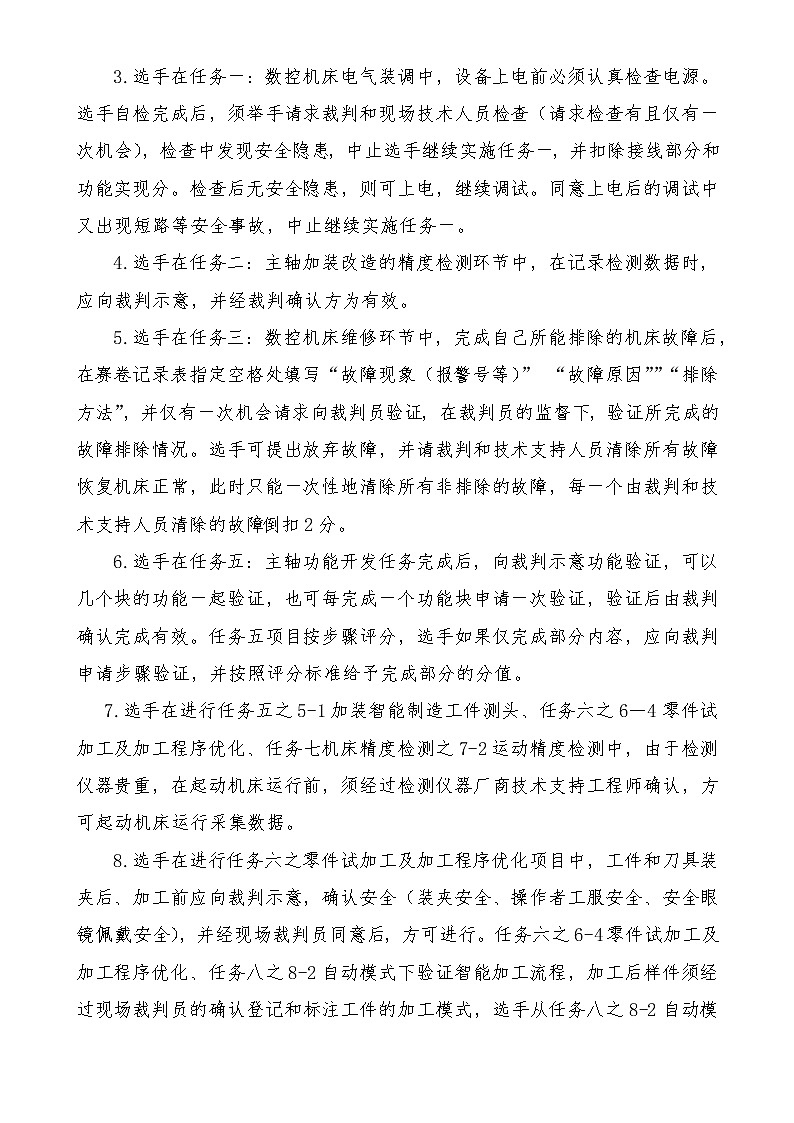
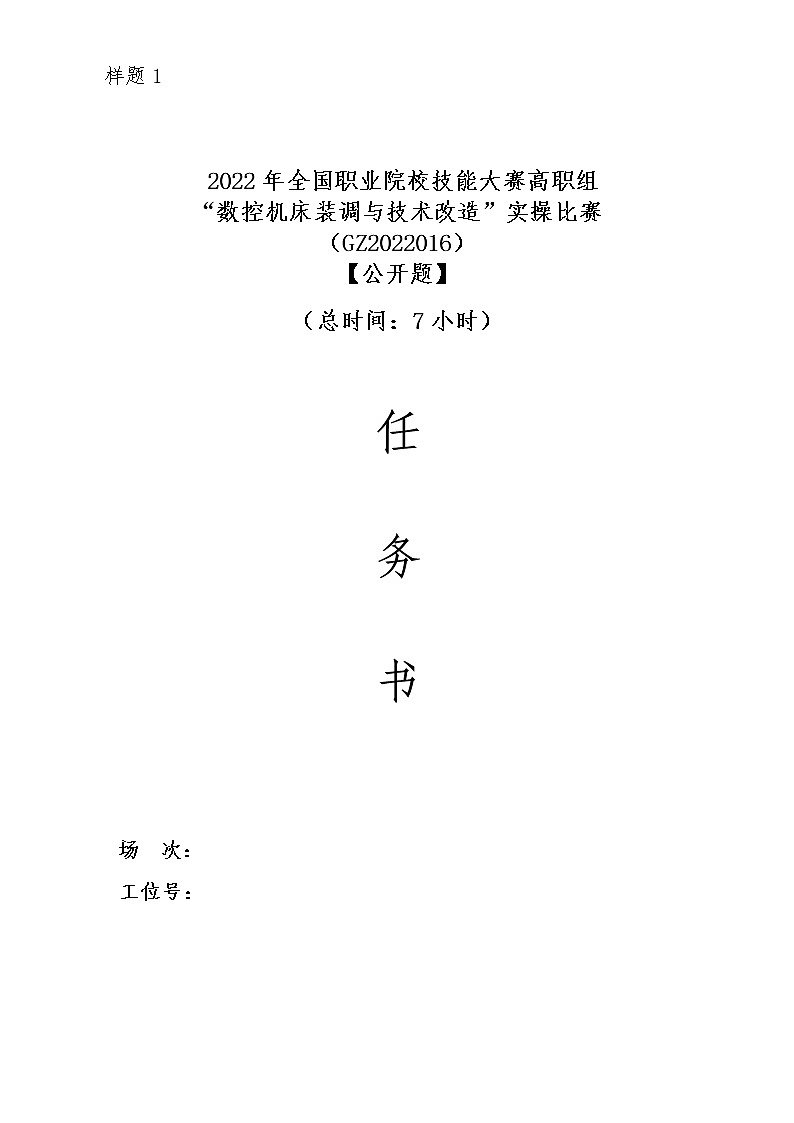
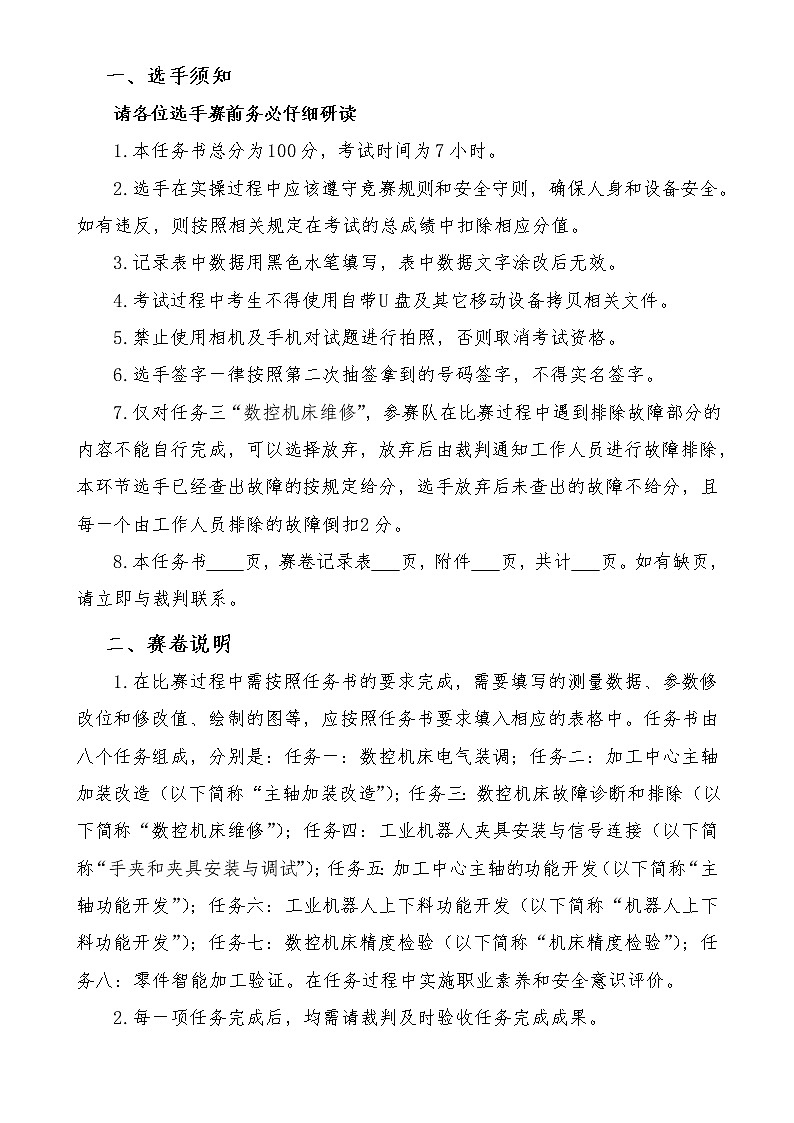

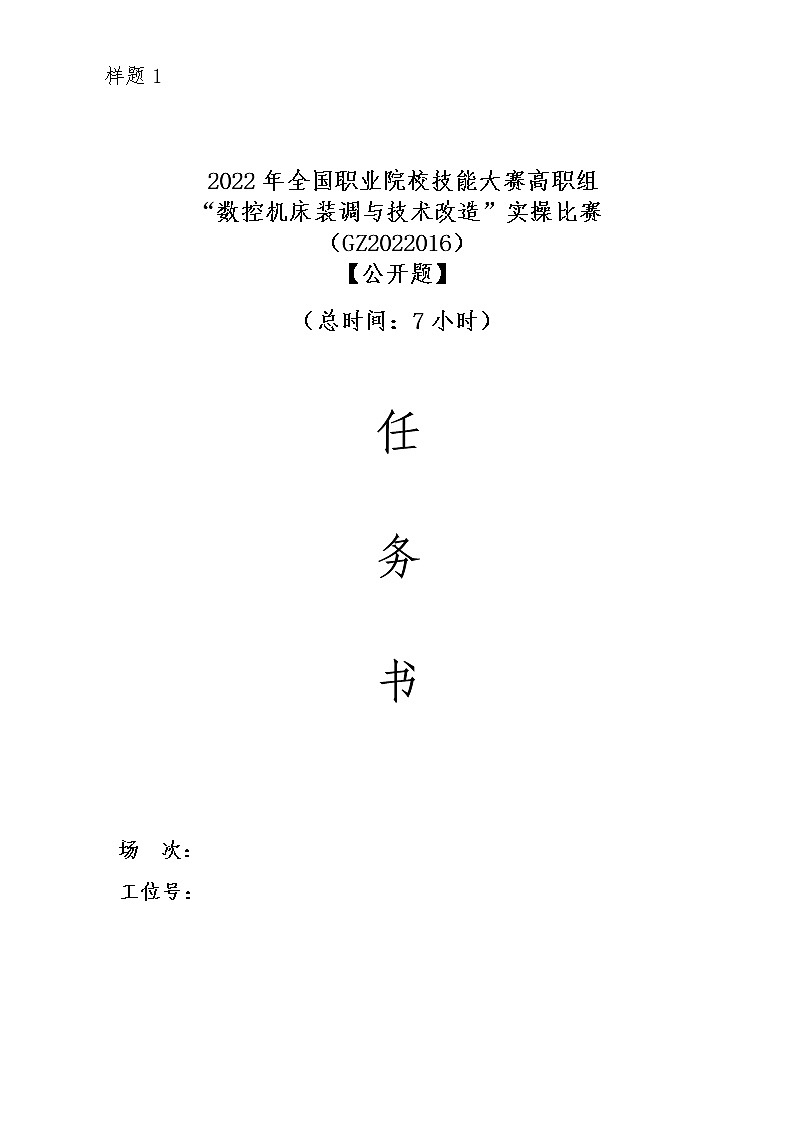
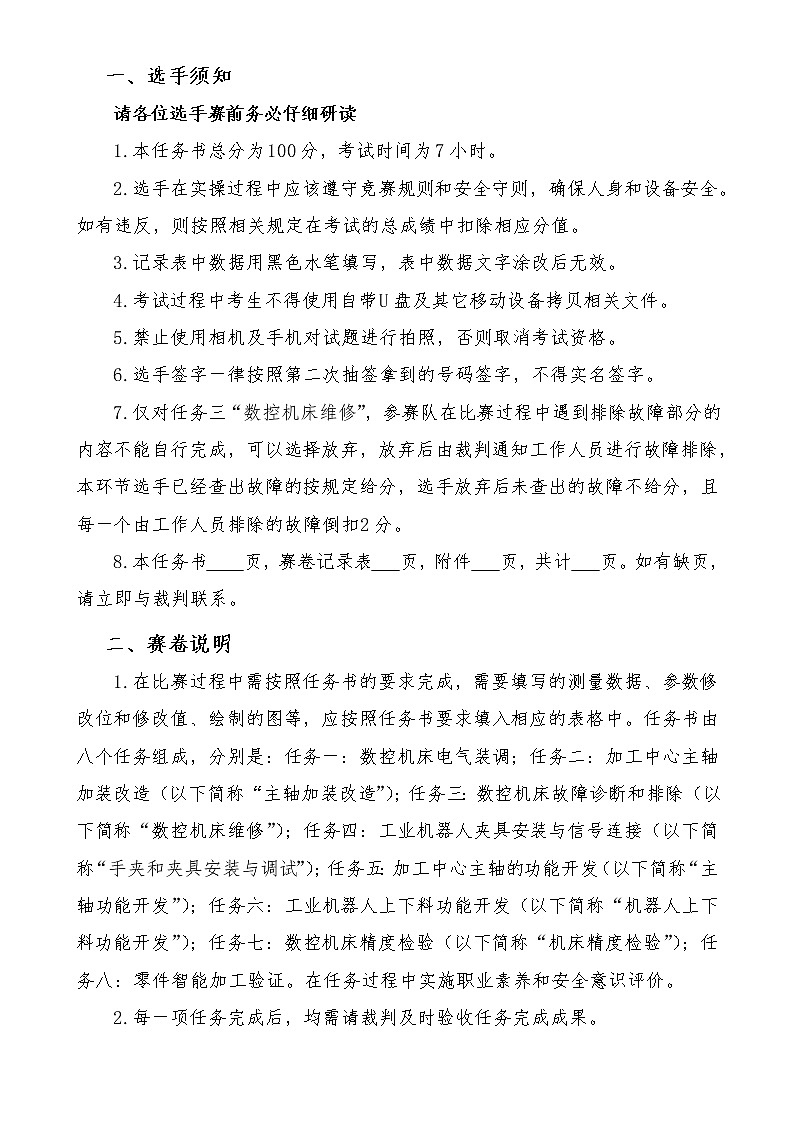
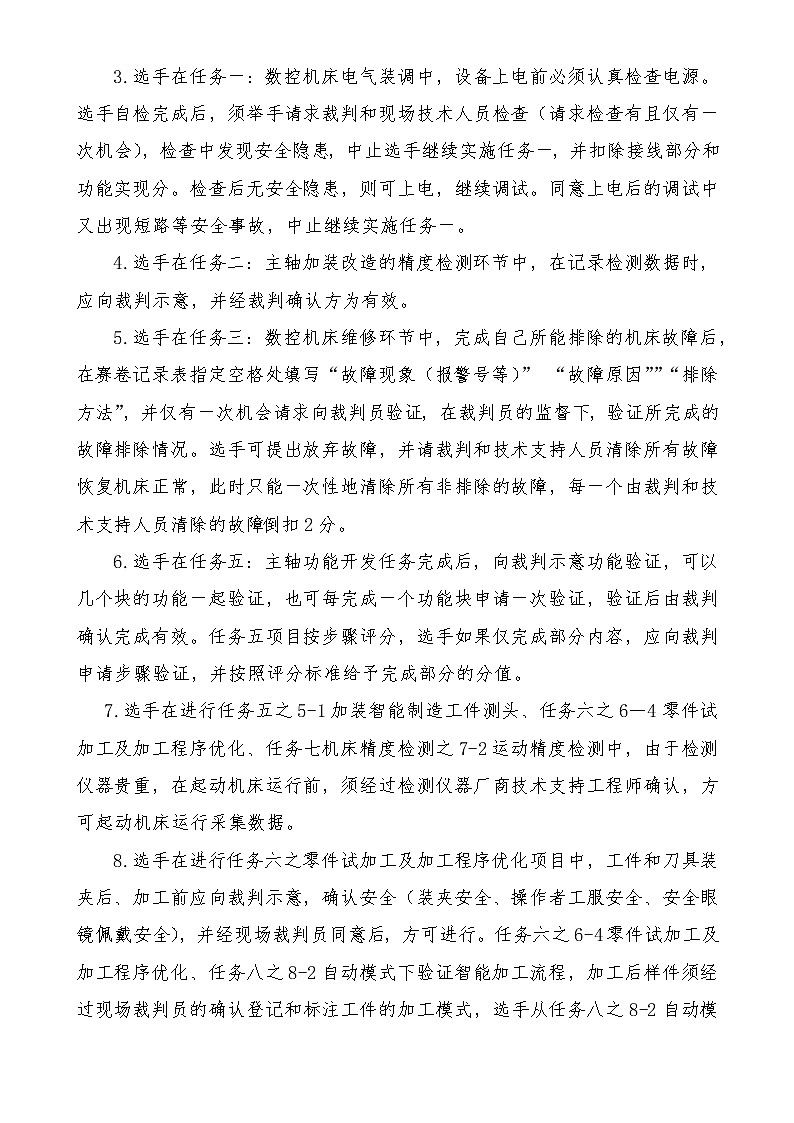
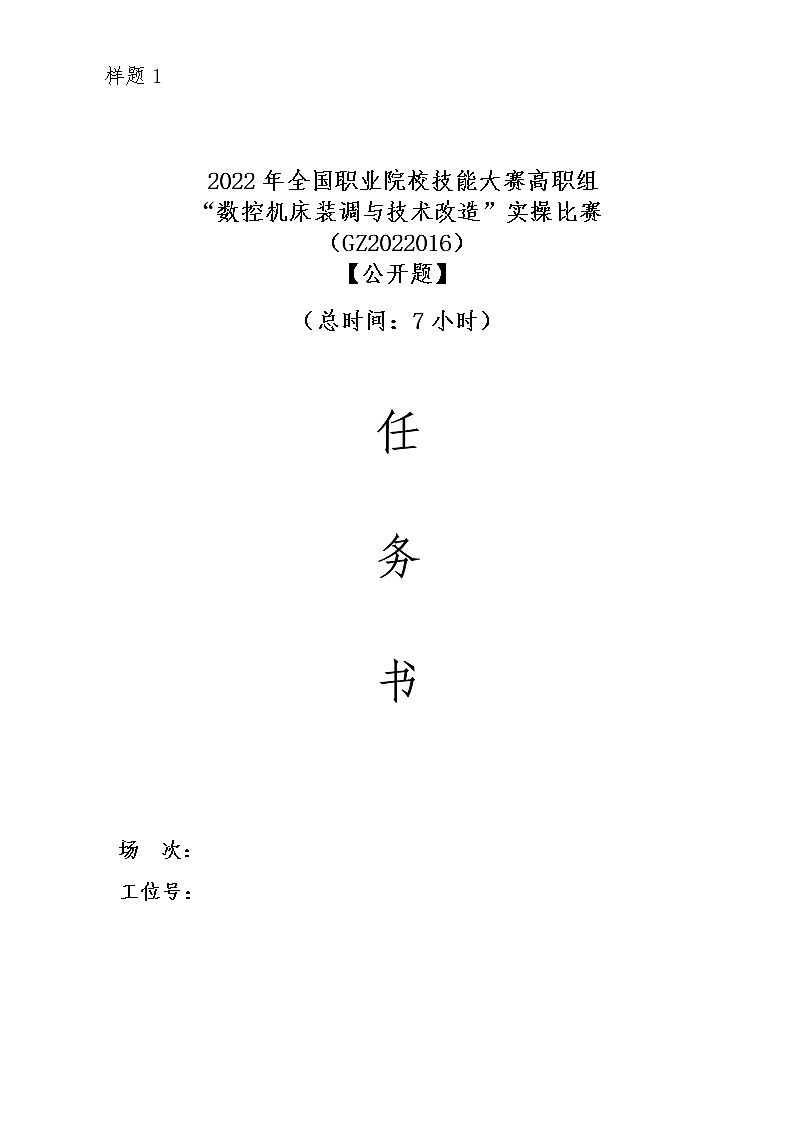
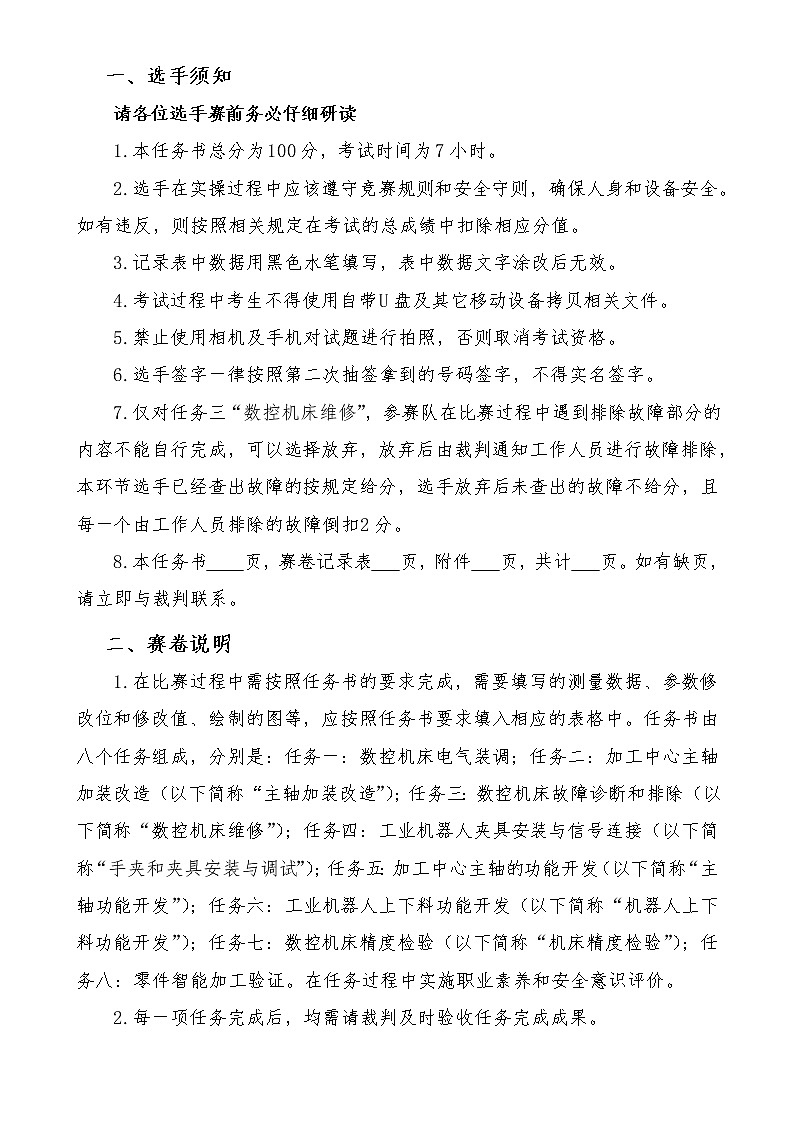
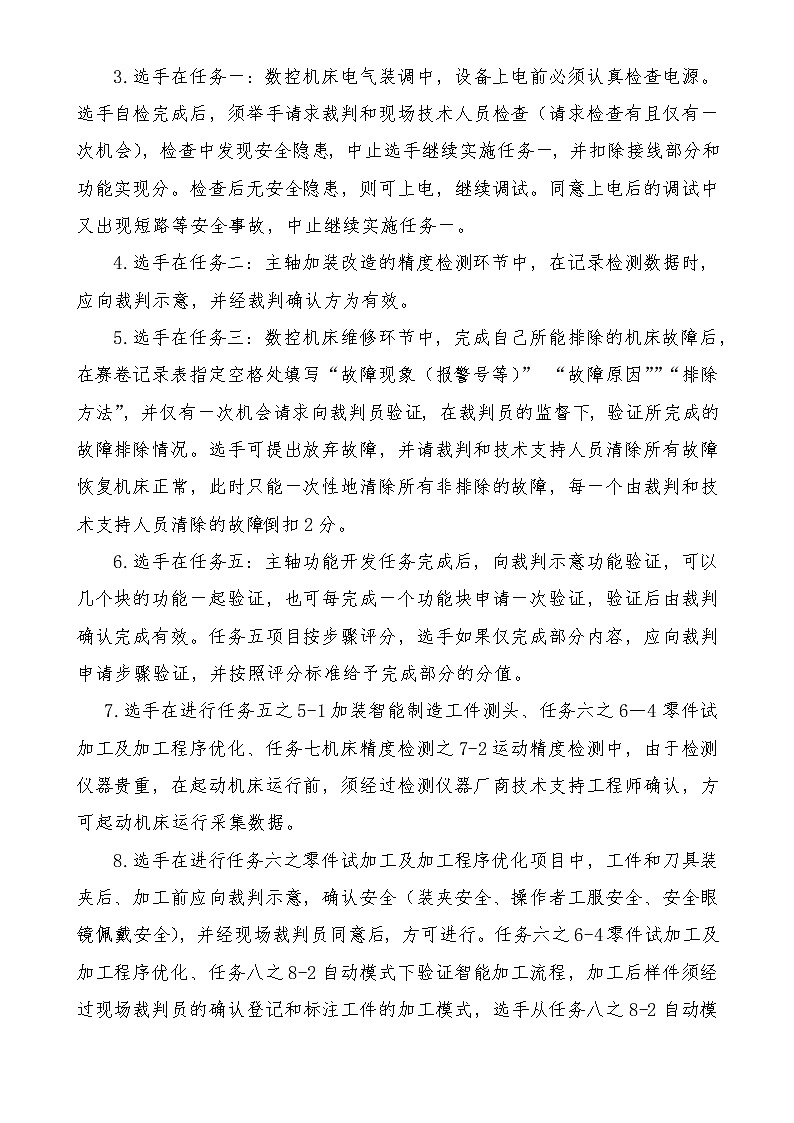
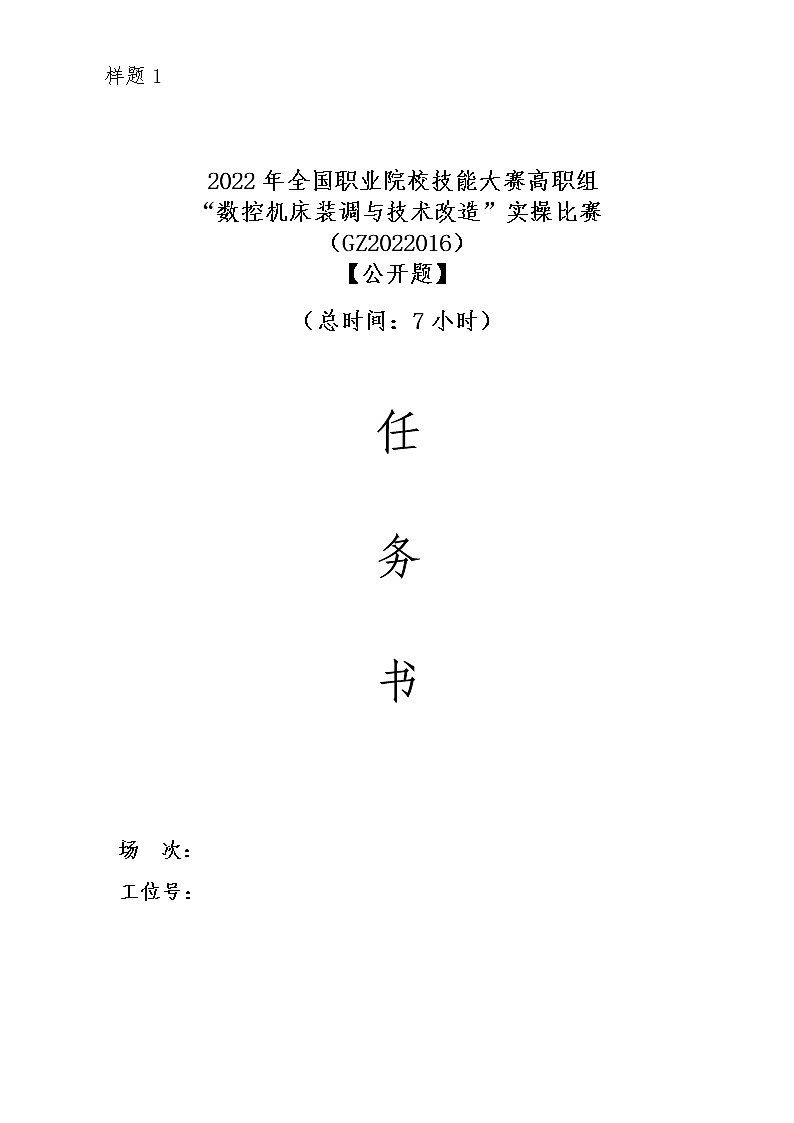
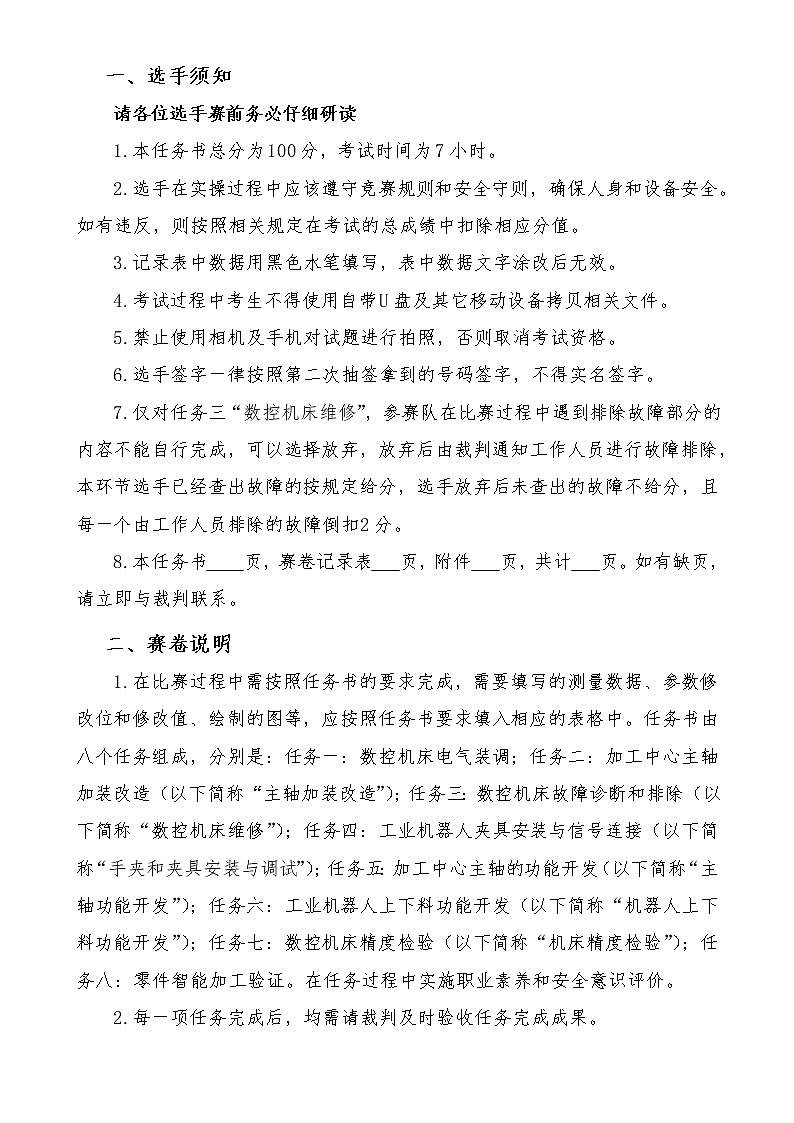
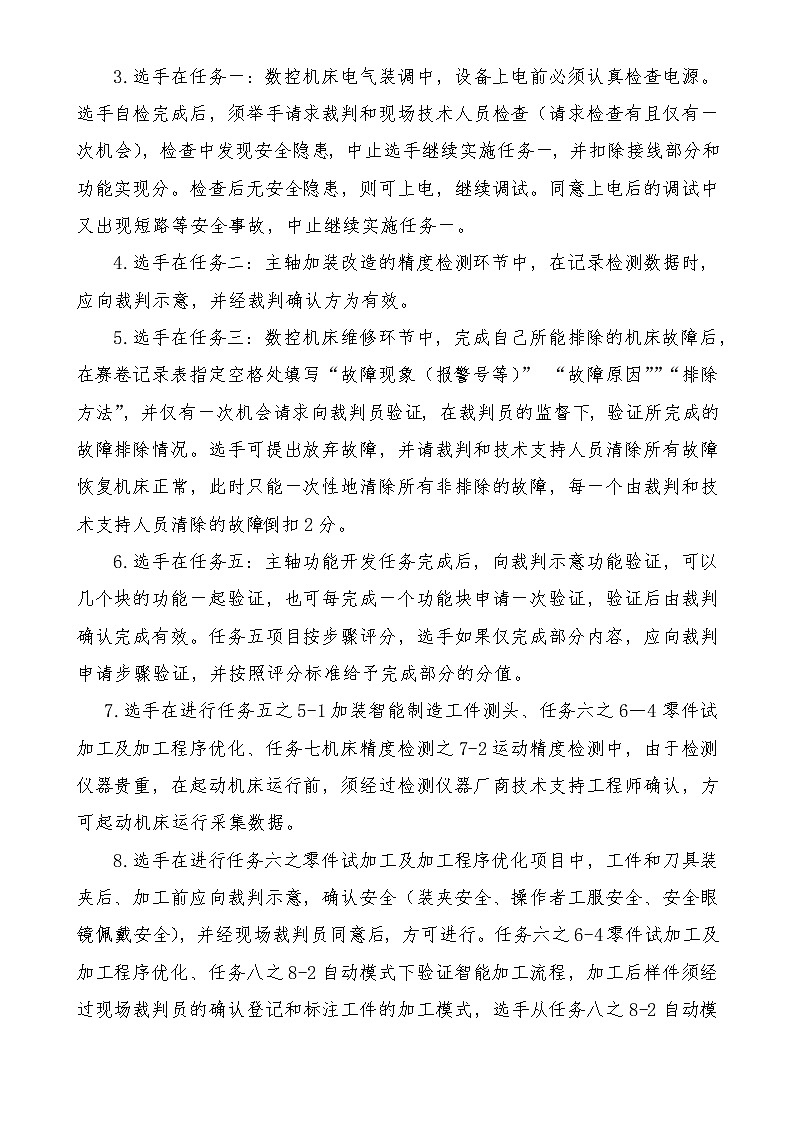
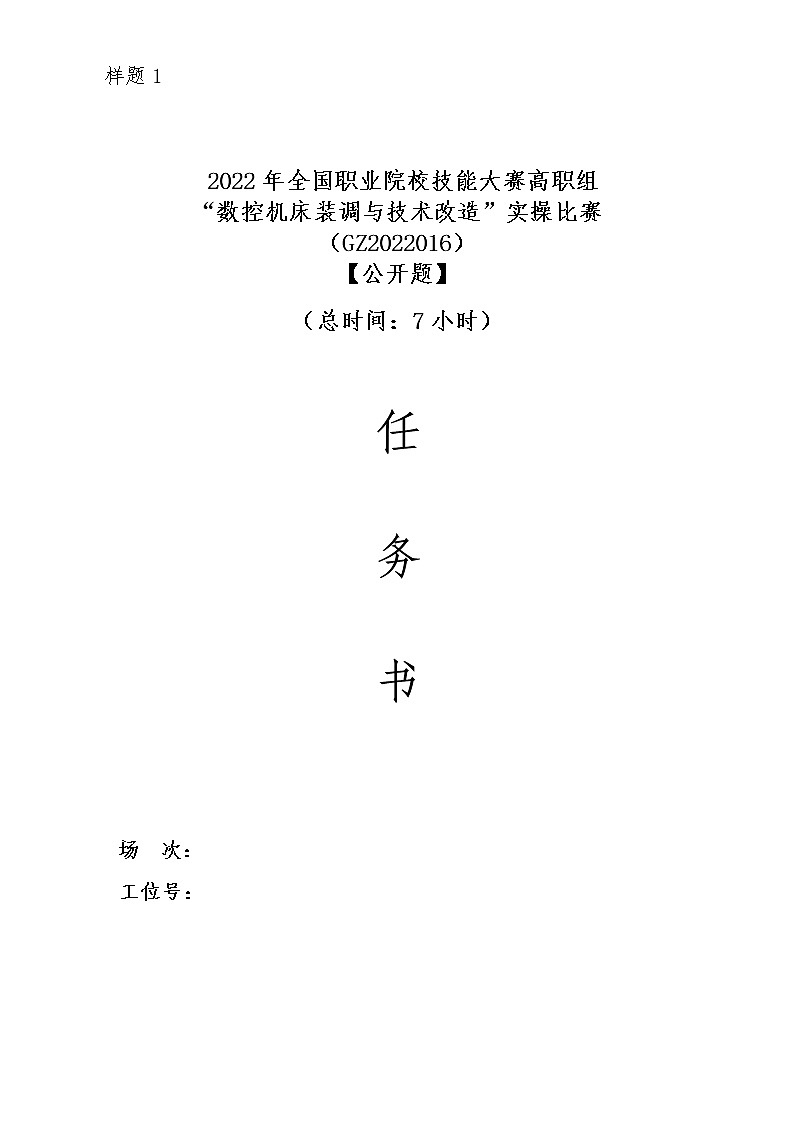
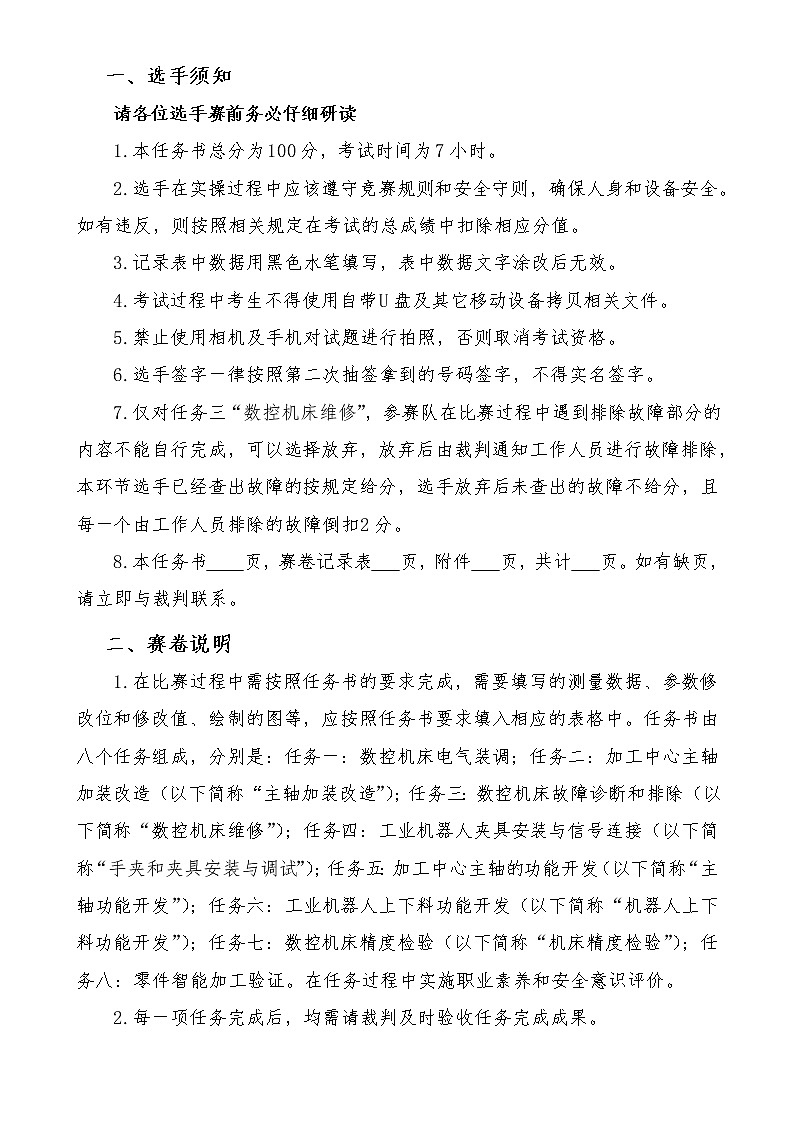
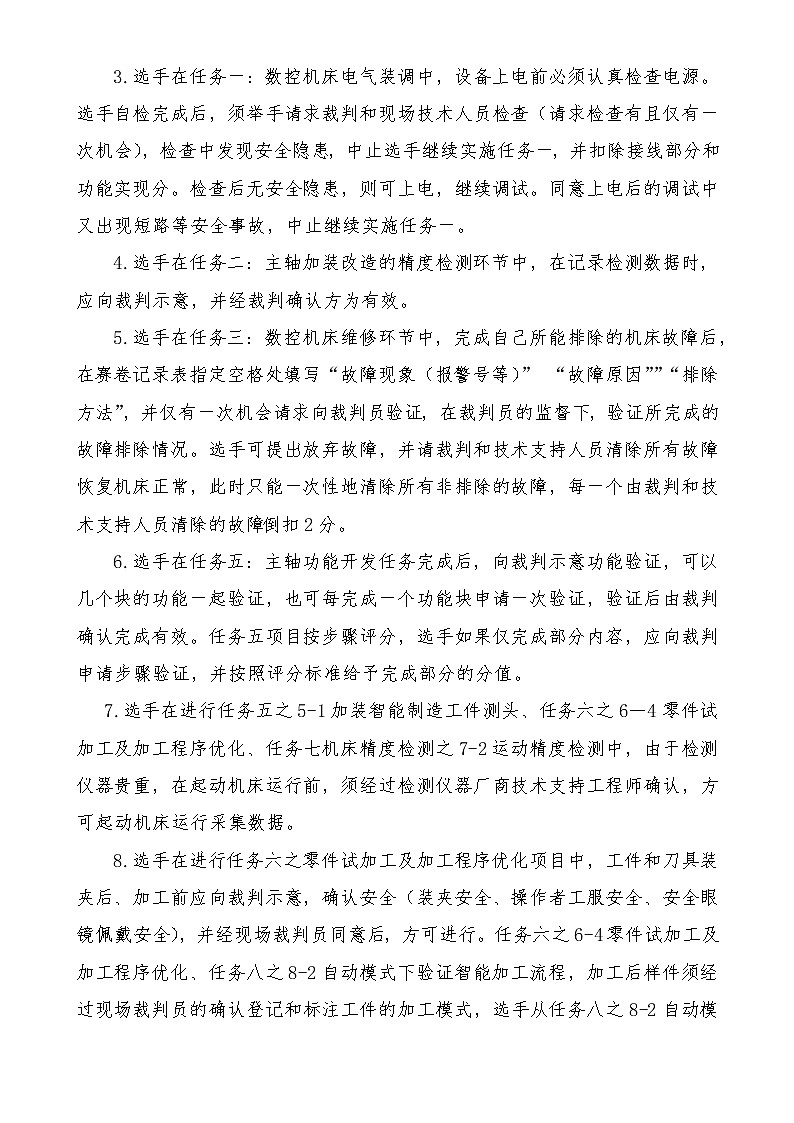
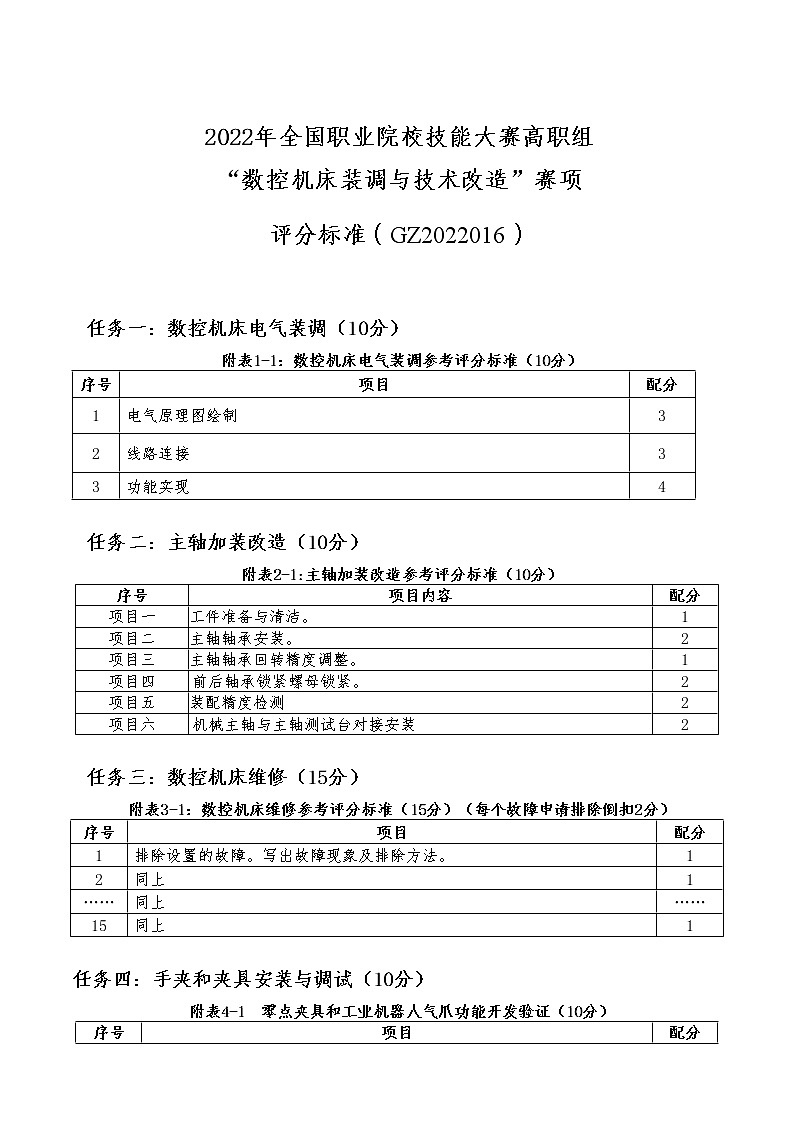
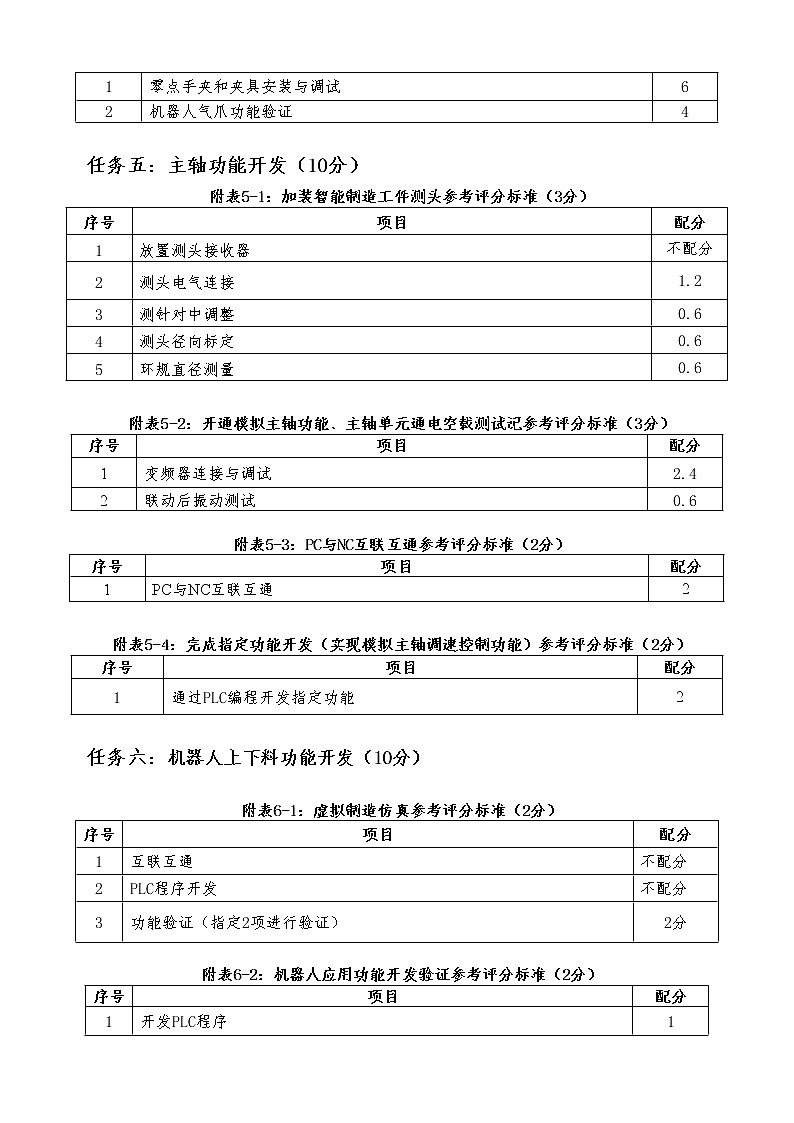
2022年全国职业院校技能大赛高职组 数控机床装调与技术改造赛项模拟赛题(Word版)
展开2022年全国职业院校技能大赛高职组
“数控机床装调与技术改造”实操比赛
(GZ2022016)
【公开题】
(总时间:7小时)
任
务
书
场 次:
工位号:
一、选手须知
请各位选手赛前务必仔细研读
1.本任务书总分为100分,考试时间为7小时。
2.选手在实操过程中应该遵守竞赛规则和安全守则,确保人身和设备安全。如有违反,则按照相关规定在考试的总成绩中扣除相应分值。
3.记录表中数据用黑色水笔填写,表中数据文字涂改后无效。
4.考试过程中考生不得使用自带U盘及其它移动设备拷贝相关文件。
5.禁止使用相机及手机对试题进行拍照,否则取消考试资格。
6.选手签字一律按照第二次抽签拿到的号码签字,不得实名签字。
7.仅对任务三“数控机床维修”,参赛队在比赛过程中遇到排除故障部分的内容不能自行完成,可以选择放弃,放弃后由裁判通知工作人员进行故障排除,本环节选手已经查出故障的按规定给分,选手放弃后未查出的故障不给分,且每一个由工作人员排除的故障倒扣2分。
8.本任务书 页,赛卷记录表 页,附件 页,共计 页。如有缺页,请立即与裁判联系。
二、赛卷说明
1.在比赛过程中需按照任务书的要求完成,需要填写的测量数据、参数修改位和修改值、绘制的图等,应按照任务书要求填入相应的表格中。任务书由八个任务组成,分别是:任务一:数控机床电气装调;任务二:加工中心主轴加装改造(以下简称“主轴加装改造”);任务三:数控机床故障诊断和排除(以下简称“数控机床维修”);任务四:工业机器人夹具安装与信号连接(以下简称“手夹和夹具安装与调试”);任务五:加工中心主轴的功能开发(以下简称“主轴功能开发”);任务六:工业机器人上下料功能开发(以下简称“机器人上下料功能开发”);任务七:数控机床精度检验(以下简称“机床精度检验”);任务八:零件智能加工验证。在任务过程中实施职业素养和安全意识评价。
2.每一项任务完成后,均需请裁判及时验收任务完成成果。
3.选手在任务一:数控机床电气装调中,设备上电前必须认真检查电源。选手自检完成后,须举手请求裁判和现场技术人员检查(请求检查有且仅有一次机会),检查中发现安全隐患,中止选手继续实施任务一,并扣除接线部分和功能实现分。检查后无安全隐患,则可上电,继续调试。同意上电后的调试中又出现短路等安全事故,中止继续实施任务一。
4.选手在任务二:主轴加装改造的精度检测环节中,在记录检测数据时,应向裁判示意,并经裁判确认方为有效。
5.选手在任务三:数控机床维修环节中,完成自己所能排除的机床故障后,在赛卷记录表指定空格处填写“故障现象(报警号等)” “故障原因””“排除方法”,并仅有一次机会请求向裁判员验证,在裁判员的监督下,验证所完成的故障排除情况。选手可提出放弃故障,并请裁判和技术支持人员清除所有故障恢复机床正常,此时只能一次性地清除所有非排除的故障,每一个由裁判和技术支持人员清除的故障倒扣2分。
6.选手在任务五:主轴功能开发任务完成后,向裁判示意功能验证,可以几个块的功能一起验证,也可每完成一个功能块申请一次验证,验证后由裁判确认完成有效。任务五项目按步骤评分,选手如果仅完成部分内容,应向裁判申请步骤验证,并按照评分标准给予完成部分的分值。
7.选手在进行任务五之5-1加装智能制造工件测头、任务六之6-4零件试加工及加工程序优化、任务七机床精度检测之7-2运动精度检测中,由于检测仪器贵重,在起动机床运行前,须经过检测仪器厂商技术支持工程师确认,方可起动机床运行采集数据。
8.选手在进行任务六之零件试加工及加工程序优化项目中,工件和刀具装夹后、加工前应向裁判示意,确认安全(装夹安全、操作者工服安全、安全眼镜佩戴安全),并经现场裁判员同意后,方可进行。任务六之6-4零件试加工及加工程序优化、任务八之8-2自动模式下验证智能加工流程,加工后样件须经过现场裁判员的确认登记和标注工件的加工模式,选手从任务八之8-2自动模式下验证智能加工流程中加工的2件零件中选择1件,由裁判封存送检。
9.本任务书包括八项技术内容,配分如下:
任务一:数控机床电气装调(10分)。
任务二:主轴加装改造(10分)。
任务三:数控机床维修(15分)。
任务四:手夹和夹具安装与调试(10分)。
任务五:主轴功能开发(10分)
任务六:机器人上下料功能开发(10分)
任务七:机床精度检验(10分)。
任务八:零件智能加工验证(15分)。
九:职业素养和安全意识(10分)。
三、实操工作任务
任务一:数控机床电气装调(10分)
题目:立式加工中心三色灯之黄灯显示功能的设计、接线及调试。
根据现场提供的器件、工具等,完成: = 1 \* GB3 ①在表1-1中绘制绿灯显示功能电气原理图; = 2 \* GB3 ②按绘制的电气原理图,完成接线; = 3 \* GB3 ③验证三色灯之黄灯显示功能。任务过程中的相关结果记入表1-1,本项任务完成后,按表1-1中的项目内容,请裁判验收任务成果。
表1-1:数控机床电气装调记录表
序号
项目
项目内容
1
电气原理图绘制
器件选择数量正确合理
原理图绘制正确,科学合理,符合要求/
图形符号规范,标注齐全
保护环节设计得当
字迹清楚、整洁、美观
2
线路连接正确
元件安装位置合理,紧固不松动,工具使用合理
线上号码管安装规范,与电气原理图相符
接至板外的导线经端子排转接,端子排上一个接点接一根线,且端子与端子之间留有空端子
所有导线进走线槽,或进行了捆束
3
功能实现
功能实现结果验证
(学生填写,裁判签字确认)
选手绘制的电气原理图(空白不够时可以画背面):
注意:选手在设备上电前需自行检查所连接线路的正确性,并经裁判和现场技术人员检查无误后方可通电运行。当技术人员或裁判发现错误连接导致电源或负载短路、以及导致设备损坏或人员安全问题时,中止选手继续实施本任务。技术人员确认可以上电后,将指出若干条已接线正确的接线,在后续的通电调试过程中,选手不可改接已确认正确的接线。技术人员确认正确的接线的连接牢靠性和接线规范性由选手自行负责。参赛队有且仅有一次,请裁判和现场技术人员检查是否可以上电的机会,经检查确认后,后续的断电和通电调试不再请现场裁判和现场技术人员检查确认是否可以上电。
任务二:主轴加装改造(10分)
题目:主轴的装配、检测与调整。
本任务共分六个项目。 = 1 \* GB3 ①工件准备与清洁; = 2 \* GB3 ②主轴轴承安装; = 3 \* GB3 ③主轴轴承回转精度调整; = 4 \* GB3 ④前后轴承锁紧螺母锁紧; = 5 \* GB3 ⑤实测主轴套筒端面到主轴套隔台的长度K1值,实测叠加放置高度K2值,实测主轴前端盖凹台深度数值H,计算主轴前端盖压紧量A,以及检测主轴锥孔跳动值△s; = 6 \* GB3 ⑥机械主轴与主轴测试台对接安装(参见下图,正式赛卷中按实际给出正式图)。
完成过程中的相关数据记入表2-1中,请裁判验收各个项目任务的完成成果。所涉主轴总装图及其主轴零件明细表由赛场提供。
表2-1:主轴加装记录表
任务三:数控机床维修(15分)
故障排查涉及立式加工中心技术指标(将在正式赛题中给出)、系统参数、伺服参数及PLC程序,最终以解除报警、准确实现功能动作为完成任务。比赛开始前,本赛位上应张贴有技术平台在赛前完成的《故障清除确认表》《故障设置完成签字表》及机床准备封条。选手确认齐全后,揭封,并在封条上签字确认。
要求:
1.根据表3-1第三列“技术指标检验标准”,排除故障现象。
2.将每一个已排除故障的现象、故障原因及修正参数写入表3-2:数控机床维修记录表中,并向裁判报告,请求裁判签字确认故障排除的工作成果。当申请裁判和技术人员恢复机床时,每一个未排除的故障倒扣2分。
3.选手不得全部清除数控系统数据和梯形图。一经发现,按要求排除全部故障的情形计分。
表3-1 故障检查事项表
表3-2 数控机床维修记录表
任务四:手夹和夹具安装与调试(10分)
根据赛场提供的机床气路图以及传感器,设计夹具气路图和传感器连接图,完成表4-1中, = 1 \* GB3 ①手夹和夹具安装与调试; = 2 \* GB3 ②机器人气夹功能验证。
附表4-1 夹具和工业机器人气爪功能开发验证
任务五:主轴功能开发(10分)
根据赛项提供的测头、主轴部件。利用机床数控系统,完成: = 1 \* GB3 ①智能制造工件测头; = 2 \* GB3 ②开通模拟主轴功能、主轴单元通电空载测试; = 3 \* GB3 ③ PC机与CNC互联互通; = 4 \* GB3 ④完成指定功能的开发。
5-1.加装智能制造工件测头
根据所提供的测头,按照表5-1工件测头加装项目表中第三列要求,完成各项任务。每一个项目任务完成后均需请裁判验收任务完成成果。
表5-1 加装智能制造工件测头项目
5-2 开通模拟主轴功能、主轴单元通电空载测试
根据任务二装配好的机械主轴和异步电机,在本节中根据赛场提供的变频器技术资料连接变频器,并通过机床MDI或操作面板备用键控制主轴分别旋转200 rpm,500rpm,800rpm进行测试。具体要求: = 1 \* GB3 ①完成数控系统模拟接口→变频器→三相异步电机的硬件连接; = 2 \* GB3 ②完成数控系统模拟接口功能开通(数控系统侧参数设置、PLC编辑); = 3 \* GB3 ③变频器参数设置; = 4 \* GB3 ④主轴旋转时测试机械主轴震动。选手依据表5-2,在任务完成过程中或任务完成后,请裁判验收任务成果。
表5-2:开通模拟主轴功能、主轴单元通电空载测试记录表
选手压接端子、标注线号(现场提供线号管)、接线参见正式赛卷提供的端子图。
5-3.PC机与NC互联互通
根据现场提供设备接口和以太网线,实现PC机与CNC(数控系统)的连接。系统与PC机联通中,要求检查在数控系统端操作,可将PC上的程序文件复制到数控系统。选手在任务完成后,根据表5-3,请裁判验收任务完成成果。
表5-3:PC与NC互联互通
5-4.完成指定功能开发(6分)
利用富余的M指令,开发PLC程序,以及参数设置,实现:
(1)通过MDI键盘输入S指令、M指令控制主轴正/反转。
(2)通过机床操作面板备用键(参照表5-4)作为“主轴正转”、“主轴反转”、“增速按钮”、“减速按钮”、“主轴停止”,按下哪个键后,其对应的按钮LED点亮,通过增速/减速按钮每按一次增/减速10%。
(3)模拟主轴指令推荐见表5-5。
(4)选手根据表5-6:完成指定功能开发(实现模拟主轴调速控制功能)后,请裁判验收任务完成成果。
表5-4 备用键对应的输入和输出地址
表5-5 模拟主轴指令推荐
表5-6 完成指定功能开发(实现模拟主轴调速控制功能)
任务六:机器人上下料功能开发(10分)
根据赛项提供的智能加工仿真软件、机器人及控制系统、数控机床及其富余的M指令等,开发PLC程序。完成: = 1 \* GB3 ①机器人应用功能仿真; = 2 \* GB3 ②机器人应用功能开发; = 3 \* GB3 ③机器人上料编程; = 4 \* GB3 ④零件试加工及加工程序优化; = 5 \* GB3 ⑤机器人上料编程。
6-1 机器人应用功能仿真。选手使用赛场提供的仿真软件,根据虚拟制造仿真流程图(图6-1。正式流程图待虚拟制造仿真软件确定后给出)。完成上料动作PLC的编写。
图6-1 虚拟制造仿真流程图
根据表6-1,指定2项功能进行虚拟仿真验证。
表6-1:虚拟制造仿真记录表
6-2 机器人应用功能开发。开发PLC程序,实现在 MDI 和单步方式下,使用机器人信号输出实现自动门开关,以及自动门开关的安全联锁,智能加工区安全围栏上安全门的安全联锁功能。
附表6-2:机器人应用功能仿真记录表(2分)
6-3 机器人上下料编程。示教编程实现上料时机器人对第1件毛坯抓取,并放置到加工中心夹具中,实现夹紧,以及机器人退出加工位置。示教编程实现下料时机器人对夹具上的工件的抓取,配合夹具的松开,机器人将工件施加到毛坯库1位置。表6-3功能全部实现后,请裁判验证任务完成成果(有,且仅有一次验证机会)。
附表6-3:机器人示教编程记录表(2分)
6-4 零件试加工及加工程序优化。在机器人退出加工位置后,选手依据GB/T-20957.7-2007《精密加工试件》标准,按照赛项任务书的图纸要求(图6-1,该件毛坯为一块方料,其中707020段为夹具夹持部位,事先已加工成形,具体的毛坯外形待机床招标完成后确定并公布),对机械人上料的1件毛坯进行试切件加工及进行在线测量,毛坯安装在夹具上必须由机器人完成,零件真实加工过程可由人工干预。加工过程中按表6-4进行工件在线测量,测量过程及结果请裁判验收。根据测量结果,通过刀补对加工程序进行优化,为零件的智能加工作准备。
附表6-4:工件在线测量参考评分标准(2分)
本项目注意事项:
(1)安装在线测头,启动检测程序,调用圆检测宏指令,检测加工后的圆直径。检测结果通过程序赋值到宏变量#XXX中。
(2)本环节不提供CAD/CAM软件,要求计算机G代码编程,通过数控机床企业提供的程序将加工程序传送至CNC。请根据现场提供的图纸,用G代码编程,完成试切件轮廓的加工。
序号
项目内容
项目一
工件准备与清洁。在零件摆放区的主轴零部件进行清点、核对,并按照正确的工艺步骤清洁,按照安装工艺步骤将零部件整齐码放到装配区,如发现零部件上有毛刺,按照正确的工艺方法去除毛刺。
项目二
前主轴轴承安装:根据主轴安装工艺要求安装主轴轴承,正确选择轴承安装方向,轴承组对形式正确。测量并调整外圆与主轴同心。
项目三
主轴轴承回转精度调整:测量和调整前轴承外环与主轴后轴承轴径接触外圆之间回转跳动,选手将测量结果填入下式(请裁判签字确认):
△r= mm,
检验前轴承外环端面跳动
△a= mm
项目四
前后轴承锁紧螺母锁紧。选手确认轴承系轴向预紧完成后,请填写如下数据,在力矩扳手调至前轴承预紧力矩值时,请裁判签字确认(仅验证选手掌握力矩扳手的调整和使用):
前轴承= Nm
后轴承= Nm
项目五
用深度尺实测主轴套筒端面到主轴套隔台的长度K1值,选手记录以下数据,请裁判签字确认:
K1= mm
K11= mm
K12= mm
K13= mm
………
K1n= mm
实测叠加放置高度K2值,选手记录以下数据,请裁判签字确认:
K2= mm
K21= mm
K22= mm
K23= mm
………
K2n= mm
实测主轴前端盖凹台深度数值H,选手记录以下数据,请裁判签字确认:
H= mm
H1= mm
H2= mm
H3= mm
………
Hn= mm
按照工艺要求计算主轴前端盖压紧量A=K2-K1-H:
A= mm
检测主轴单锥孔跳动△s,选手记录以下数据,请裁判签字确认:
△s= mm
项目六
机械主轴与主轴测试台对接安装
安装流程:S1-将主轴安装在赛场提供的主轴测试架上(参见图2-2);
S2-安装交流异步电动机于电机座上;
S3-预装弹性联轴节(对接两轴);
S4-调整交流异步电机轴与主轴传动芯轴的同轴度;
S5-锁紧联轴节;
S6-安装安全防护罩。
安装完成后的效果参见图2-3。要求:
1)机械主轴在测试台上应调整至主轴中心线与电机轴中心线同轴,联轴节安装规范。
2)调整电机轴与主轴传动芯轴同轴,选手采用百分表或千分表检测。记录实测数据,请裁判确认:
3)异步电机安装时提供0.02mm和0.04mm铜皮做调整垫。
4)上述每完成一步均应协助裁判员检测、确认。
5)电机轴与主轴轴芯同轴度 >0.3mm时,不允许带电旋转。
6)安全防护罩安装合格后,方可通电检查。
序号
检查事项
技术指标检验标准
1
急停检查
急停按钮起作用
2
伺服驱动检查
解除伺服报警
3
进给伺服移动无报警
X/Y/Z 轴显示正常,在JOG方式和录入方式下,倍率100%移动各轴,能正常移动无报警
4
伺服移动方向正确
X/Y/Z轴在JOG方式下+/-移动确认轴运动方向符合立式数控铣床相关坐标定义标准。
5
进给轴软/硬限位
检测各轴运行范围符合该机床行程规格且限位有效
6
坐标轴移动准确
检测手轮或MDI方式下进给轴移动的实际距离与显示数值相等
7
进给轴倍率修调正确
在JOG(手动)和MDI方式下移动进给轴,调整倍率开关,轴按照指定倍率移动
8
手轮方式下轴选正确
在手轮方式下,切换手轮轴选开关信号,能够正确选择相应的坐标轴,实现X/Y/Z轴移动。
9
手轮方式下倍率正确
在手轮方式下,切换手轮倍率信号,移动X/Y/Z轴,能够正确实现相应的倍率。
10
进给轴伺服驱动性能匹配
通过伺服优化,观察圆图形误差有明显改善
11
主轴的启动和停止正常
在JOG(手动)和MDI方式下,能够启动和停止主轴。
12
主轴定向准确
MDI方式下,执行M19,主轴准停准确。
13
主轴旋转方向正确
在MDI方式下,执行M03 S500检查主轴的旋转方向正确
14
主轴速度和倍率正确
在MDI方式下,执行M03 S500检查主轴的旋转速度和各档倍率正确
15
机床操作面板功能正常
检查机床操作面板各按键、旋钮、指示灯功能正常
序号
故障现象
处理方案
学生签字
裁判签字
1
原因
解决方法
已排除()未排除()申请排除()
2
原因
解决方法
已排除()未排除()申请排除()
3
原因
解决方法
已排除()未排除()申请排除()
4
原因
解决方法
已排除()未排除()申请排除()
5
原因
解决方法
已排除()未排除()申请排除()
6
原因
解决方法
已排除()未排除()申请排除()
7
原因
解决方法
已排除()未排除()申请排除()
8
原因
解决方法
已排除()未排除()申请排除()
9
原因
解决方法
已排除()未排除()申请排除()
10
原因
解决方法
已排除()未排除()申请排除()
11
原因
解决方法
已排除()未排除()申请排除()
12
原因
解决方法
已排除()未排除()申请排除()
13
原因
解决方法
已排除()未排除()申请排除()
14
原因
解决方法
已排除()未排除()申请排除()
15
原因
解决方法
已排除()未排除()申请排除()
小计
=SUM(ABOVE) 15分
序号
项目
项目内容
1
手夹和夹具安装与调试
在加工中心上安装夹具,调整气压。
2
设计夹具气路,按设计气路图,完成夹具的气路连接
3
设计夹具传感器控制回路,按设计的回路,完成夹具的传感器控制回路的连接。
4
MDI状态下,夹具夹紧、松开
5
MDI状态下,夹具夹紧到位验证、夹具松开到位验证
6
MDI状态下,夹具上零件有无信号验证
7
机器人气爪功能验证
机器人气爪松开功能及控制信号验证
8
机器人气爪夹紧功能及控制信号验证
9
手爪松开到位控制功能及控制信号验证
10
手爪夹紧到位控制功能及控制信号验证
序号
项目
要求
1
放置测头接收器
将测头接收器固定于电气柜顶部合适位置
2
测头电气连接
1)连接测头接收器电源线。
2)连接“工件测头开启”信号线至PLC输出点Y10.7,并在PLC中编辑M88开启测头/M89关闭测头的梯形图。
连接“测头状态”信号线至数控系统测量输入点X11.7
4)在MDI下开启测头,输入测量信号测试指令“G91G31X50F50”,待机床运动后,用手触碰测头测针,以模仿机床碰到了测针,观察机床能否正确地停止。
3
测针对中调整
利用百分表或千分表调整测针圆跳动,使之不超0.03mm。
记录测量值 (请裁判当场确认)。
4
测头径向标定
1)用磁铁固定或利用工作台上的台钳轻夹自备环规,保持上表面平行工作台面。
2)将测头装至机床主轴,并手动定位至环规大约中心位置,测球低于环规上表面。
3)M88;(测头开启代码)
4)MDI编写并执行测头标定宏程序:
G65P9901M102.D;
D:环规准确直径;标定结果位于:#500,#501,#502,#503。
5)M89;(测头关闭代码)
5
环规直径测量
同上1、2步骤。
3)M88;(测头开启代码)
4)MDI下执行G65P9901M2.D_S。
D:环规准确直径;S:更新的工件坐标系编号。
注:#100存储环规直径测量值。
并将环规直径值存储到#610,编写#610=#100并执行。
5)M89;(测头关闭代码)
序号
项目
项目内容
1
变频器连接与调试
异步电机连接正确
2
系统模拟电压及信号线连接正确
3
模拟主轴参数设置正确,模拟主轴被激活
4
变频器通电及参数设置正确
5
联动后振动测试
纪录振动分贝值 (请裁判签字确认)。注:主轴芯轴和电机轴同轴度大于0.3mm 时不能进行此测试。
项目内容
调整结果
项目内容
PC与NC互联互通
参数调整
PC侧IP地址设置正确
NC侧IP地址设定正确
数据线连接成功
NC侧调用程序成功
新定义内容
在操作面板上定义
输入地址
输出地址
主轴正转
Fx
X.X
X.X
主轴反转
Fx
X.X
X.X
增速按钮
Fx
X.X
X.X
减速按钮
Fx
X.X
X.X
主轴停止
Fx
X.X
X.X
分类
正转/反转/主轴停
备注
主轴指令
MXX/MXX/MXX
也可自行定义未用M代码
主轴速度指令
SXX
序号
项目
项目内容
1
PLC编程
MDI方式下执行主轴控制M/S代码,主轴旋转
2
主轴正转按钮/主轴反转按钮/LED有效
3
增速按钮/减速按钮/ LED有效
4
主轴停止按钮/ LED有效
序号
项目
项目内容
1
互联互通
数控机床与虚拟制造仿真软件间的互联互通信号连接。
2
PLC程序开发
编写虚拟机器人实现对加工中心上下料流程的PLC程序开发。
3
功能验证(3~10项中指定2项进行验证)
机床执行M**指令,可以运行无报警
4
机床可以回到指定的第二参考点
5
机器人可以在传送带上抓取毛坯
6
机床门可以自动打开
7
机床平口钳可以自动松开
8
平口钳夹紧,机器人可以完成机床上料
9
机床门可以自动关闭
10
虚拟制造仿真流程与给定的流程图符合
序号
项目
项目内容
1
开发PLC程序
MDI 和单步方式下,自动门开、自动门开到位。
2
MDI 和单步方式下,自动门关、自动门关到位。
3
自动门安全联锁
自动门关闭时,机器人无法进入数控机床,自动门开启时,机器人进入数控机床运行解锁
4
智能加工区域安全围栏
安全围栏门开启时,机器人停止运行,安全围栏门关闭时时,机器人停止运行解锁。
序号
项目
项目内容
1
机器人上料示教编程
示教编程实现上料时机器人对第1件毛坯抓取,并放置到加工中心夹具中,实现夹紧,以及机器人退出加工位置
2
机器人下料示教编程
示教编程实现下料时机器人对夹具上的工件的抓取,配合夹具的松开,机器人将工件施加到毛坯1位置,移动到毛坯2位置上方。
序号
评分内容
评分细节(每行扣完为止)
1
测量准备
台面清扫
装夹测头前执行MXX定向指令,之后进行测头装夹。
在MDI下开启测头,输入测量信号测试指令用手触碰测头测针,检查机床是否停止运动。
2
编程测量
三点或四点测量圆直径
编程正确
结果输出至宏变量
图6-1 试切件图
(3)选手根据图纸要求和赛场提供的毛坯,自行设计试件切削试验工艺,完成试件切削试验的程序编制和加工。
(4)选手自备刀具、刀柄和量具,合理安装、调整刀具,配合其它工、量具使用,完成试件切削试验操作。
(5)试切件毛坯要求:毛坯形状、尺寸及其技术要求参见样题,毛坯由承办校准备,为每个参赛队共提供三件毛坯,本环节使用其中的一件毛坯,此件不得作为零件加工质量的检测件。赛场另准备若干备用件,当仅当提供给参赛队的毛坯出现“硬点”等质量问题时,参赛队可以提出更换毛坯。当参赛选手因自身原因损坏毛坯时,不予更换毛坯。
任务七:机床精度检验(10分)
本任务基于:标准GB17421-1/2/4和GB-T20957[1].2-2007精密加工中心检验条件(2)标准检测方法和评价标准,包括圆度误差检测。
7-1.数控机床几何精度测量
1.依据GB/T 18400.2-2010 (ISO10791-2:2001)精密加工中心检验条件(2)中的部分测量标准以及GB/T 17421.1-1998通用标准,选择5项检验项目,利用所提供的工具、量具、检具,进行数控机床几何精度测量。
2.工具、量具、检具选用合理,使用方法正确,每一项数据检测完成后,选手应举手示意,经现场裁判确认后将检测结果填入表7-1几何精度检测表中。
表7-1:数控机床几何精度测量评分记录表
7-2.运动精度检测——球杆仪检测圆轨迹运动精度
按照表7-2中第二列“检测项目”和第三列“要求”,使用球杆仪对机床某指定位置按GB17421.4或ISO230-4标准要求测量XY平面圆度(假定机床温度20℃,膨胀系数11.7)。并填写和保存数据。
表7-2:运动精度检测参考评分标准
任务八:零件智能加工验证(15分)
8-1 单步模式下和自动模式下分别验证智能加工流程。根据8-1给出的参考智能加工流程和环节,或选手自行设计智能加工流程和环节,利用给定的一组M指令,进行PLC编程。完成: = 1 \* GB3 ①单步模式下,用30秒延时替代零件真实加工,完成智能制造,验证智能加工流程。 = 2 \* GB3 ②自动模式下,按单步模式下相同的智能加工流程,真实加工2件毛坯和得到2件零件(选手不得人工干预智能加工过程)。两种模式下的验证请裁判确认。
表8-1:智能加工验证
8-2 加工完成后,选手清理工作台,选手选择1件智能加工完成的零件,由裁判封存送检。选手请参考表8-2,确保零件加工质量
表8-2:零件加工质量参考
序号
检验项目
简图
1
线性运动直线度-X轴线运动的直线度(具体按赛卷)
a) 在 ZX 垂直平面内 b) 在 XY 水平面内
检验项目一简图 X轴线运动的直线度
根据GB/T 18400.2-2010,局部公差:在任意300测量长度上,公差0.007;X500,公差0.010;500X800,公差0.015;800X1250,公差0.020;1250X2000,公差0.025。
检验工具:a)平尺 指示器或光学方法;b)平尺 指示器或钢丝和显微镜或光学方法
检验方法:对所有结构型式的机床,平尺或钢丝或直线度反射器都应置于工作台上,如主轴能锁紧,则指示器或显微镜或干涉仪可装在主轴上,否则检验工具应装在机床的主轴箱上。测量线应尽可能靠近工作台的中央。
在 ZX 垂直平面内的直线度: (裁判签字确认)
在XY水平面内的直线度: (裁判签字确认)
2
选择项目2
选自GB/T 18400.2-2010 (ISO10791-2:2001)精密加工中心检验条件(2)中的部分测量标准以及GB/T 17421.1-1998通用标准
3
选择项目3
同上
4
选择项目4
同上
5
选择项目5
同上
序号
检测项目
检测内容
设定数据(选手填写)
裁判
签字
1
编制X-Y平面测试程序(可以借鉴仪器帮助手册中的已有程序),并输入数控系统
半径:100mm,
进给速度
1000mm/min
2
设定球杆仪测试中心
在机床上建立测试程序的坐标系原点
记录所设定坐标系原点:
X:
Y:
Z:
3
测试程序调试
空运行测试程序
4
蓝牙连接调试
将球杆仪与电脑连接起来
5
配置校准规
配置校准规30mm~100mm中任意一种
校准规校准后球杆仪实际长度:
6
安装球杆仪并测试
测量后存储测试报告到选手文件夹
7
按GB17421-4分析圆度误差
记录圆度误差值:
G(CW)顺时针圆度
G(CCW)逆时针圆度
8
给出该处X-Y平面垂直度误差
记录垂直度:
序号
项目
项目内容
1
单步模式下验证智能加工流程(6分)
自动门开、夹具松开(2个环节)
2
机器人抓取第1件毛坯、上料至机床(2个环节)
3
机器人放置毛坯、夹具夹紧(2个环节)
4
机器人回退到位(1个环节)
5
自动门关、机床暂不进行真实加工,用延时30秒钟替代(2个环节)
6
延时到,机床门开、夹具松开(2个环节)
7
机器人下料运动至机床(1个环节)
8
机器人抓取零件(1个环节)
9
机械人回退到位,放置零件(2个环节)
10
机器人移动,抓取第2件毛坯,进入下一个循环(2个环节)
11
自动模式下验证智能加工流程
自动模式下,第1件零件完成加工。
12
自动模式下,第2件零件完成加工。
序号
项目
评分细则(每行扣完为止)
1
形状检查
工件形状与图纸符合。
2
质量检查
若形状检查不符合图纸,本项得分0分。
若符合,进一步计加工质量
160mm x 160mm图示形位公差直线度≤0.02mm(三处)
160mm x 160mm图示形位公差垂直度和平行度≤0.02mm(二处)
108mmx108mm四边直线度和倾斜度≤0.02mm(四处)
图示形位公差3°斜边直线度和倾斜度≤0.02mm(二处)
Φ108mm圆度≤0.015mm
加工表面粗糙度
九:职业素养和安全意识(10分)
本赛项专设职业素养和安全意识评价环节,用于评价选手在竞赛全程的职业素养水平和安全意识。选手参照表8-1中的要求执行。
表9-1:职业素养与安全意识评分记录表
序号
项目
要求
1
安全意识
着装、电工鞋及其他劳动防护得当、具有良好的安全意识及行为。
2
遵守规范
操作过程中遵守标准和规范。
3
践行5S
工、量具码放整齐,保持工位清洁卫生,践行现场5S管理规范。
4
和谐友善
参赛选手间和谐团结,善意对待其他选手。
5
诚信文明
在提出补时申请时,以及赛后向指导教师描述申诉事实时,不夸大不扭曲事实。尊重裁判及其他赛场工作人员,言行举止文明。
2022年全国职业院校技能大赛高职组 云计算赛项模拟赛题(Word版): 这是一份2022年全国职业院校技能大赛高职组 云计算赛项模拟赛题(Word版),共158页。
2022年全国职业院校技能大赛高职组 智能电梯装调与维护赛项模拟赛题(Word版): 这是一份2022年全国职业院校技能大赛高职组 智能电梯装调与维护赛项模拟赛题(Word版),文件包含智能电梯装调与维护赛项赛题A卷doc、智能电梯装调与维护赛项赛题B卷doc、智能电梯装调与维护赛项赛题C卷doc、智能电梯装调与维护赛项赛题D卷doc、智能电梯装调与维护赛项赛题E卷doc、智能电梯装调与维护赛项赛题F卷doc、智能电梯装调与维护赛项赛题G卷doc、智能电梯装调与维护赛项赛题H卷doc、智能电梯装调与维护赛项赛题I卷doc、智能电梯装调与维护赛项赛题J卷doc等10份试卷配套教学资源,其中试卷共170页, 欢迎下载使用。
2022年全国职业院校技能大赛高职组 中药传统技能赛项模拟赛题(Word版): 这是一份2022年全国职业院校技能大赛高职组 中药传统技能赛项模拟赛题(Word版),文件包含2022年大赛性状+真伪试题-第7套-GA-答案docx、2022年大赛性状+真伪试题-第6套-GA-答案docx、2022年大赛性状+真伪试题-第1套-GA-答案docx、2022年大赛性状+真伪试题-第2套-GA-答案docx、2022年大赛性状+真伪试题-第9套-GA-答案docx、2022年大赛性状+真伪试题-第3套-GA-答案docx、2022年大赛性状+真伪试题-第8套-GA-答案docx、2022年大赛性状+真伪试题-第4套-GA-答案docx、2022年大赛性状+真伪试题-第10套-GA-答案docx、2022年大赛性状+真伪试题-第5套-GA-答案docx、1-2022年中药显微鉴别题库范围评分标准混合粉末doc、2022年大赛性状+真伪试题-第6套-GAdocx、2022年大赛性状+真伪试题-第7套-GAdocx、2022年大赛性状+真伪试题-第8套-GAdocx、2022年大赛性状+真伪试题-第9套-GAdocx、中药炮制操作评分标准docx、2022年大赛性状+真伪试题-第10套-GAdocx、中药调剂操作评分标准docx、2022GS-4Adoc、2022年大赛性状+真伪试题-第3套-GAdocx、2022GS-10Bdoc、2022GS-10Bdoc、2022GS-1Adoc、2022GS-1Adoc、2022GS-1Bdoc、2022GS-1Bdoc、2022GS-2Adoc、2022GS-2Adoc、2022年大赛性状+真伪试题-第4套-GAdocx、2022GS-2Bdoc、2022GS-2Bdoc、中药制剂分析操作评分标准docx、2022年大赛性状+真伪试题-第2套-GAdocx、2022GS-3Adoc、2022年大赛性状+真伪试题-第1套-GAdocx、2022GS-3Adoc、2022GS-3Bdoc、2022GS-3Bdoc、2-2022年中药显微鉴别评分标准docx、2022GS-4Adoc、2022年中药制剂分析操作题库范围评分标准样题doc、2022年中药性状+真伪评分标准docx、2022GS-10Adoc、2022年大赛性状+真伪试题-第5套-GAdocx、2022GS-6Bdoc、2022GS-7Adoc、2022GS-5Adoc、2022GS-4Bdoc、2022GS-10Adoc、2022GS-5Bdoc、2022GS-5Bdoc、2022GS-6Adoc、2022GS-6Adoc、2022GS-5Adoc、2022GS-6Bdoc、2022GS-7Adoc、2022GS-7Bdoc、2022GS-7Bdoc、2022GS-8Adoc、2022GS-8Adoc、2022GS-8Bdoc、2022GS-8Bdoc、2022GS-9Adoc、2022GS-9Adoc、2022GS-9Bdoc、2022GS-9Bdoc、中药药剂操作评分标准docx、2022GS-4Bdoc、2022年大赛中药炮制试题-第7套-GBdocx、2022年大赛中药炮制试题-第8套-GBdocx、2022年大赛中药炮制试题-第8套-GAdocx、中药审方理论评分标准docx、2022年大赛中药炮制试题-第7套-GAdocx、2022年大赛中药炮制试题-第6套-GBdocx、2022年大赛中药炮制试题-第6套-GAdocx、2022年大赛中药炮制试题-第5套-GBdocx、2022年大赛中药炮制试题-第5套-GAdocx、2022年大赛中药炮制试题-第9套-GAdocx、2022年大赛中药药剂试题-第8套doc、2022年大赛中药炮制试题-第9套-GBdocx、2022年大赛中药药剂试题-第10套doc、2022年大赛中药药剂试题-第1套doc、2022年大赛中药药剂试题-第2套doc、2022年大赛中药药剂试题-第3套doc、2022年大赛中药药剂试题-第4套doc、2022年大赛中药药剂试题-第5套doc、2022年大赛中药药剂试题-第6套doc、2022年大赛中药药剂试题-第7套doc、2022年大赛中药药剂试题-第9套doc、2022年大赛中药炮制试题-第4套-GAdocx、2022年大赛中药炮制试题-第4套-GBdocx、2022GT-9Adocx、2022年大赛中药炮制试题-第3套-GBdocx、2022GT-2Cdocx、2022GT-4Ddocx、2022GT-4Cdocx、2022GT-4Bdocx、2022GT-4Adocx、2022GT-3Ddocx、2022GT-3Cdocx、2022GT-3Bdocx、2022GT-3Adocx、2022GT-2Ddocx、2022GT-2Bdocx、2022GT-5Bdocx、2022GT-2Adocx、2022GT-1Ddocx、2022GT-1Cdocx、2022GT-1Bdocx、2022GT-1Adocx、2022GT-10Ddocx、2022GT-10Cdocx、2022GT-10Bdocx、2022GT-10Adocx、2022GT-5Adocx、2022GT-5Cdocx、2022年大赛中药炮制试题-第3套-GAdocx、2022GT-8Ddocx、2022年大赛中药炮制试题-第2套-GBdocx、2022年大赛中药炮制试题-第2套-GAdocx、2022年大赛中药炮制试题-第1套-GBdocx、2022年大赛中药炮制试题-第1套-GAdocx、2022年大赛中药炮制试题-第10套-GBdocx、2022年大赛中药炮制试题-第10套-GAdocx、2022GT-9Ddocx、2022GT-9Cdocx、2022GT-9Bdocx、2022GT-8Cdocx、2022GT-5Ddocx、2022GT-8Bdocx、2022GT-8Adocx、2022GT-7Ddocx、2022GT-7Cdocx、2022GT-7Bdocx、2022GT-7Adocx、2022GT-6Cdocx、2022GT-6Bdocx、2022GT-6Adocx、2022GT-6Ddocx等139份试卷配套教学资源,其中试卷共235页, 欢迎下载使用。