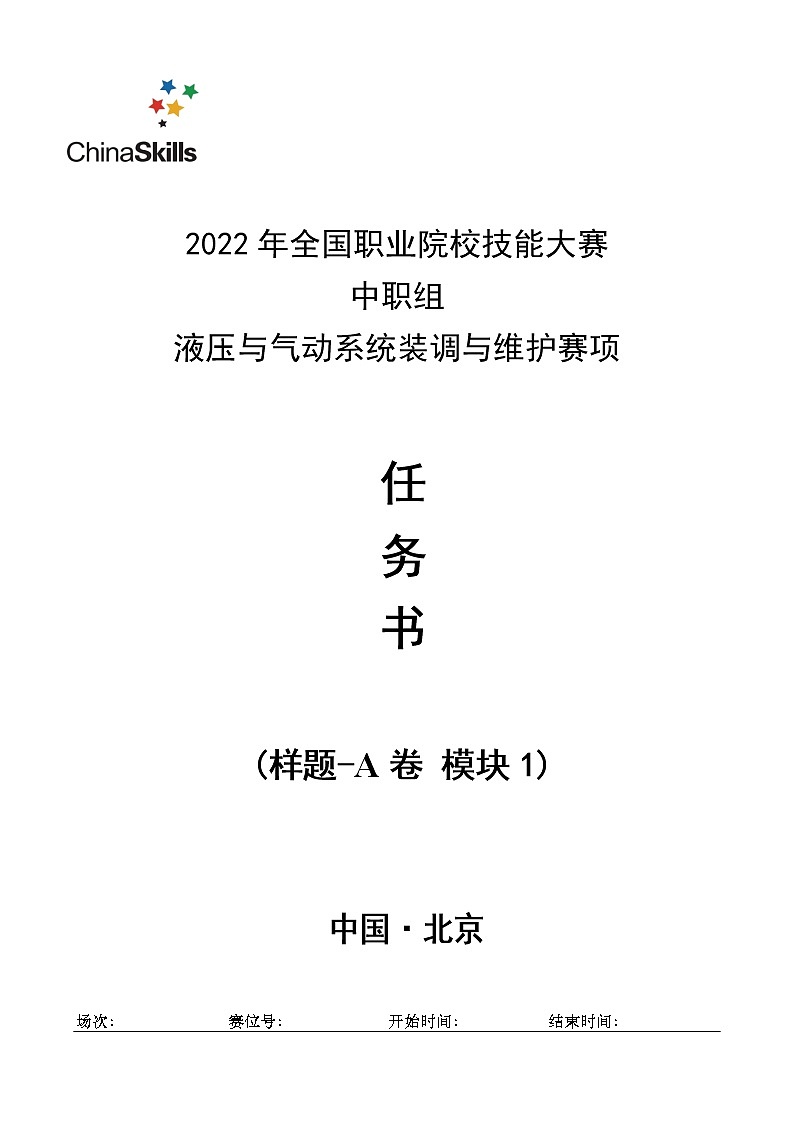
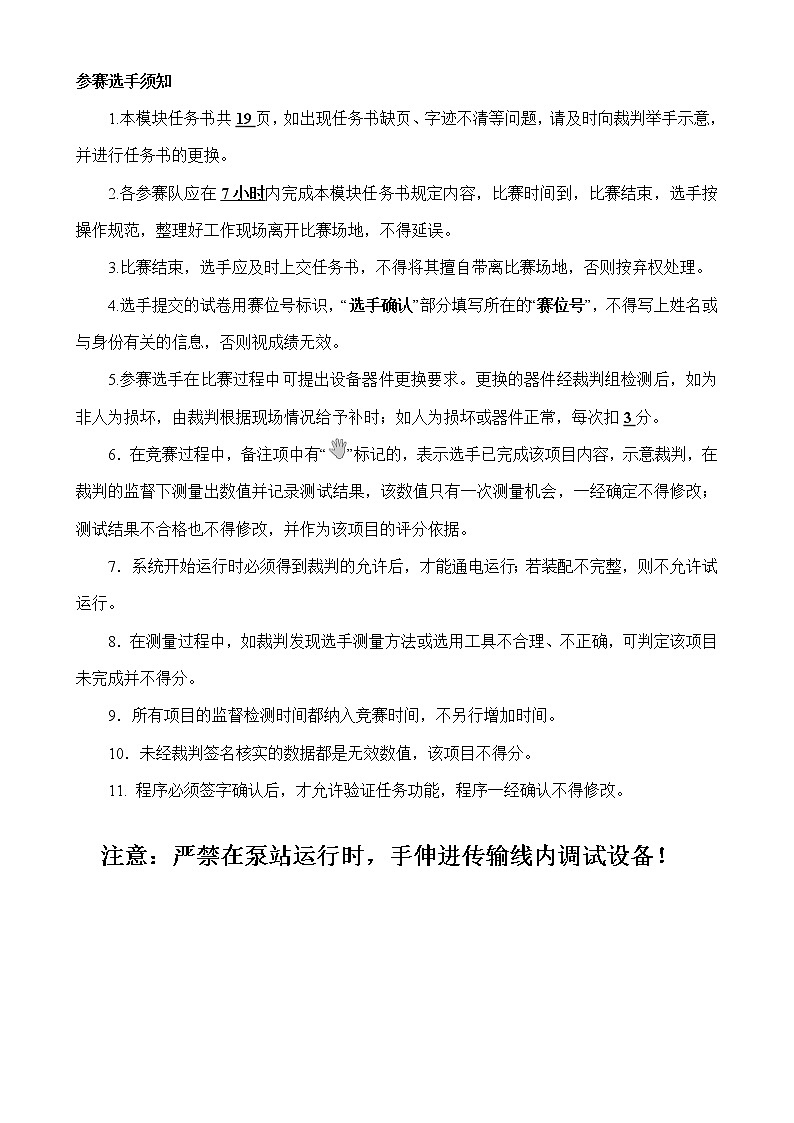
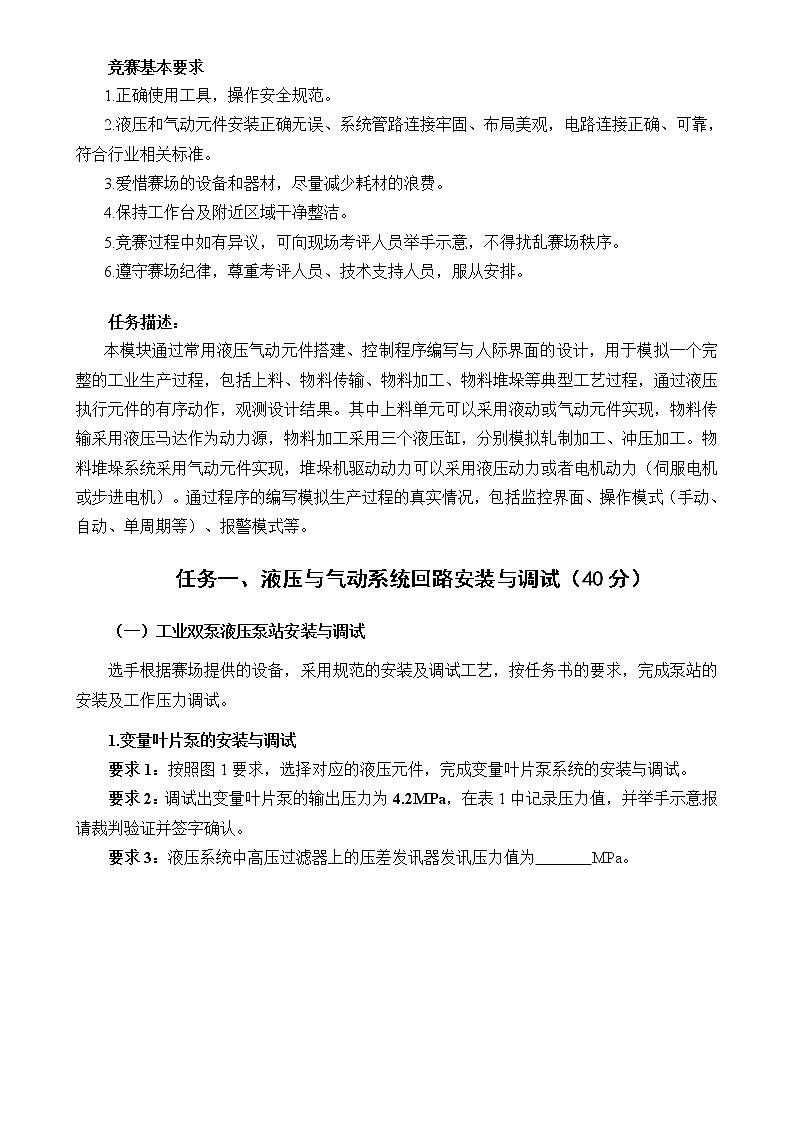
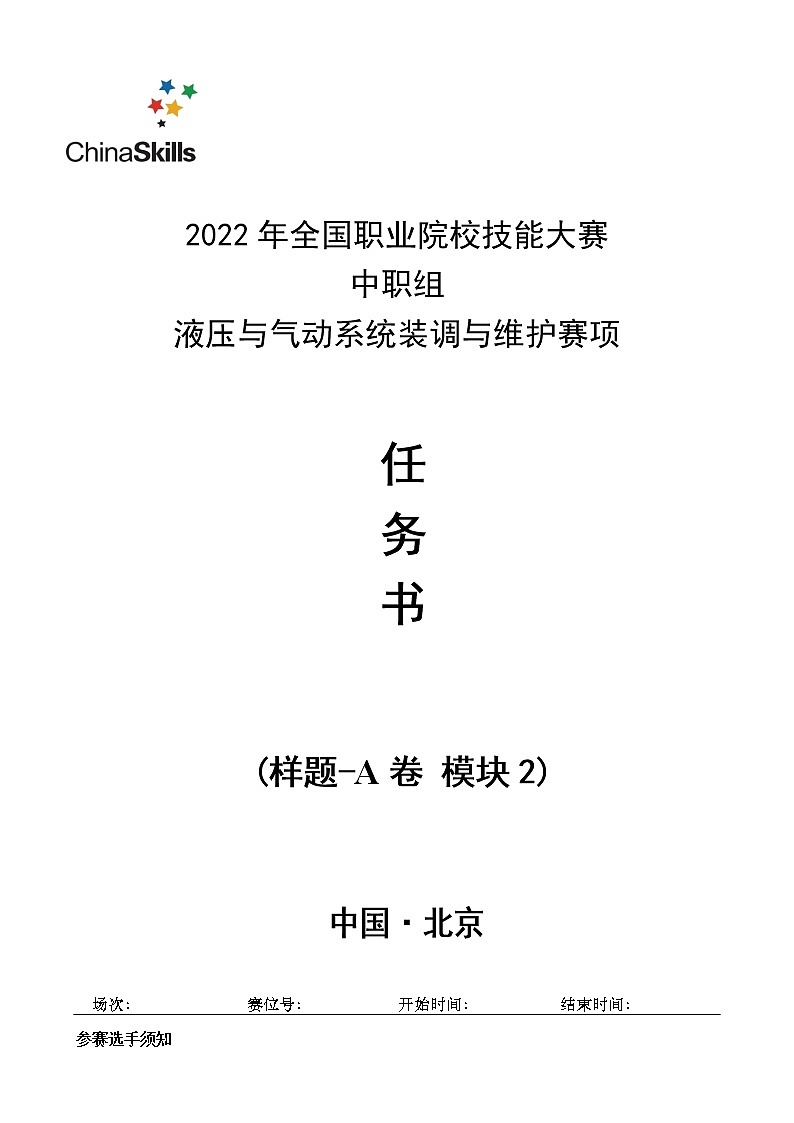
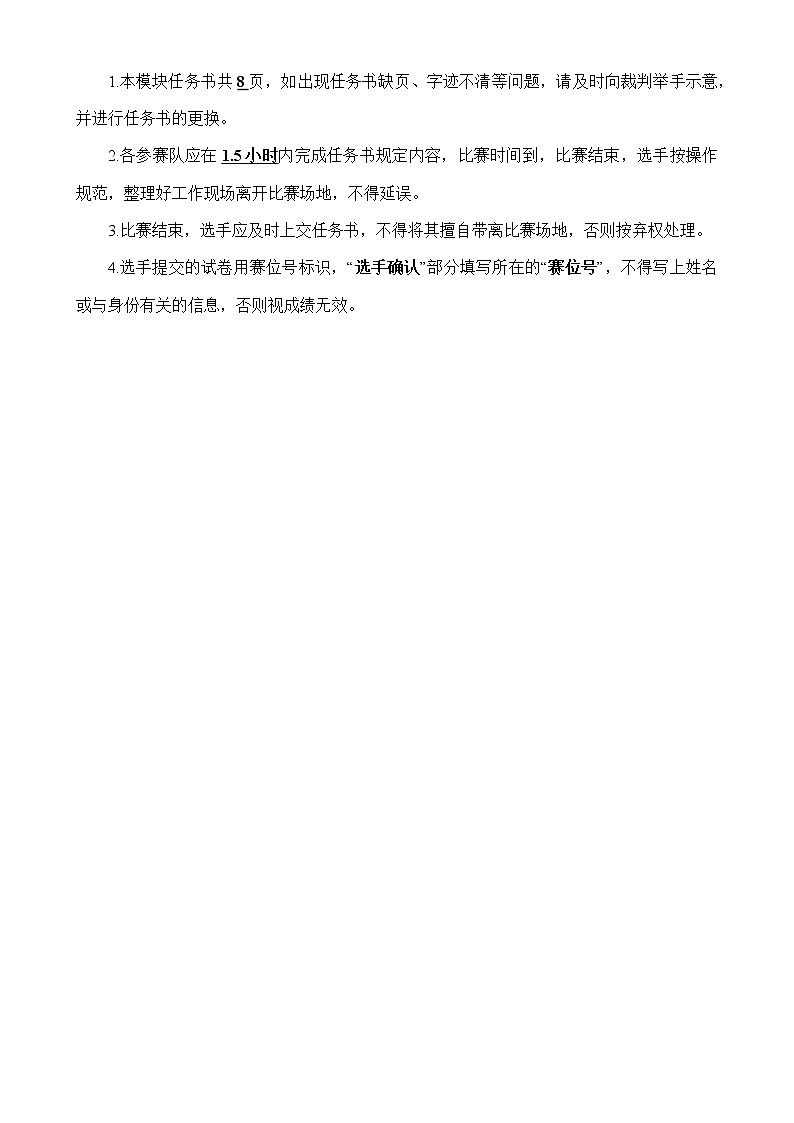
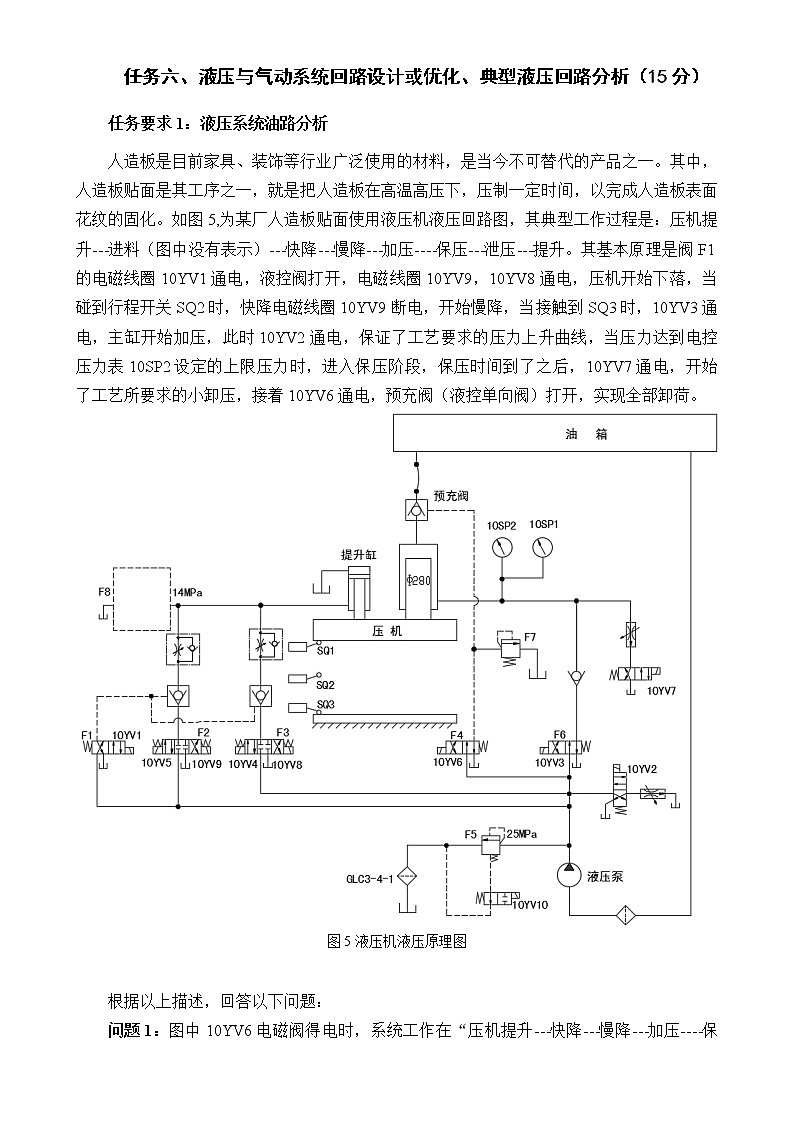
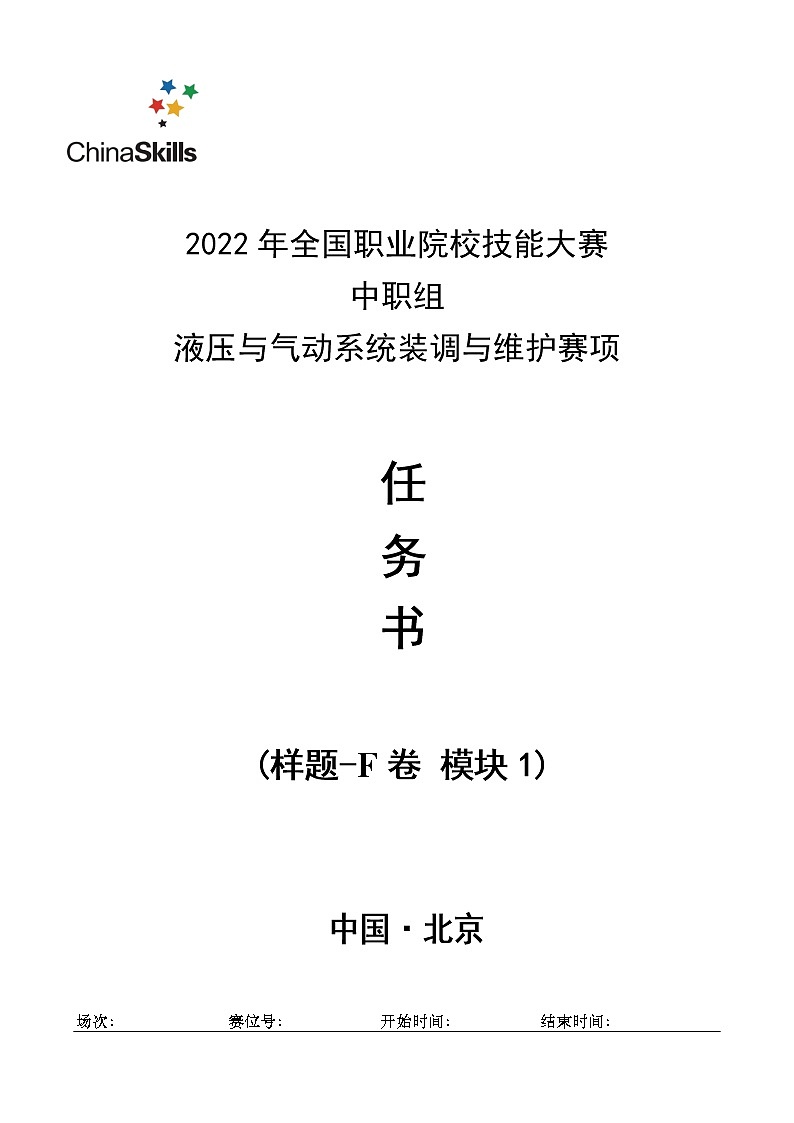
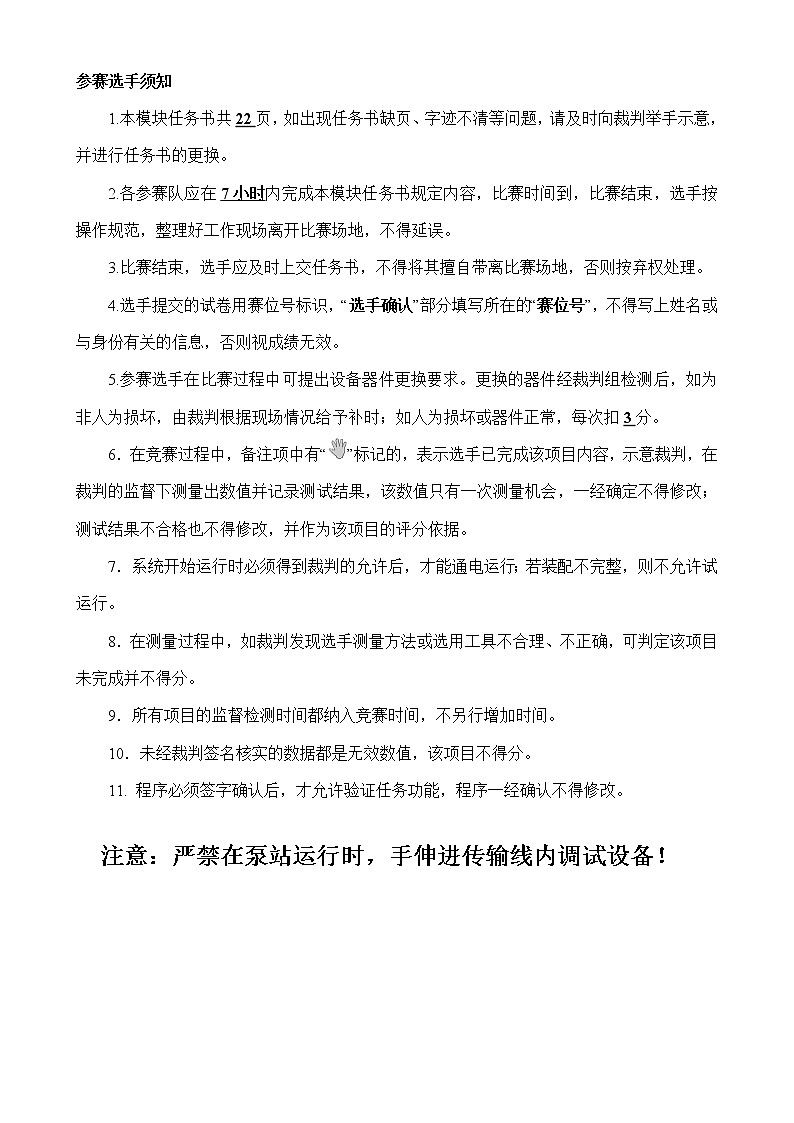
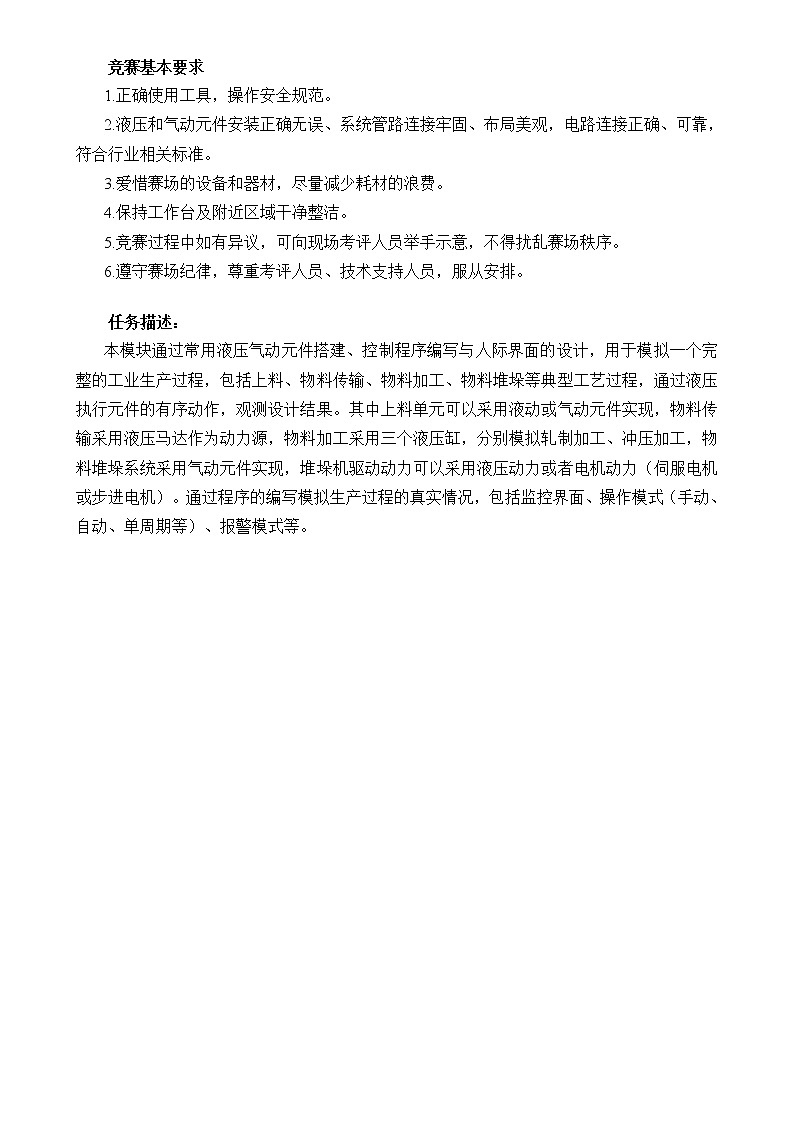
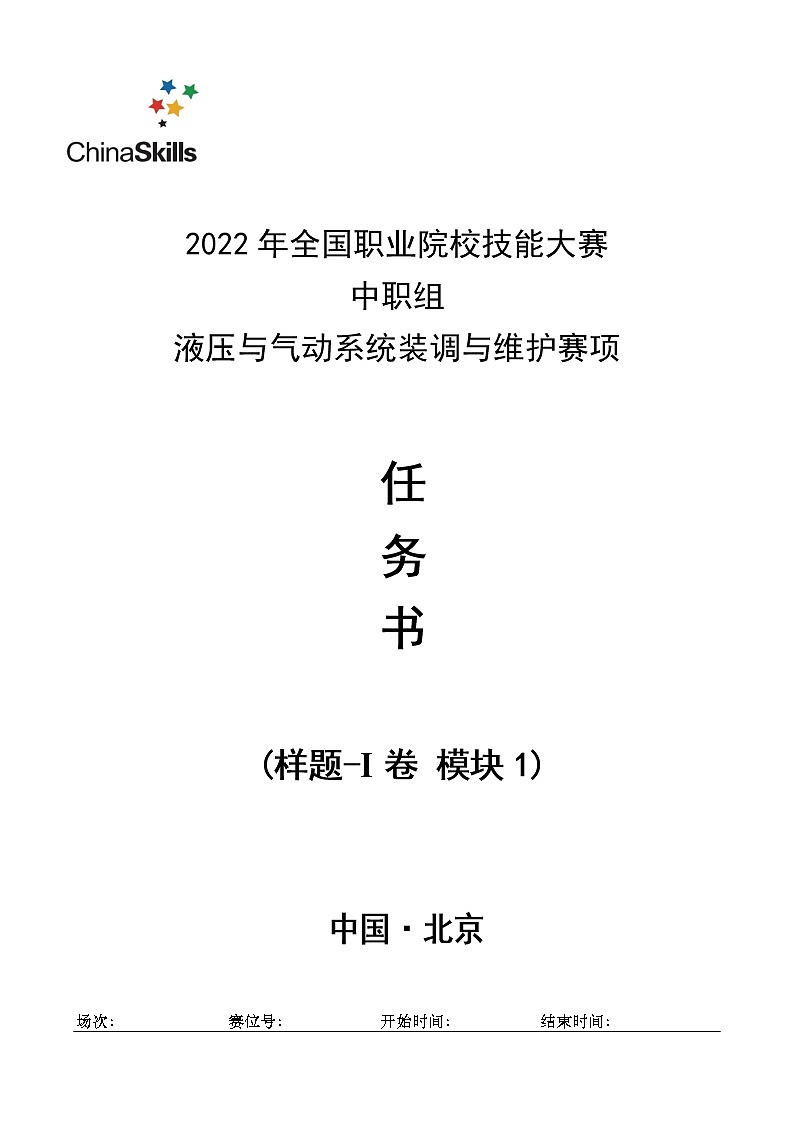
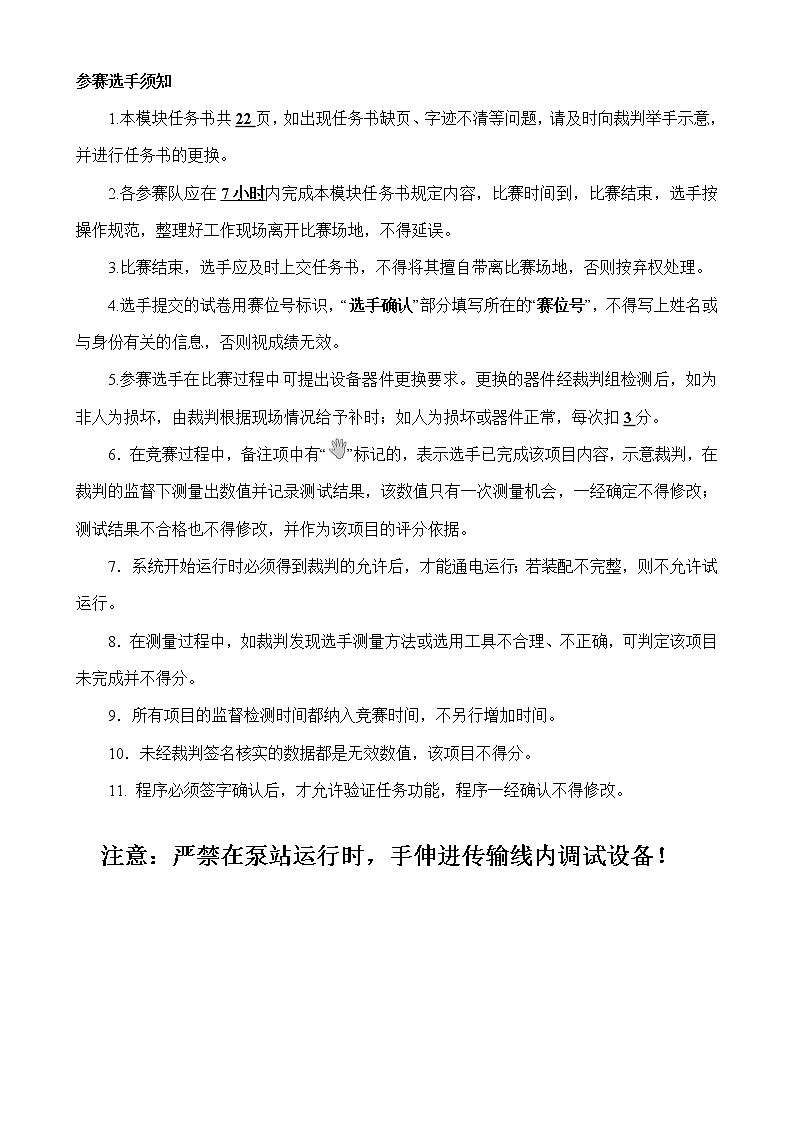
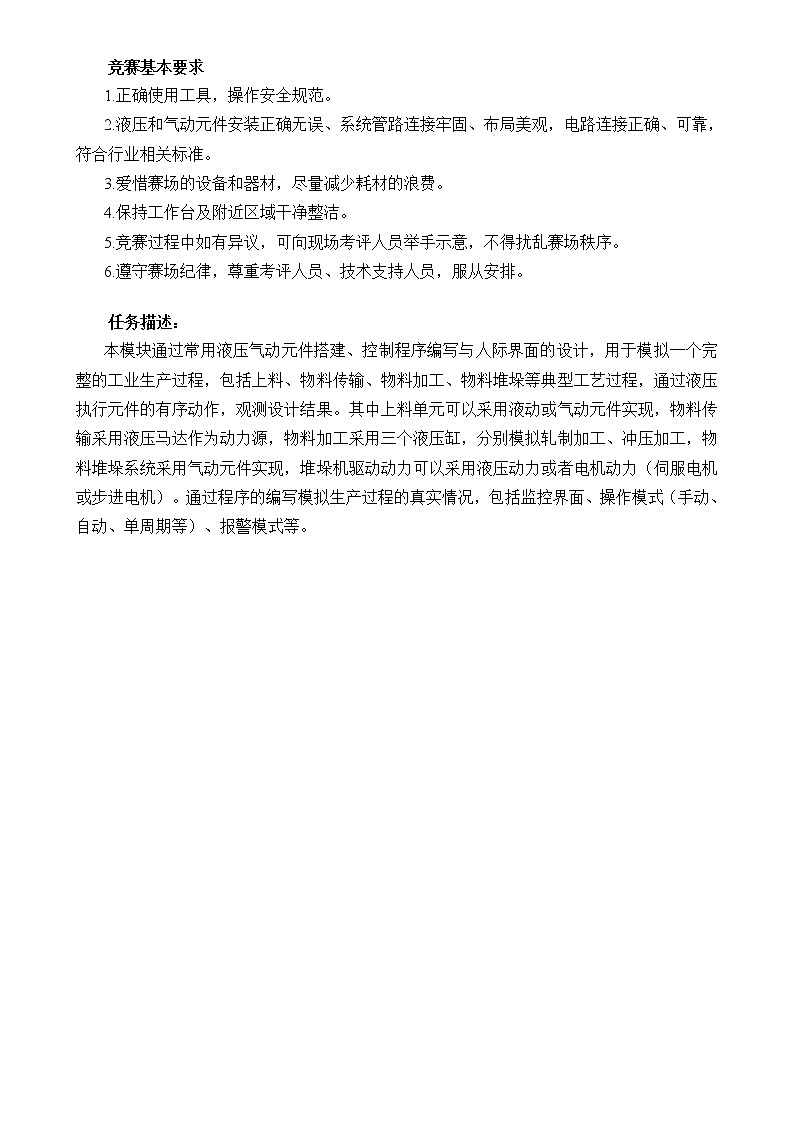
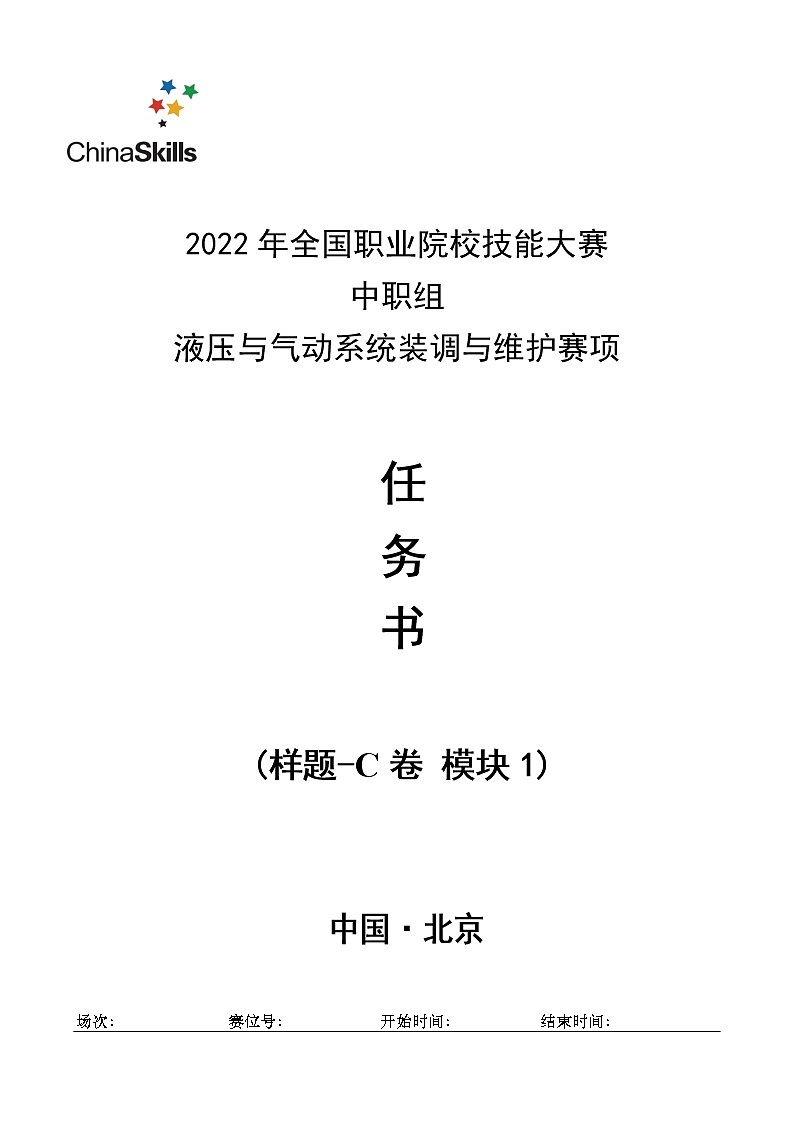
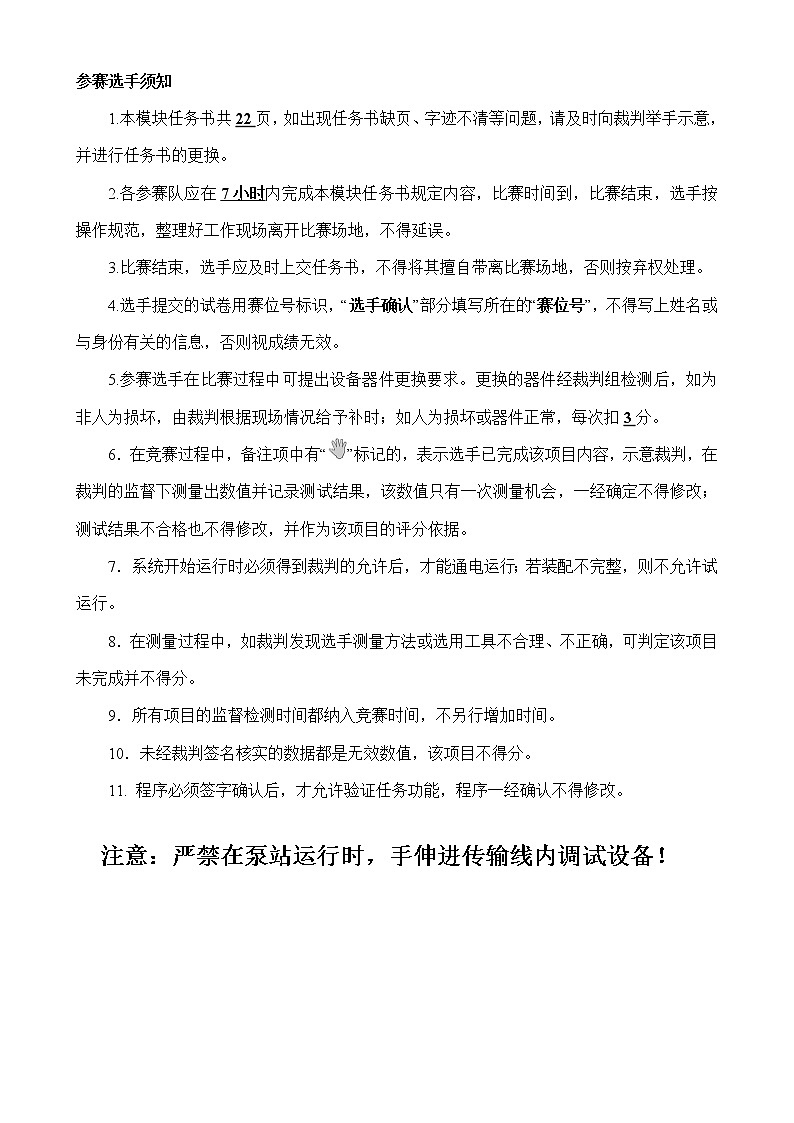
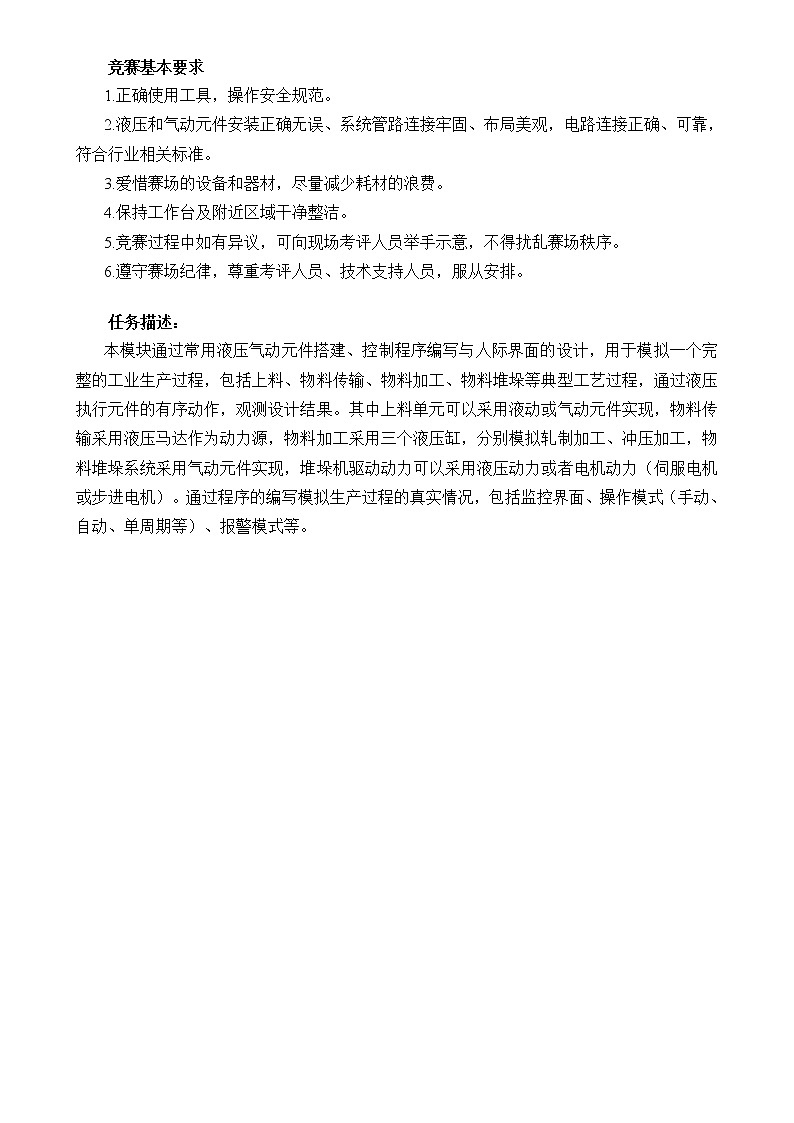
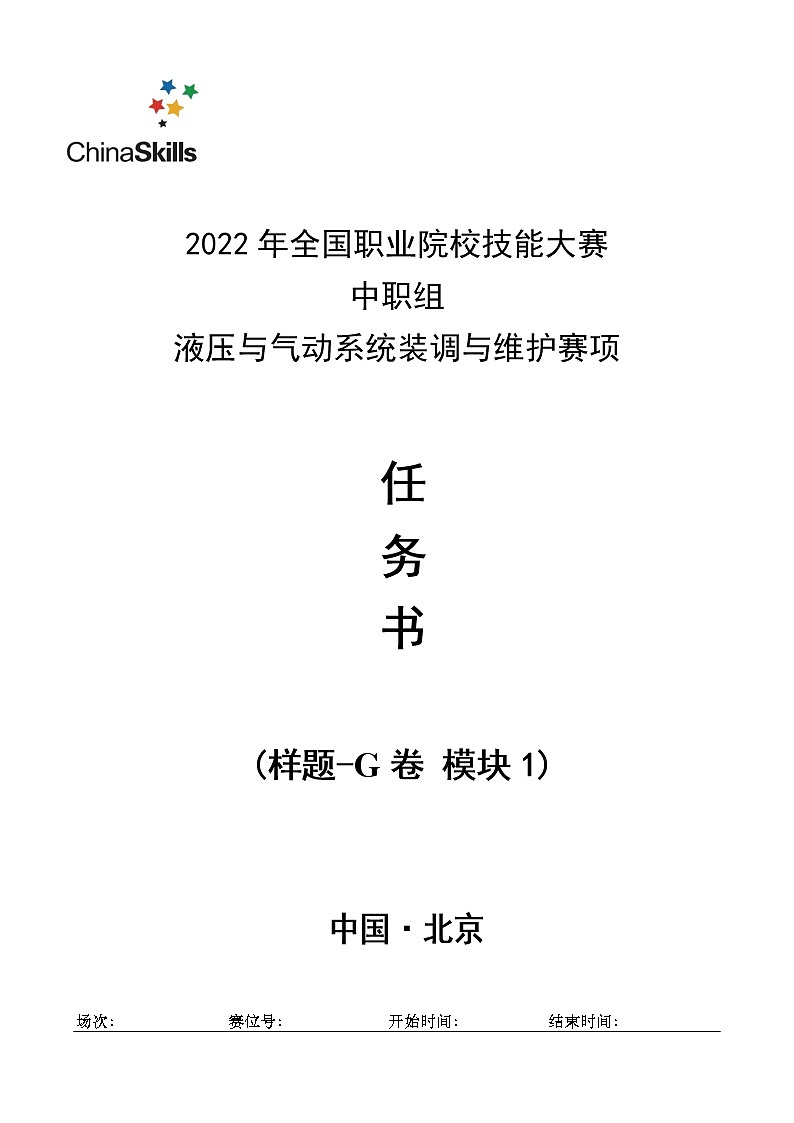
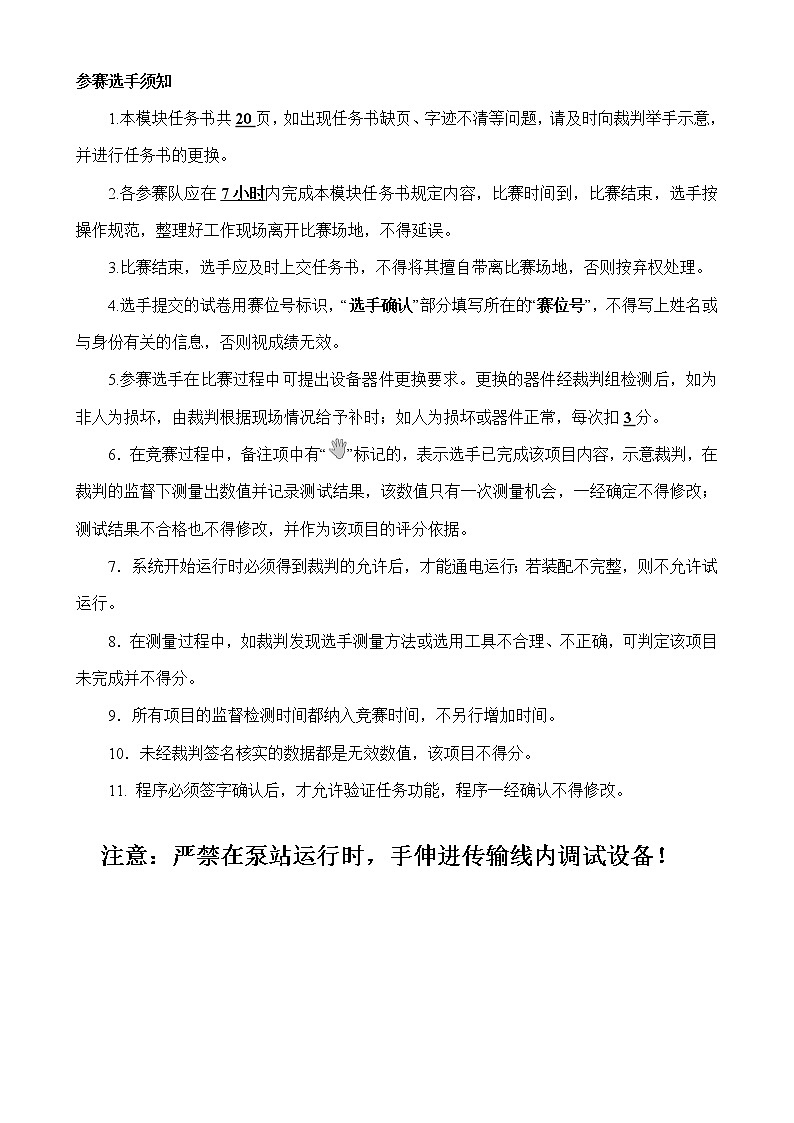
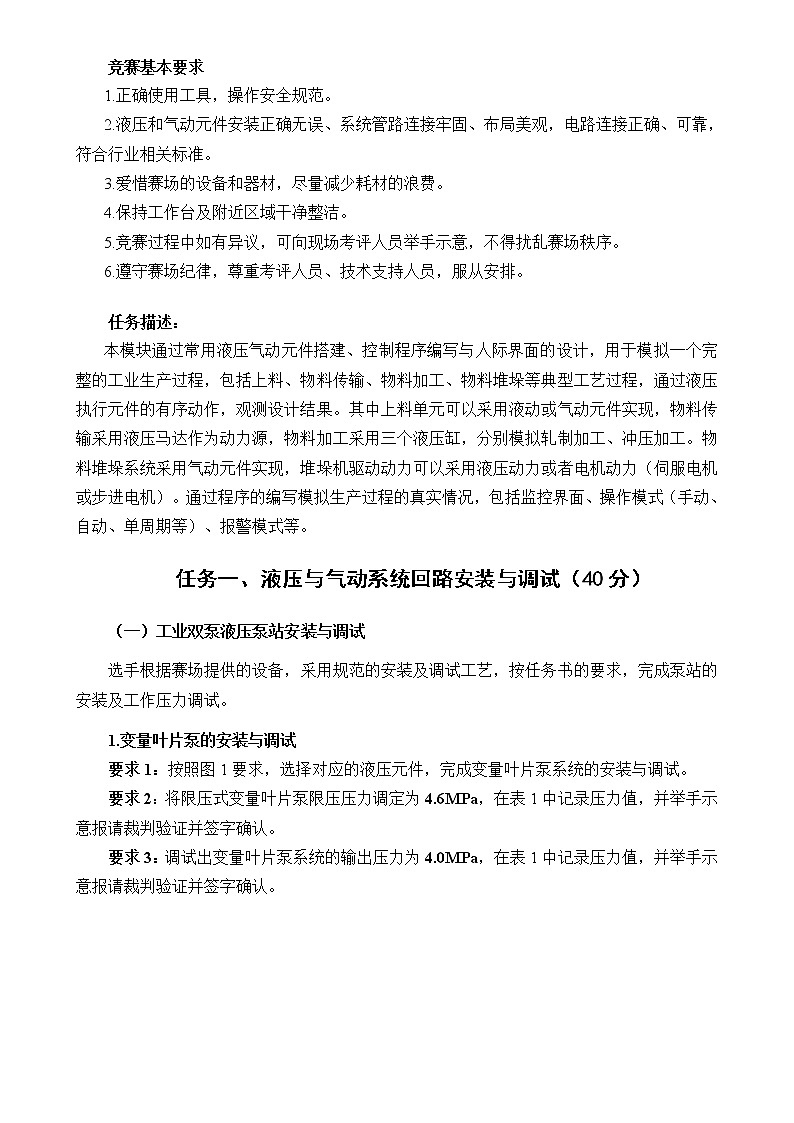
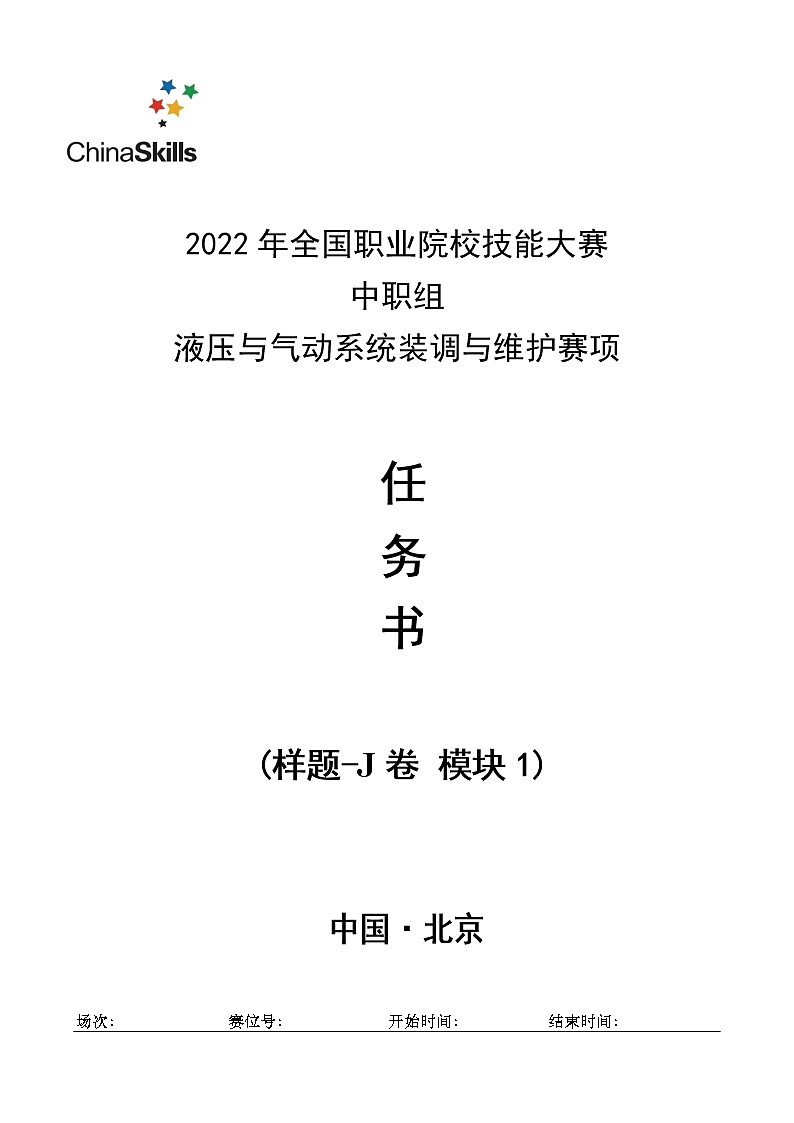
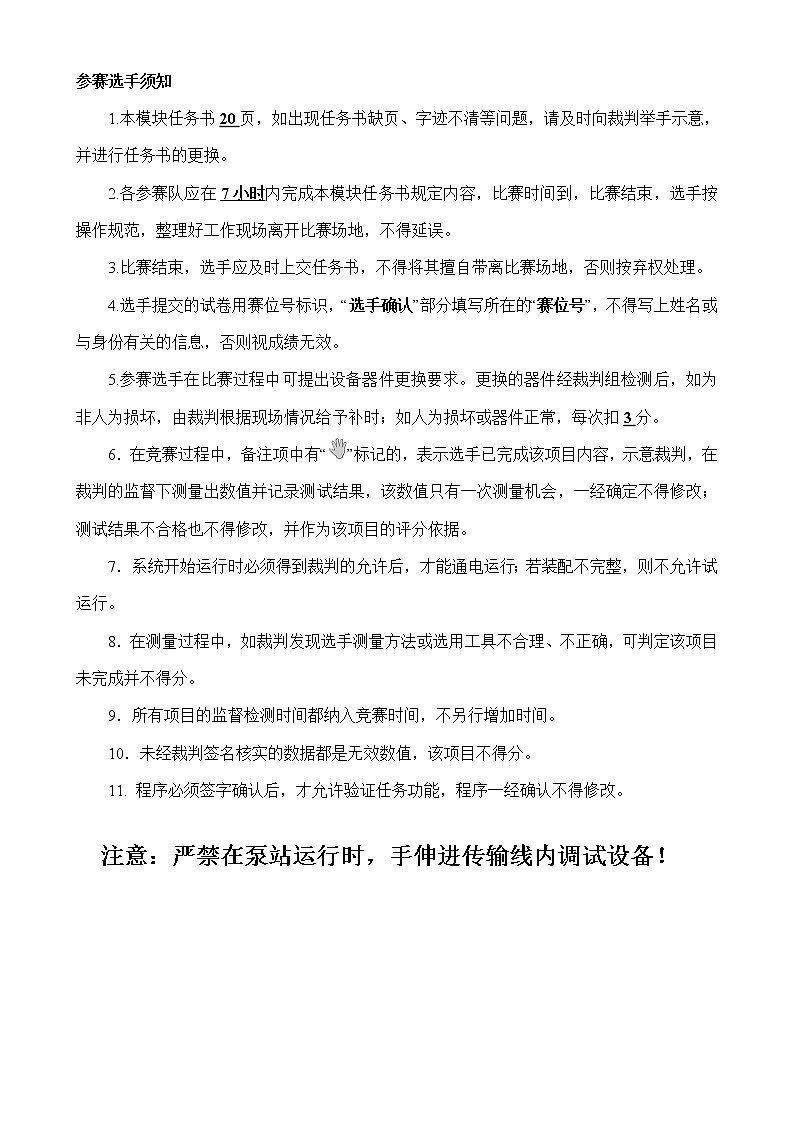
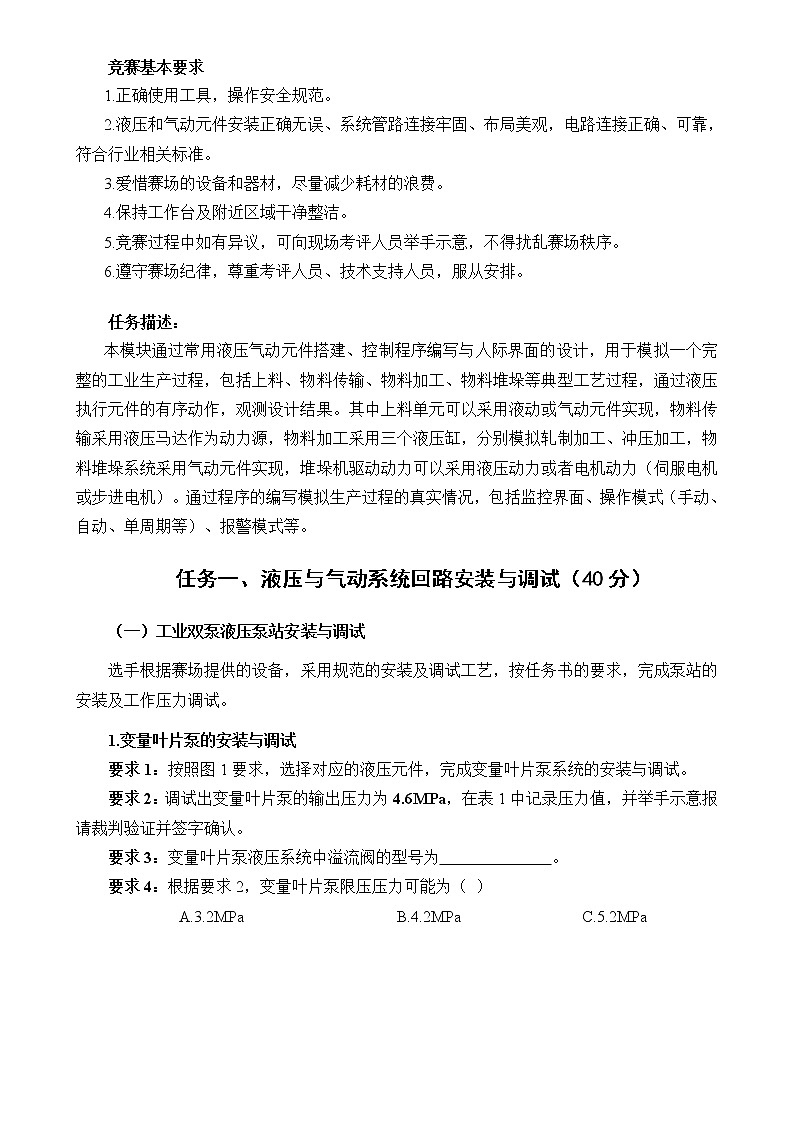
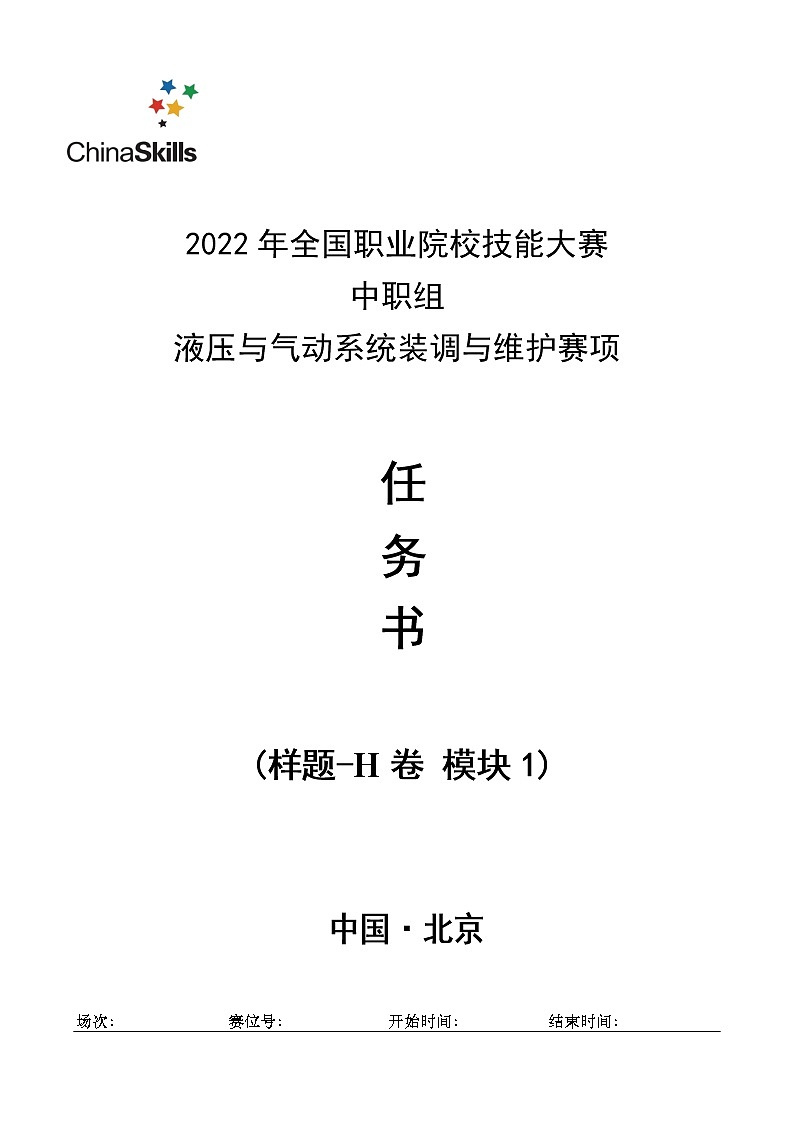
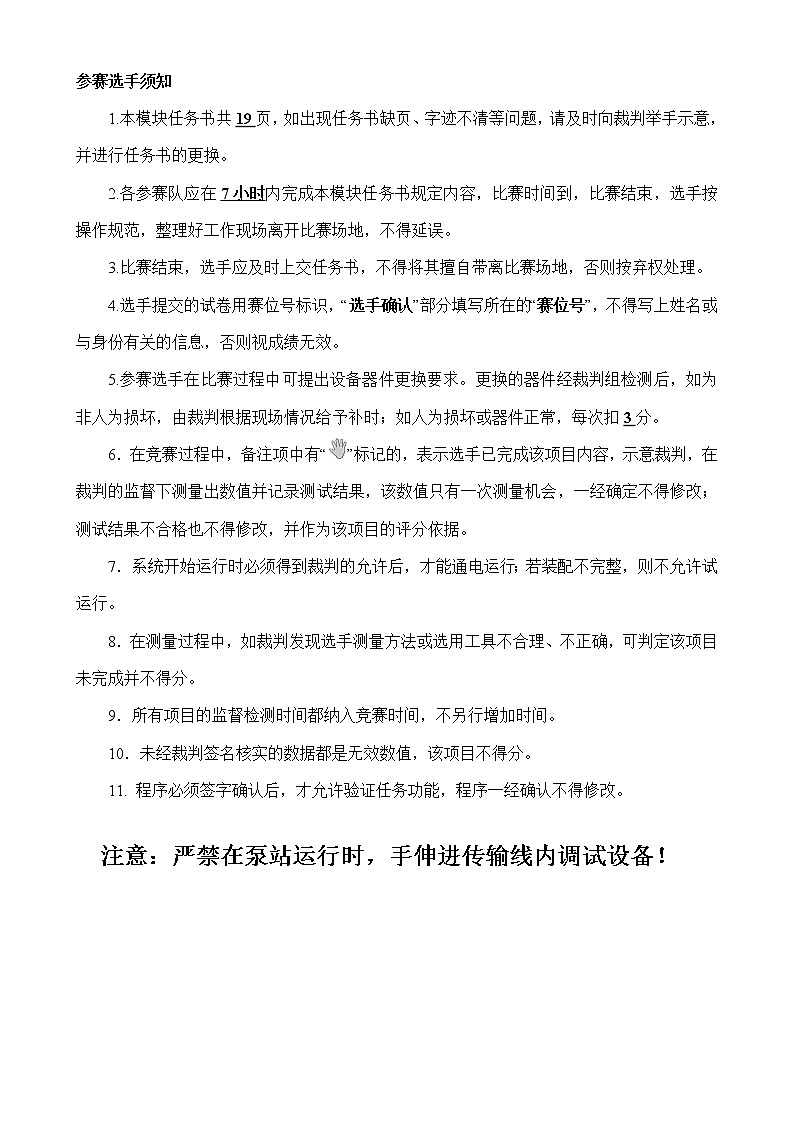
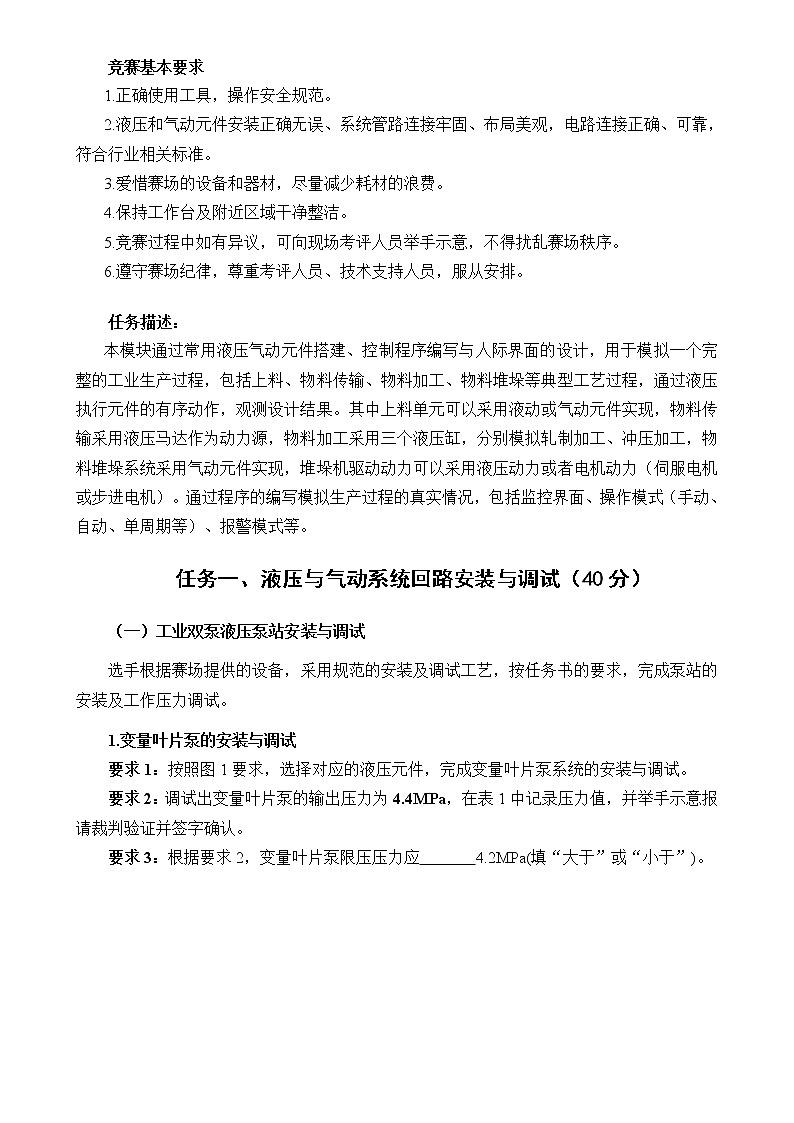
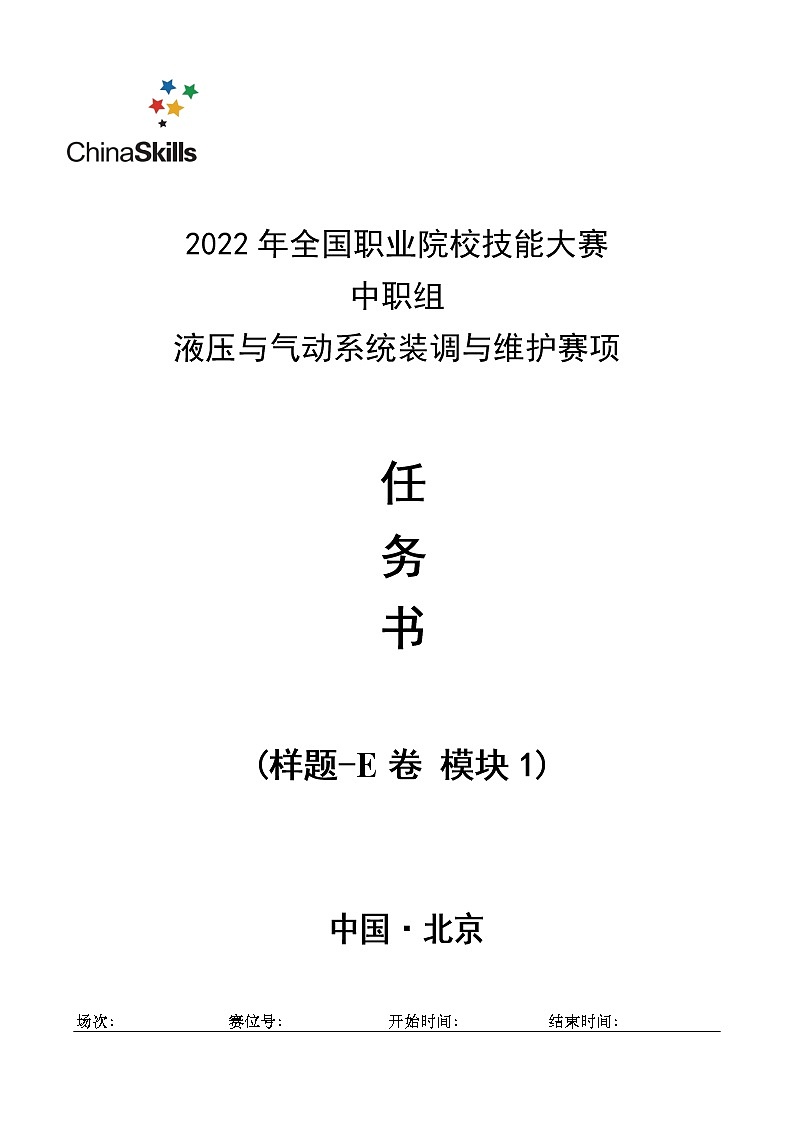
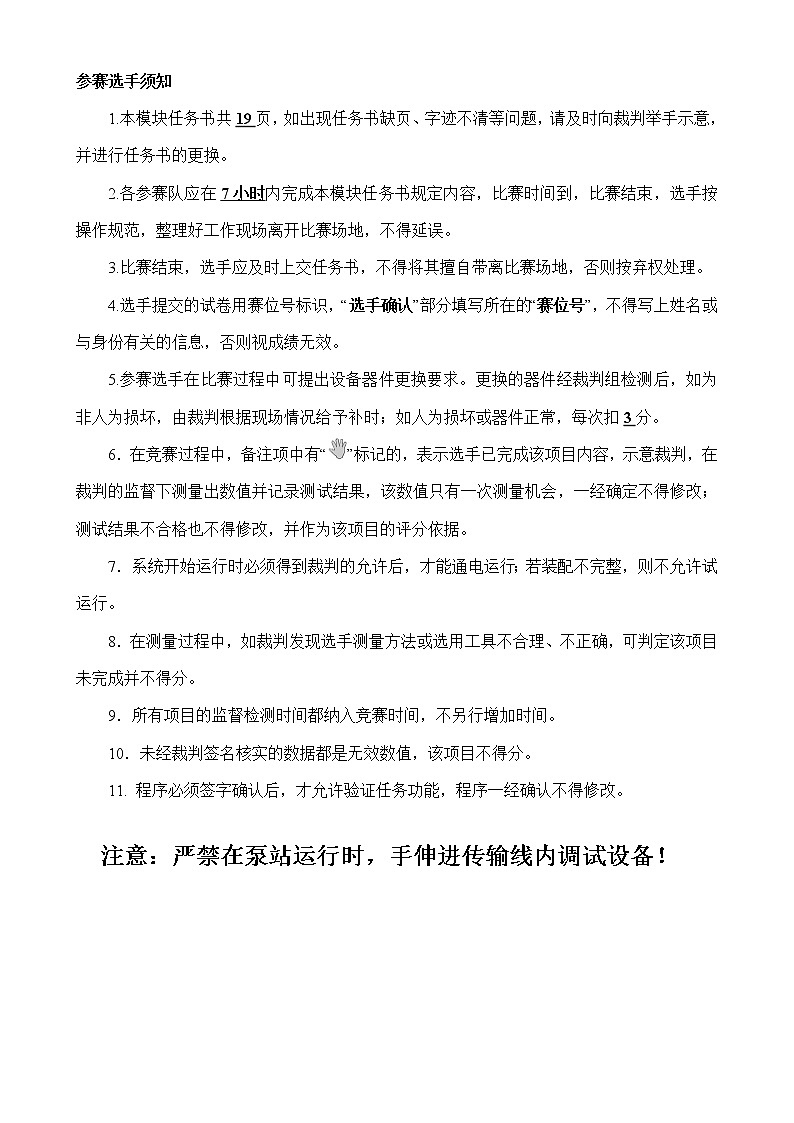
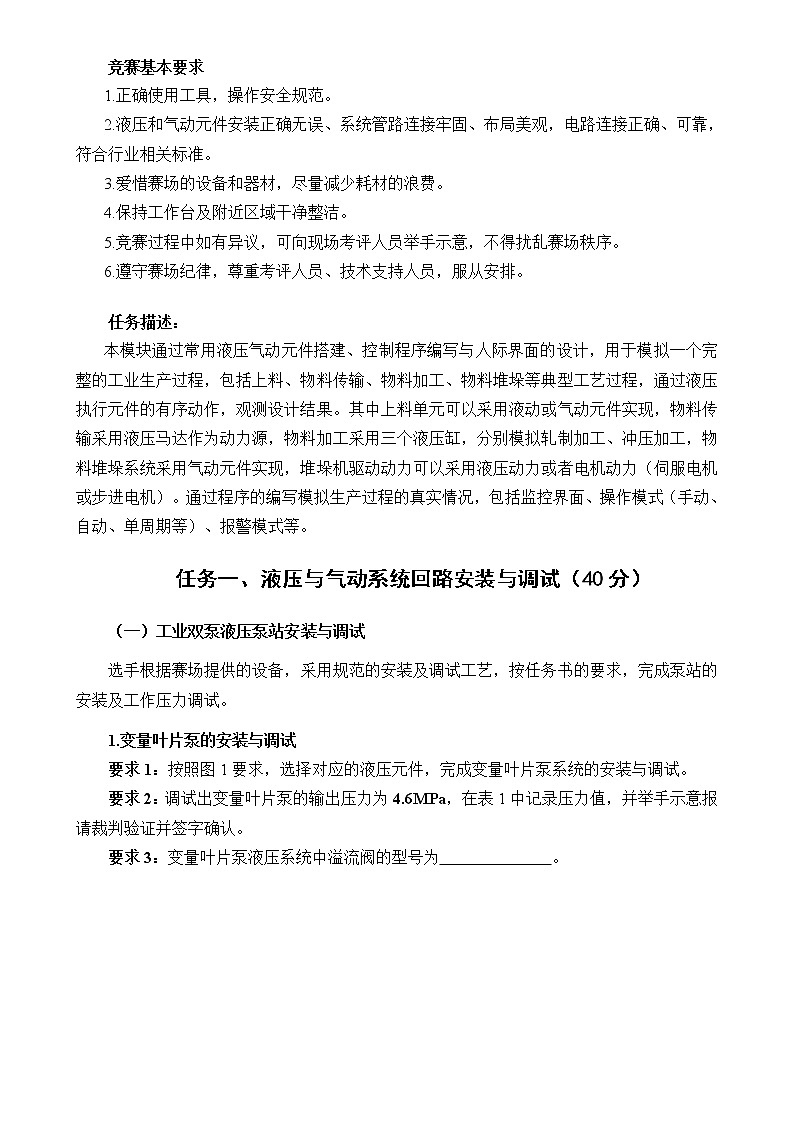
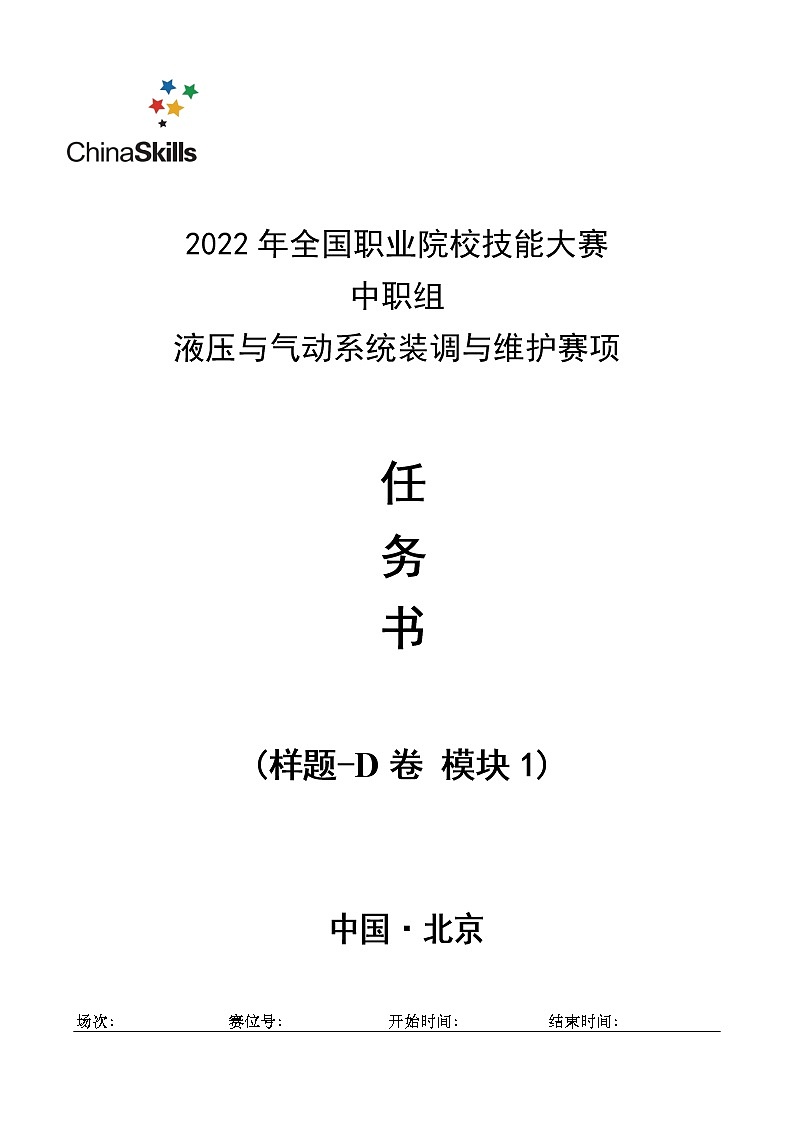
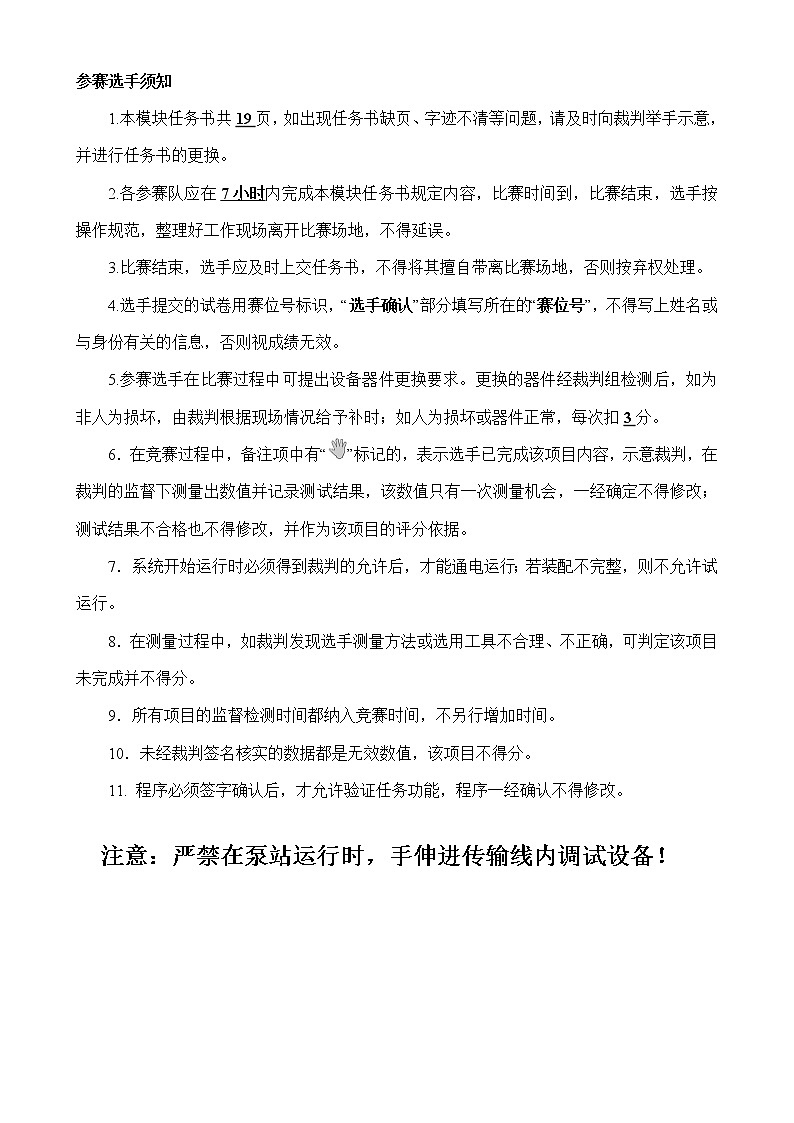
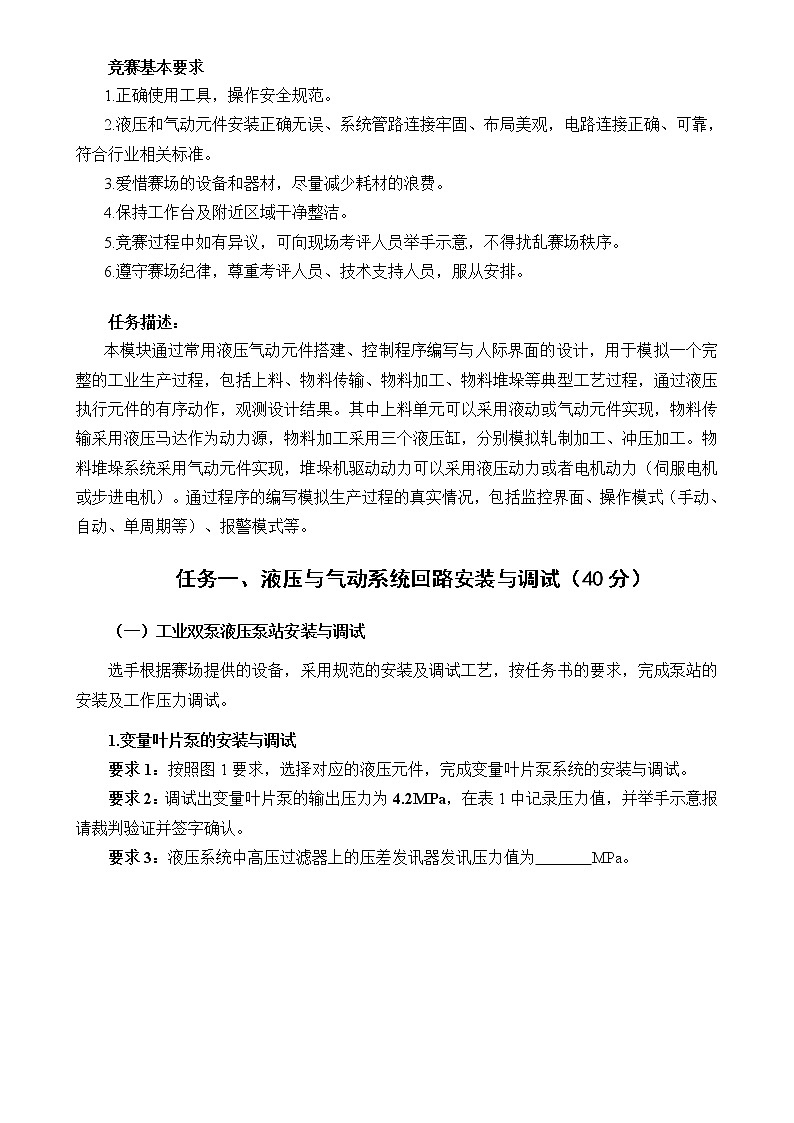
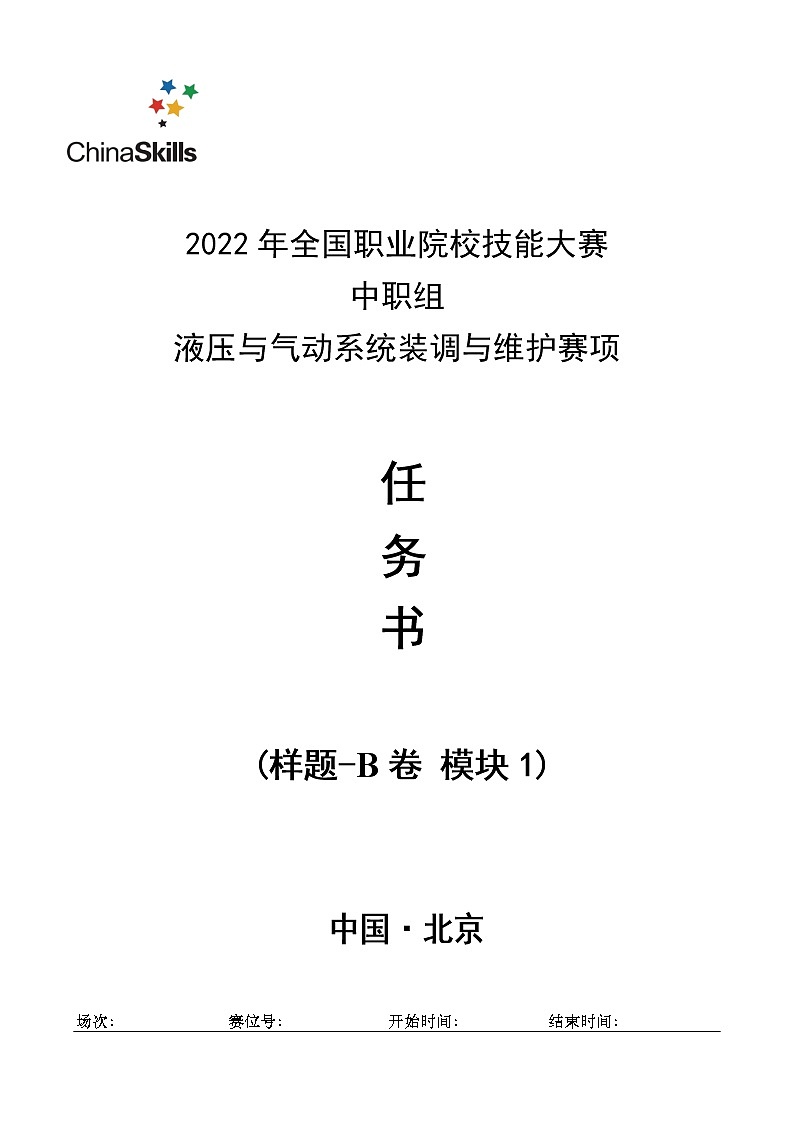
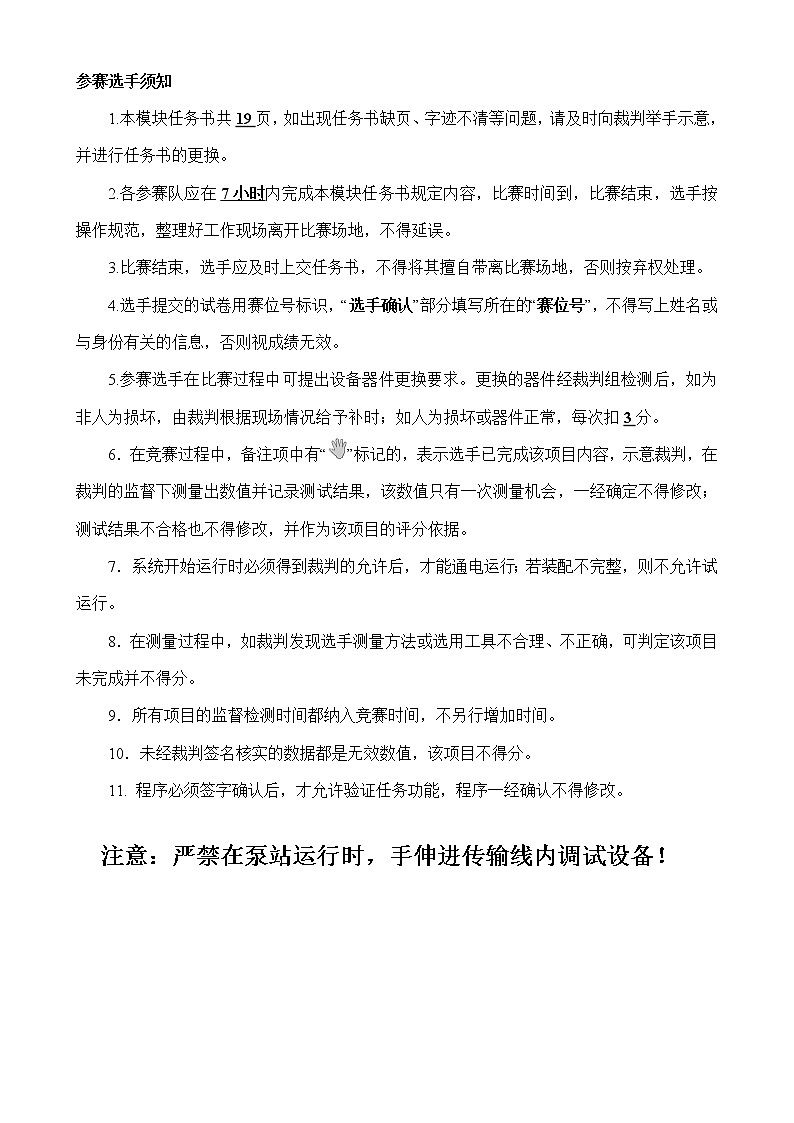
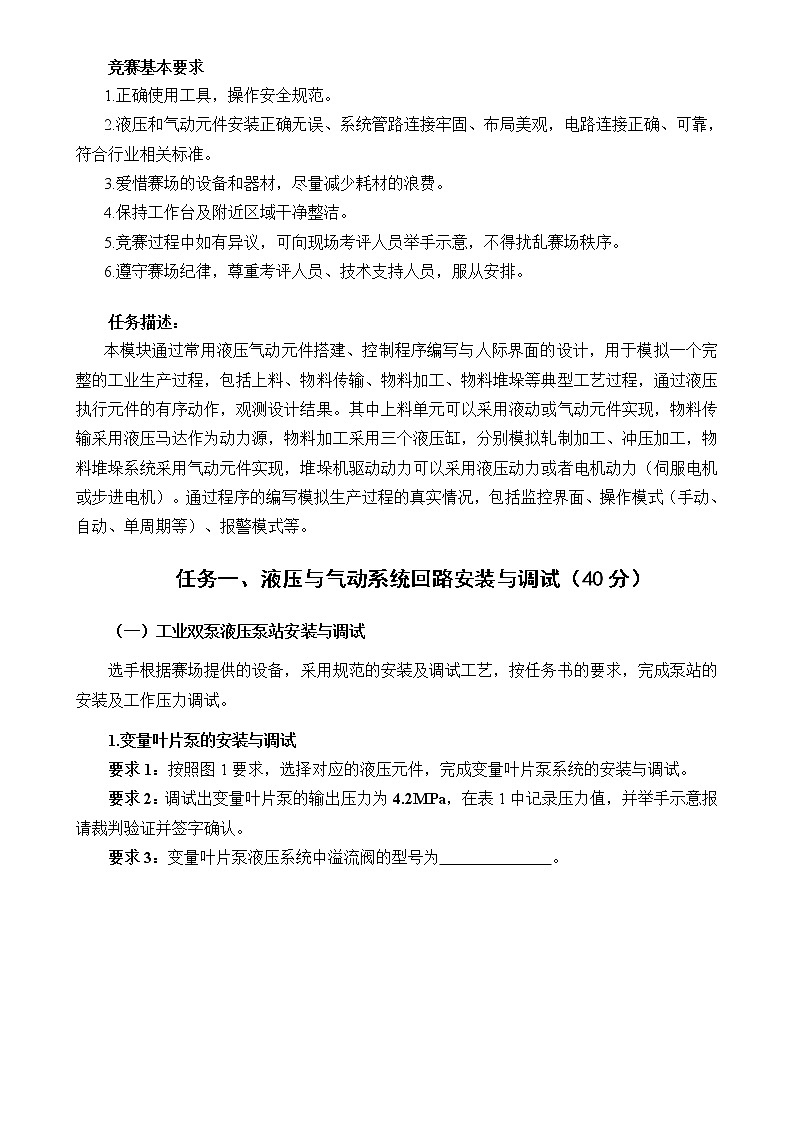
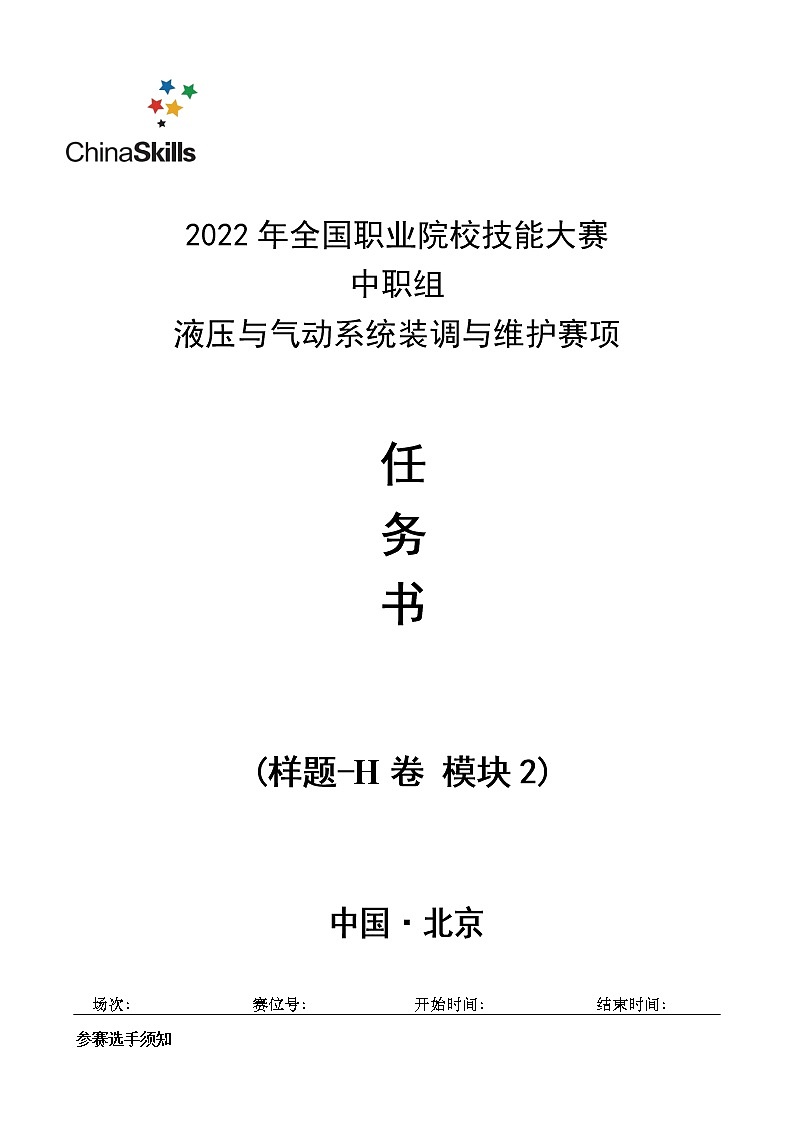
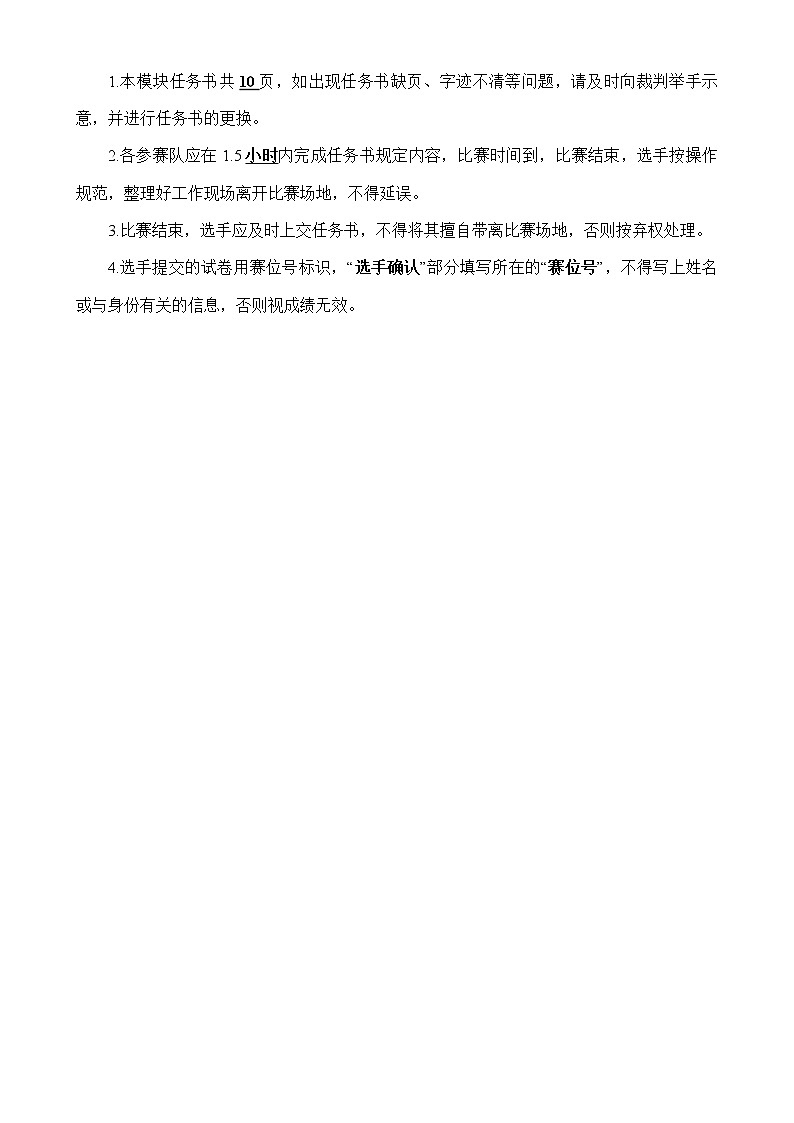
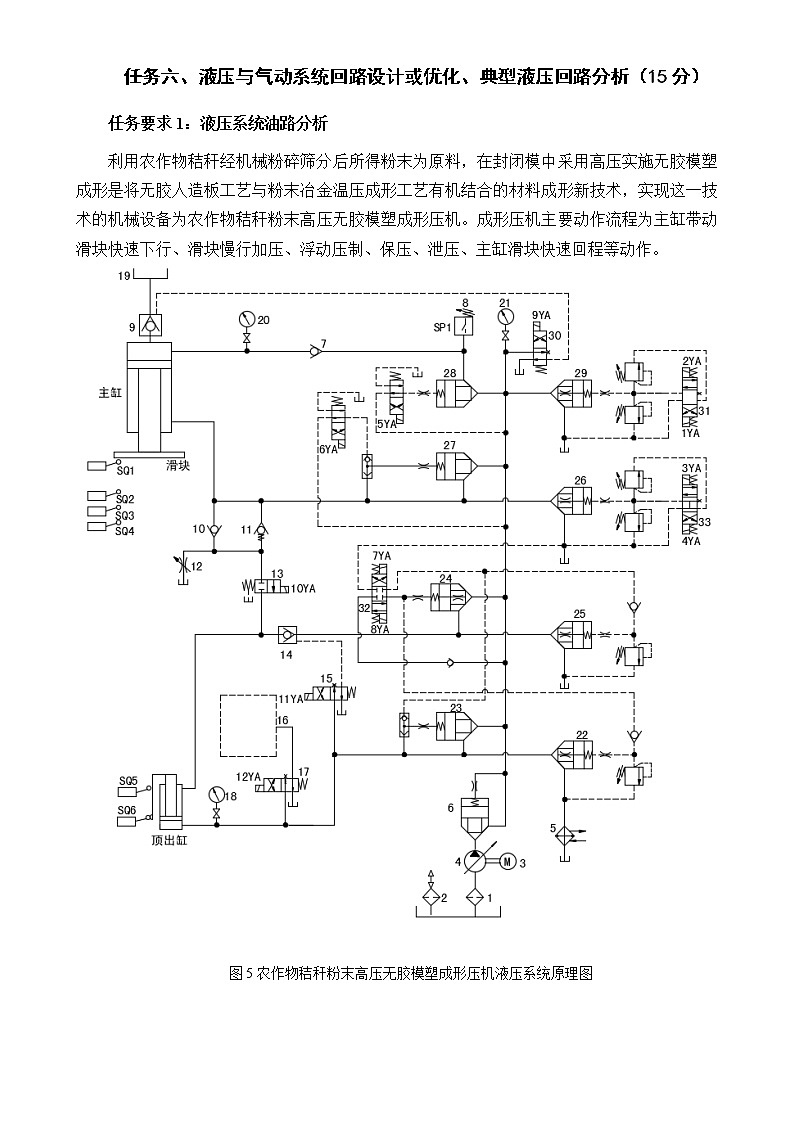
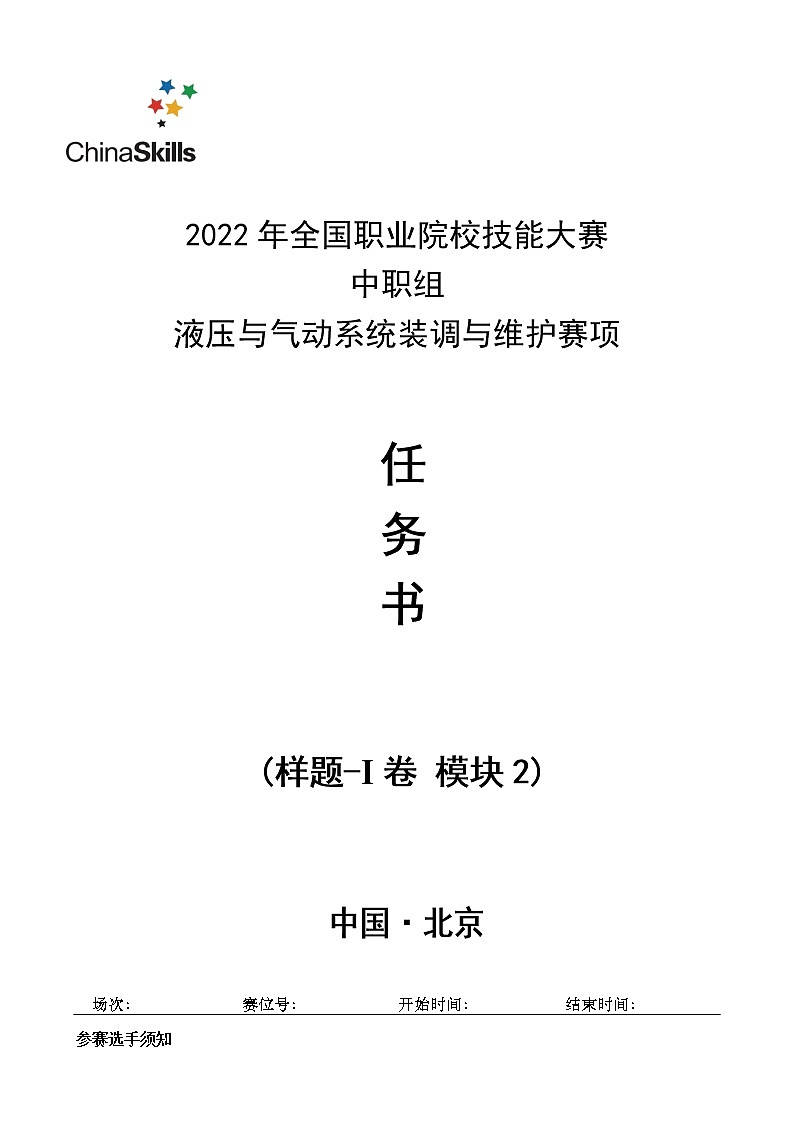
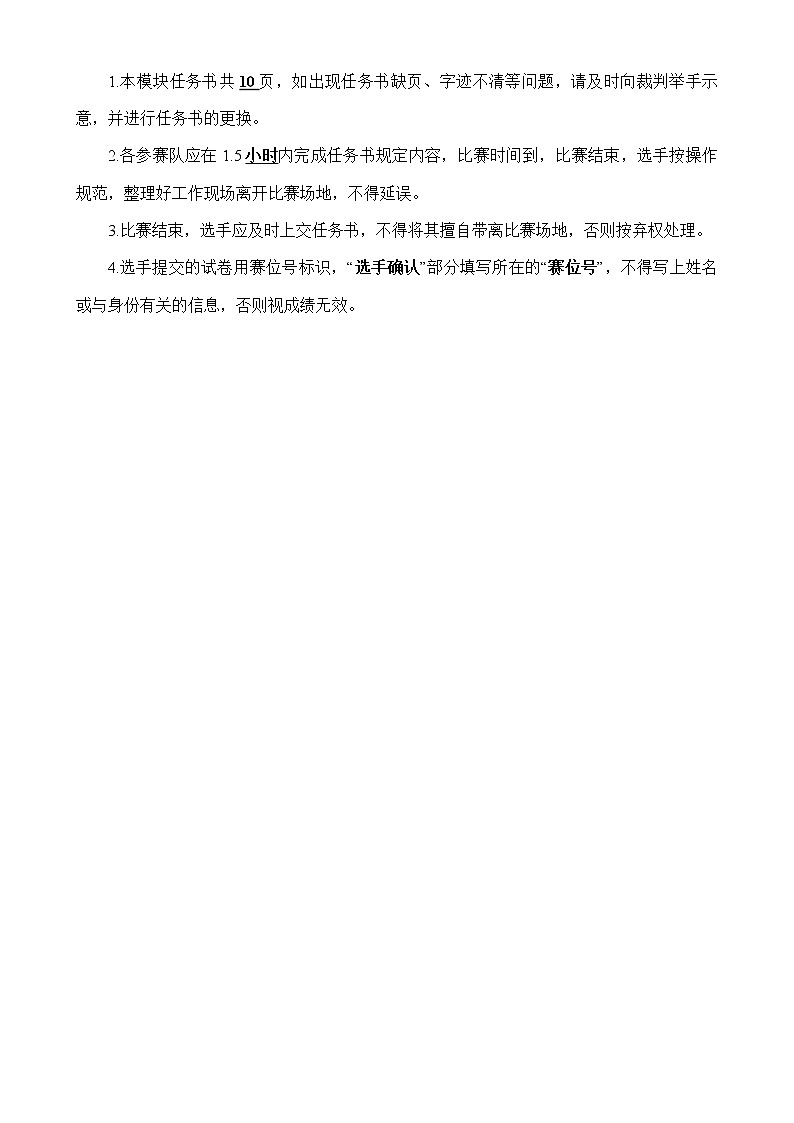
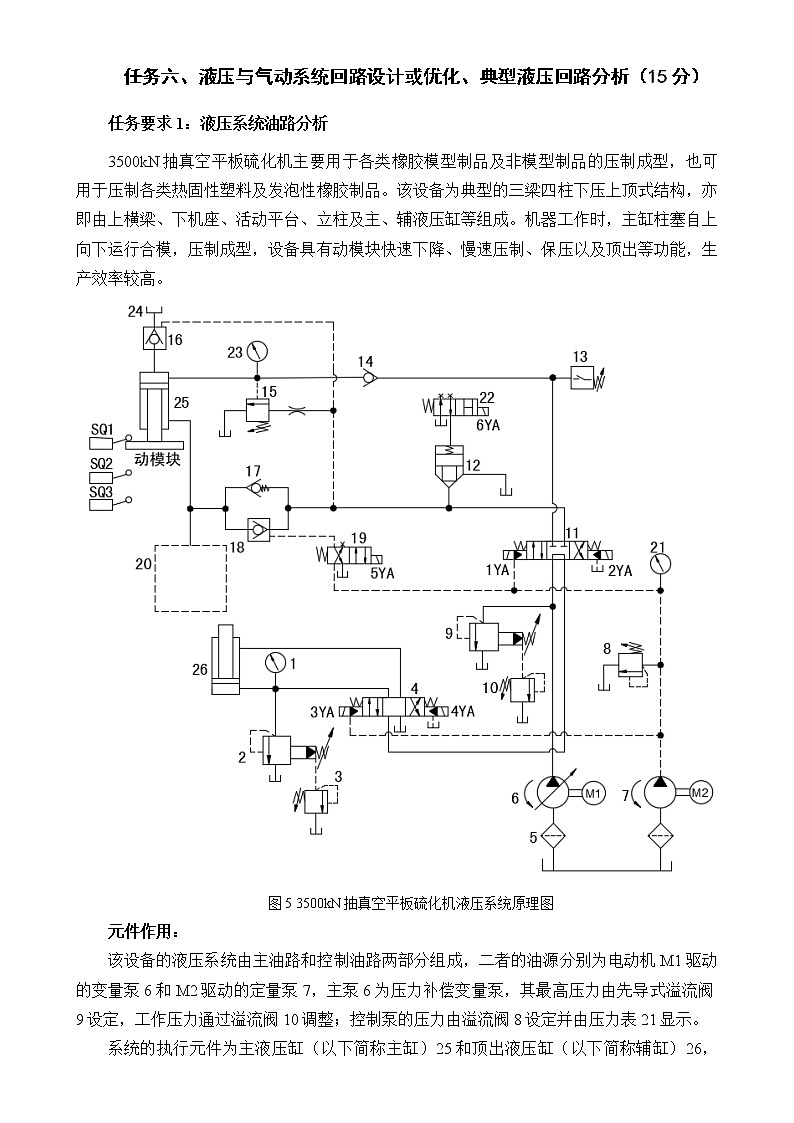
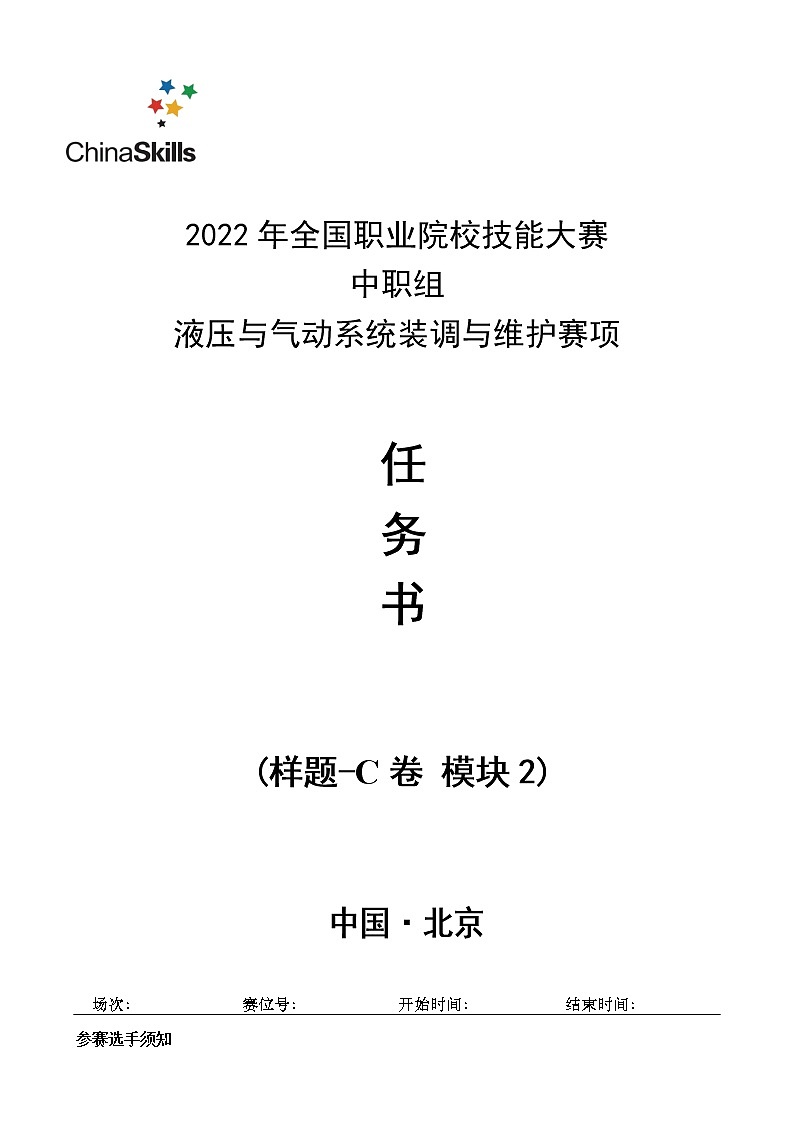
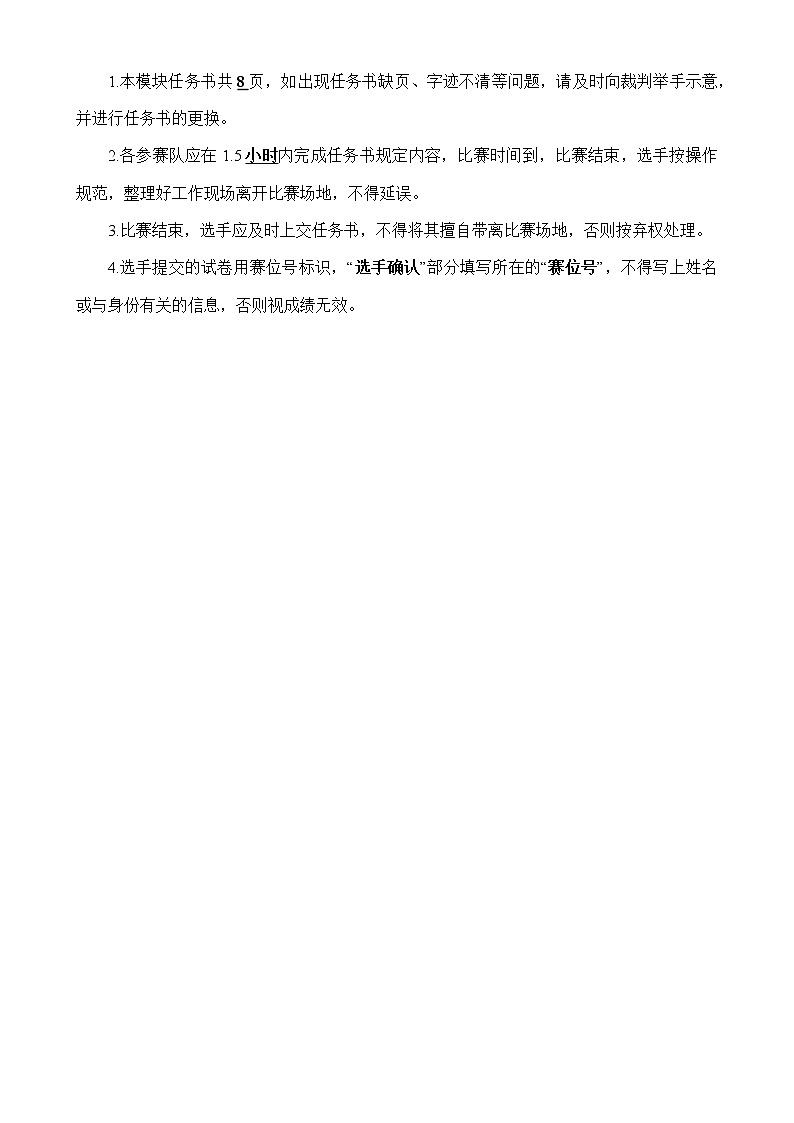
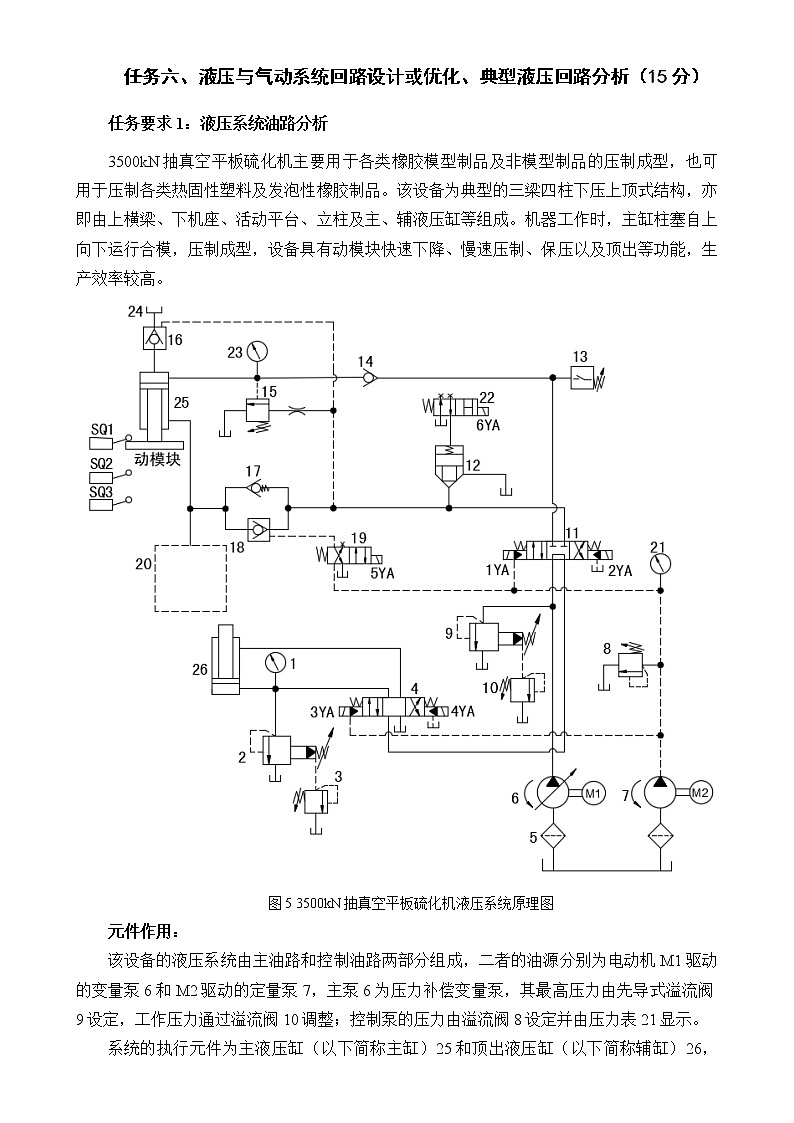
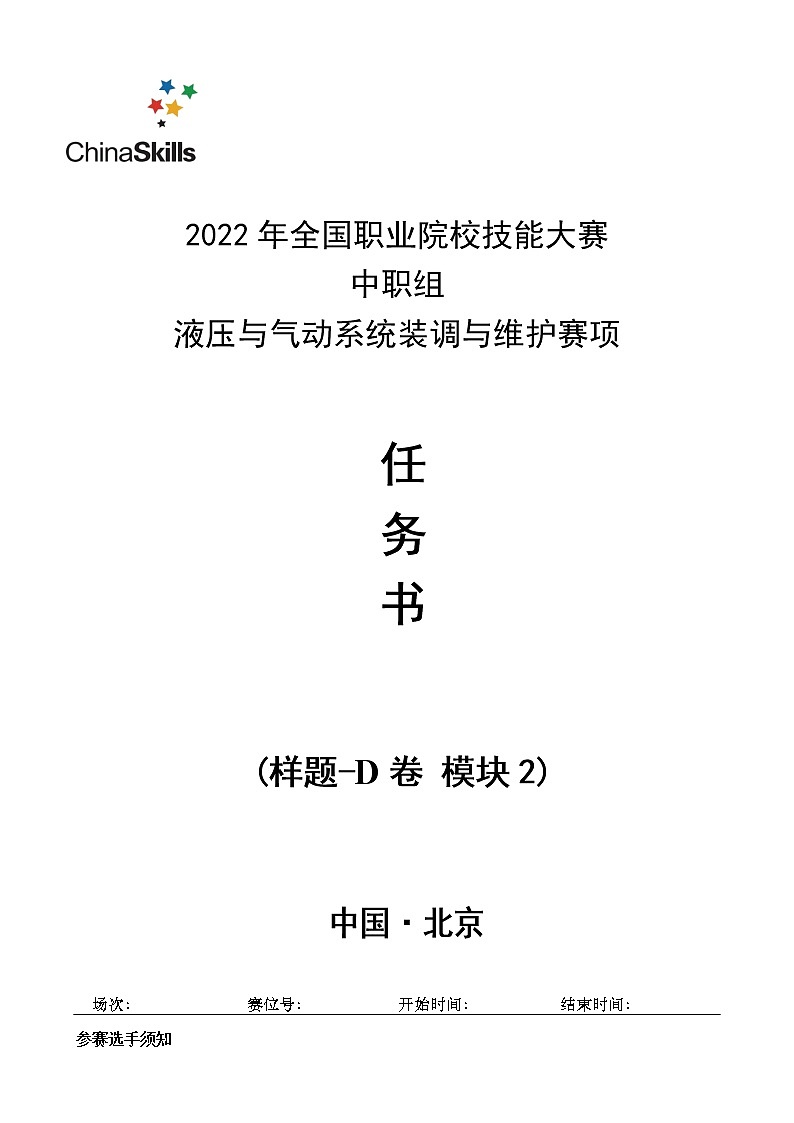
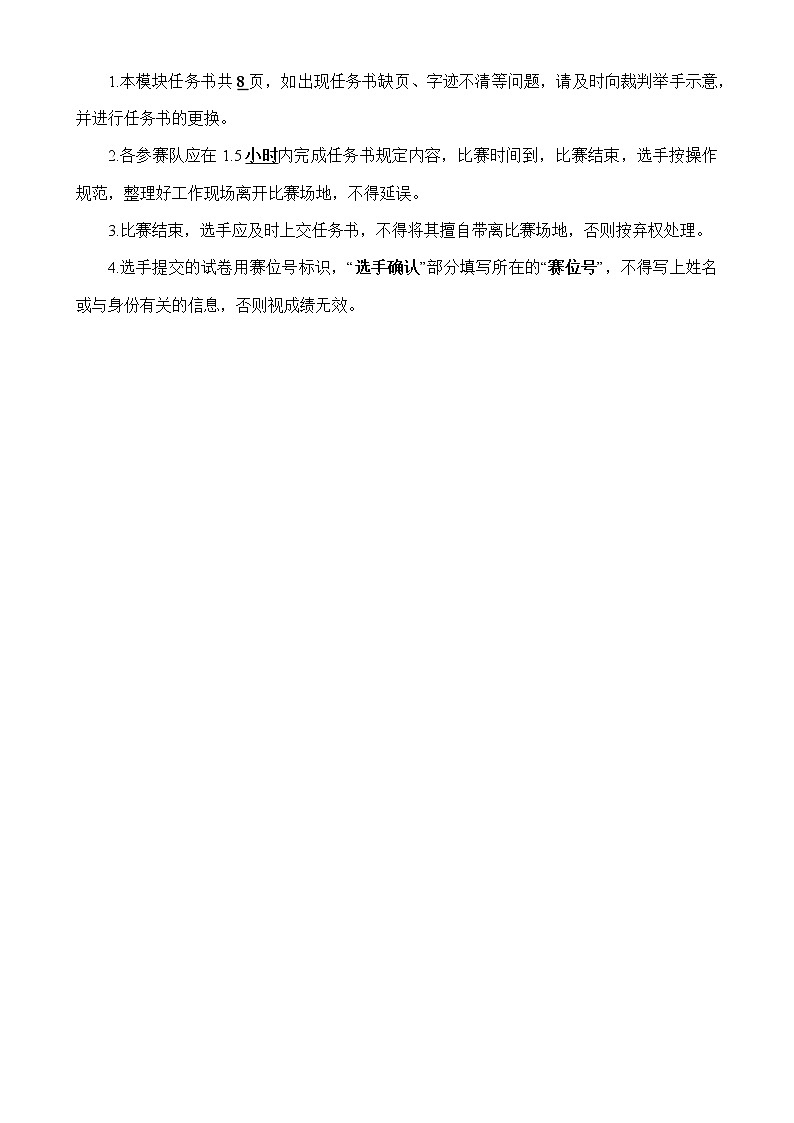
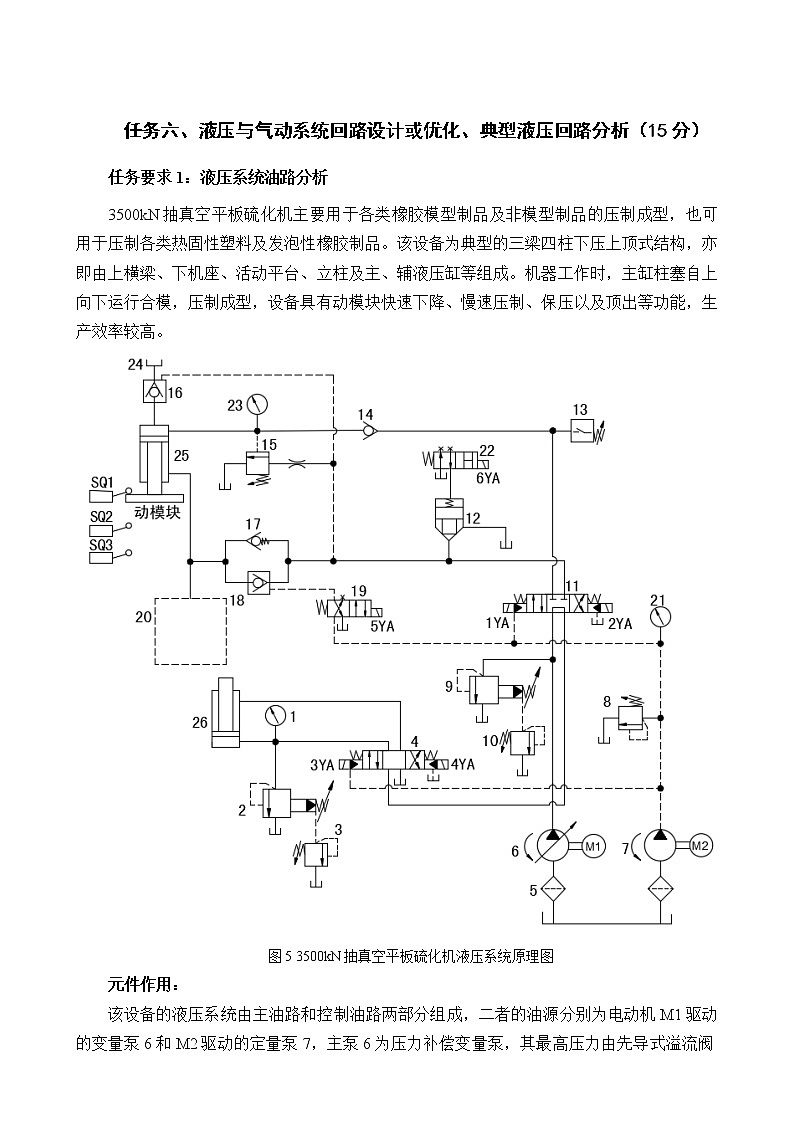
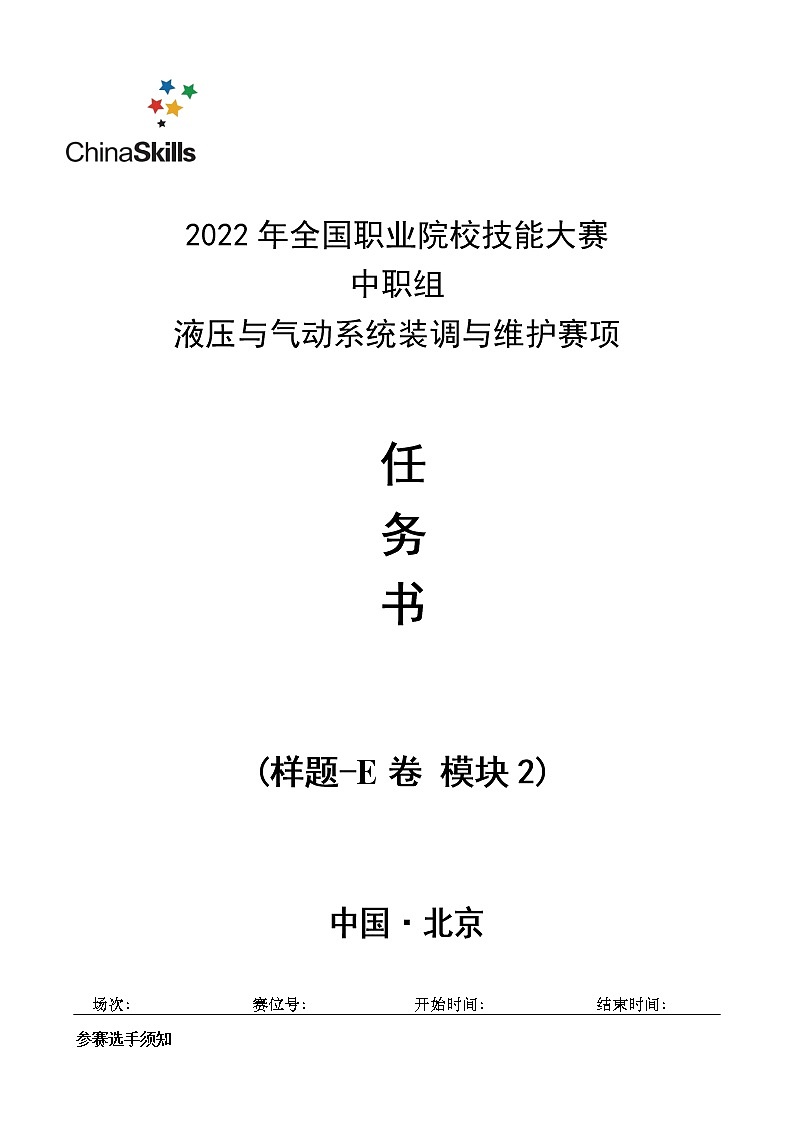
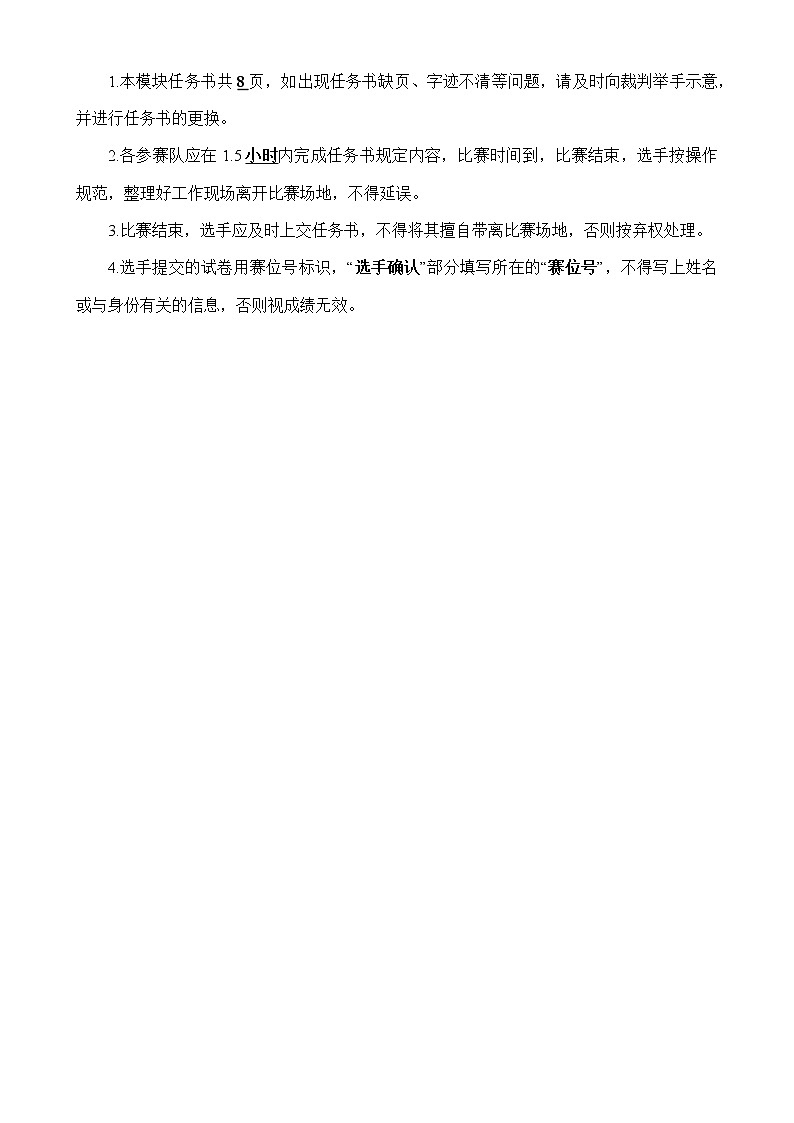
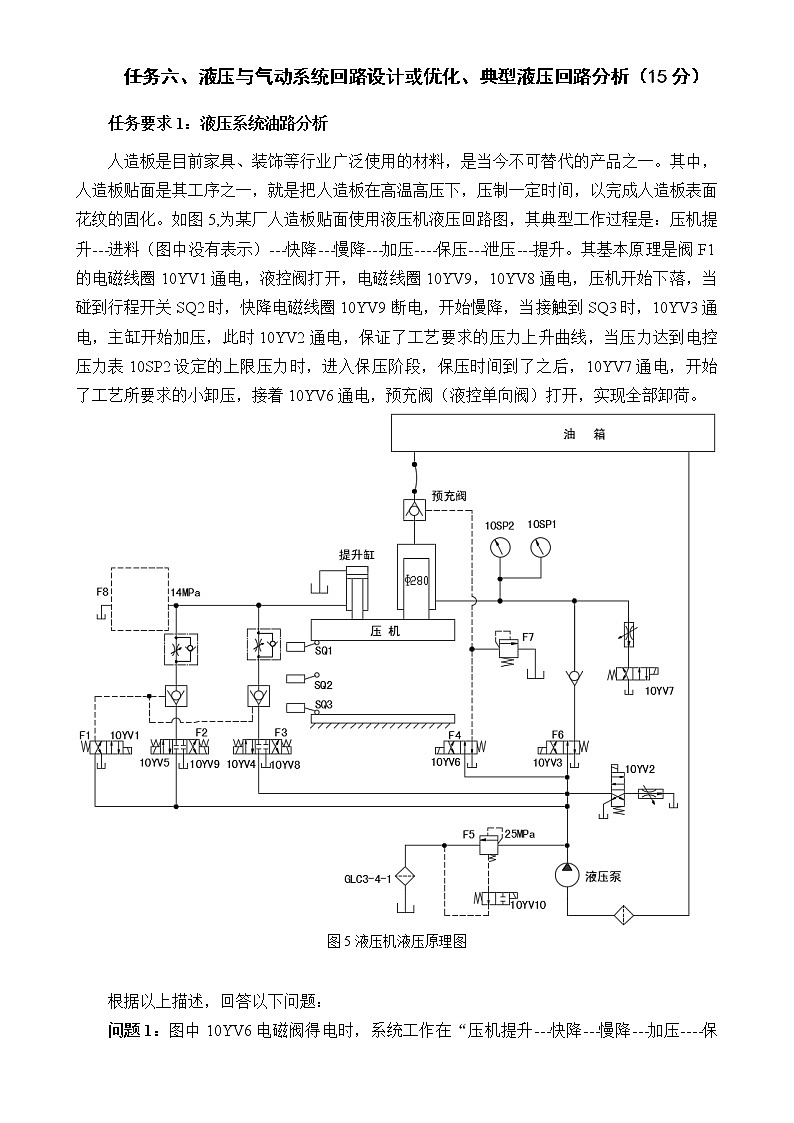
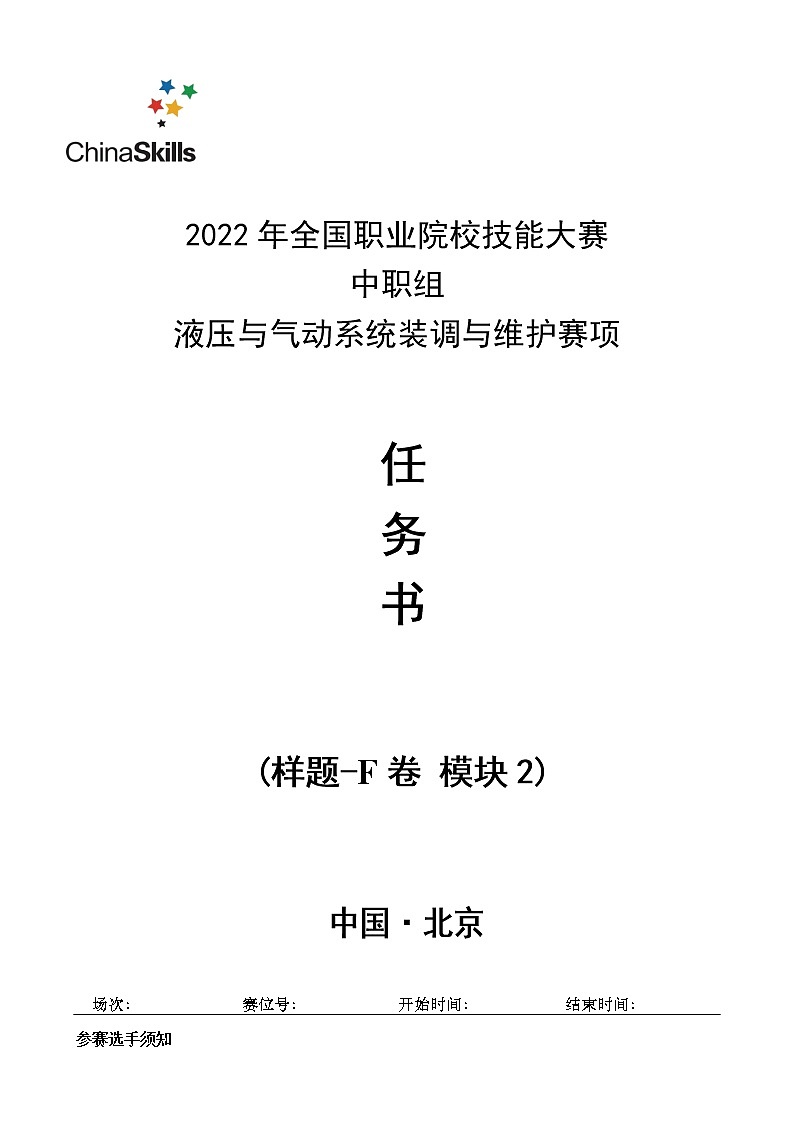
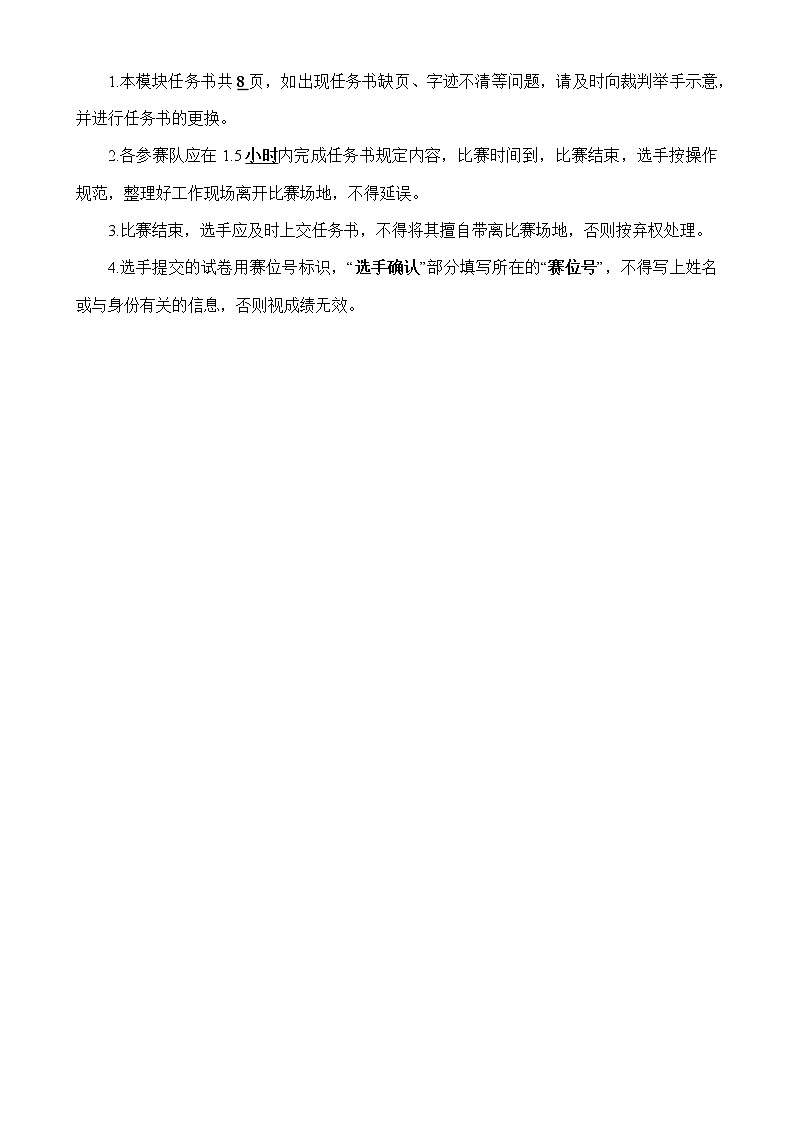
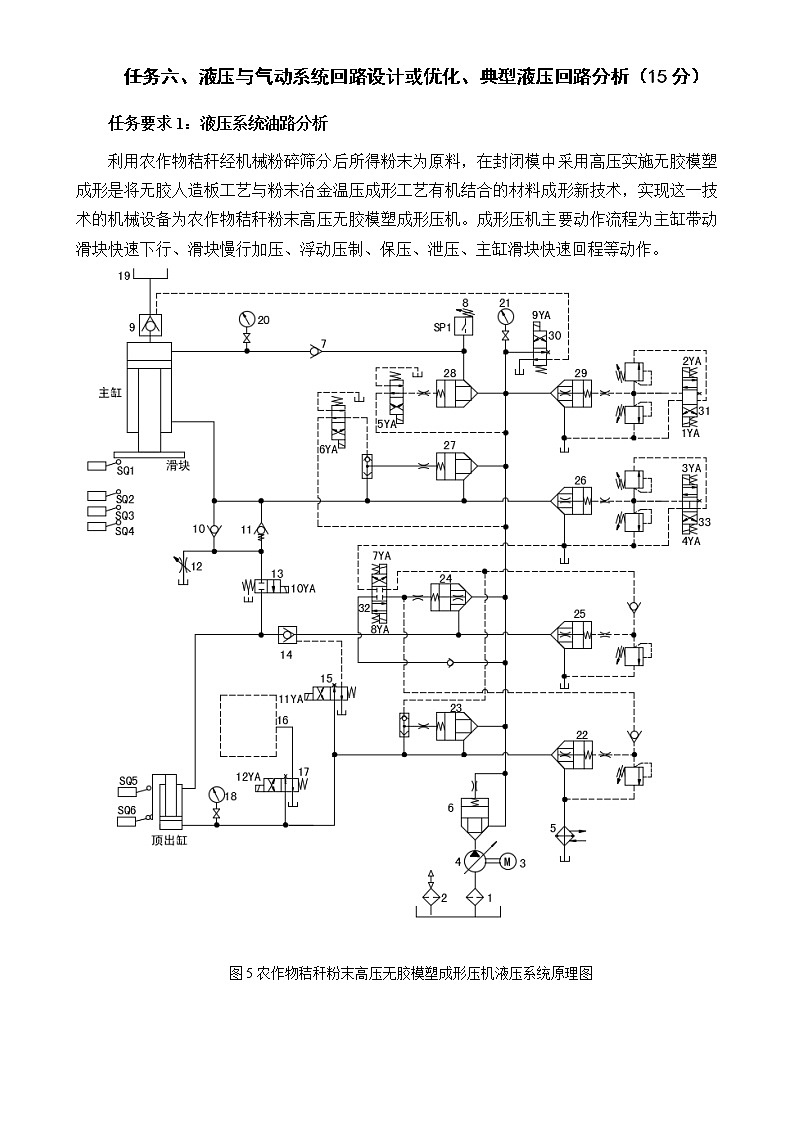
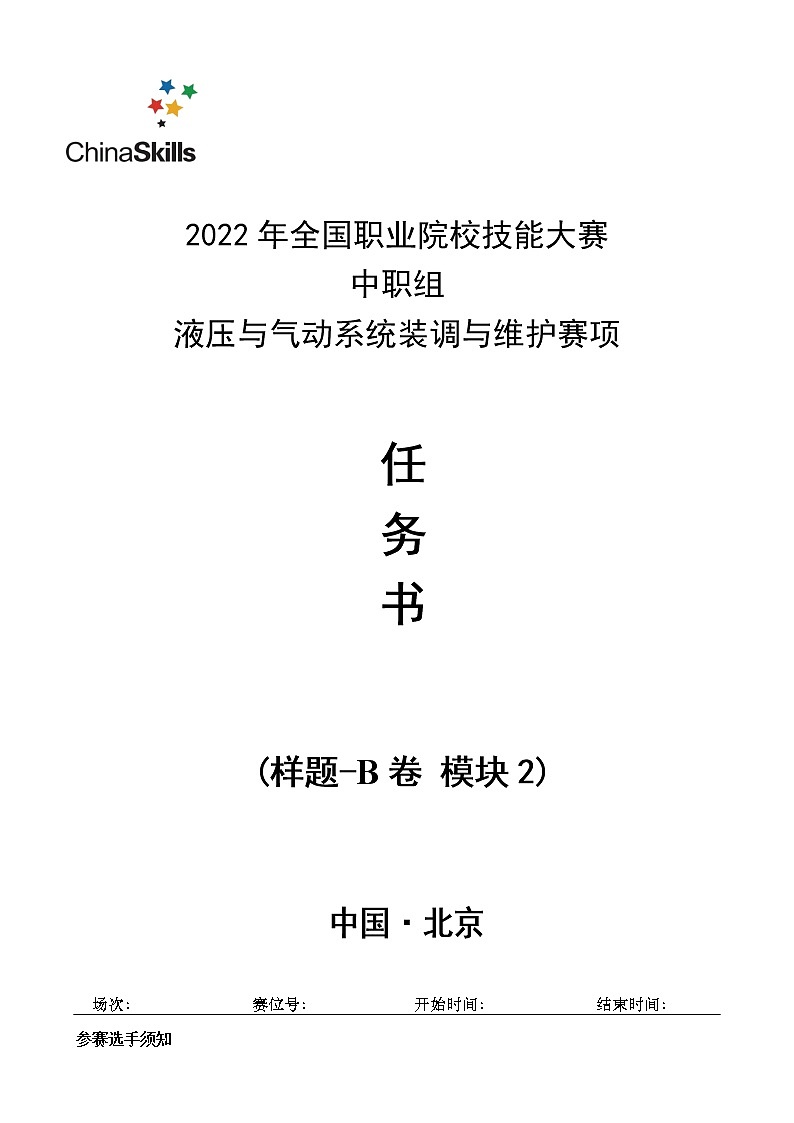
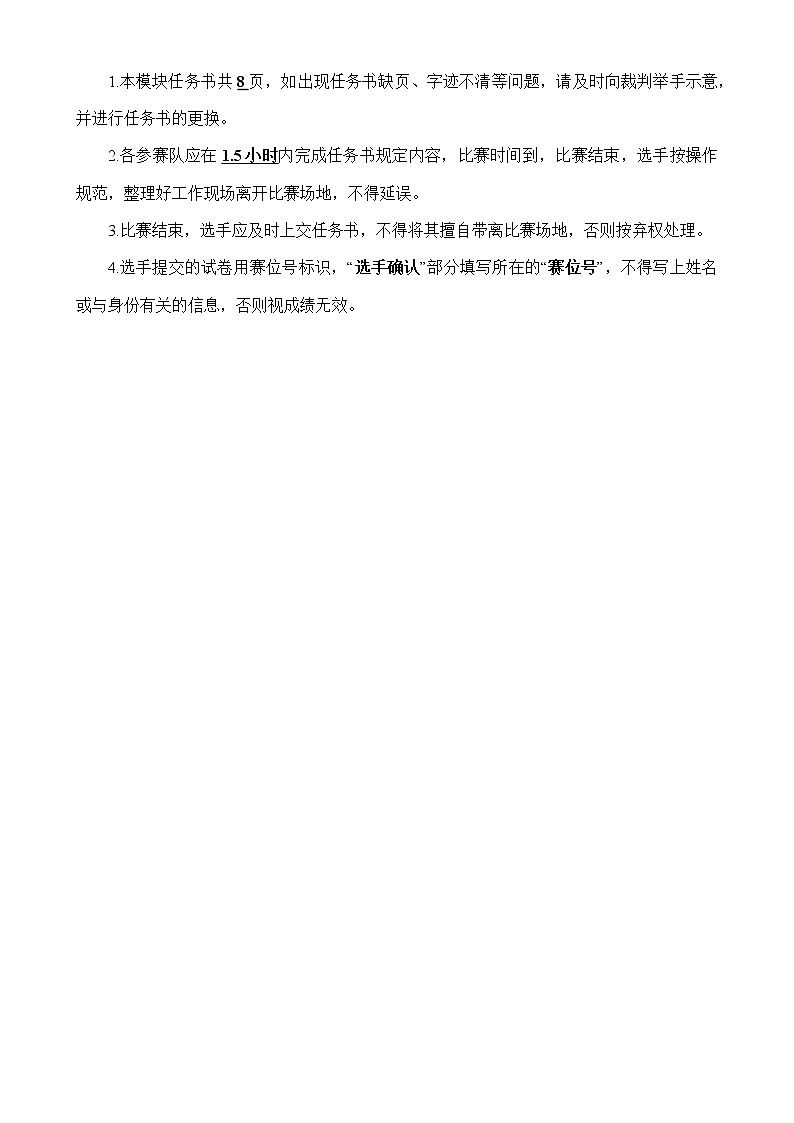
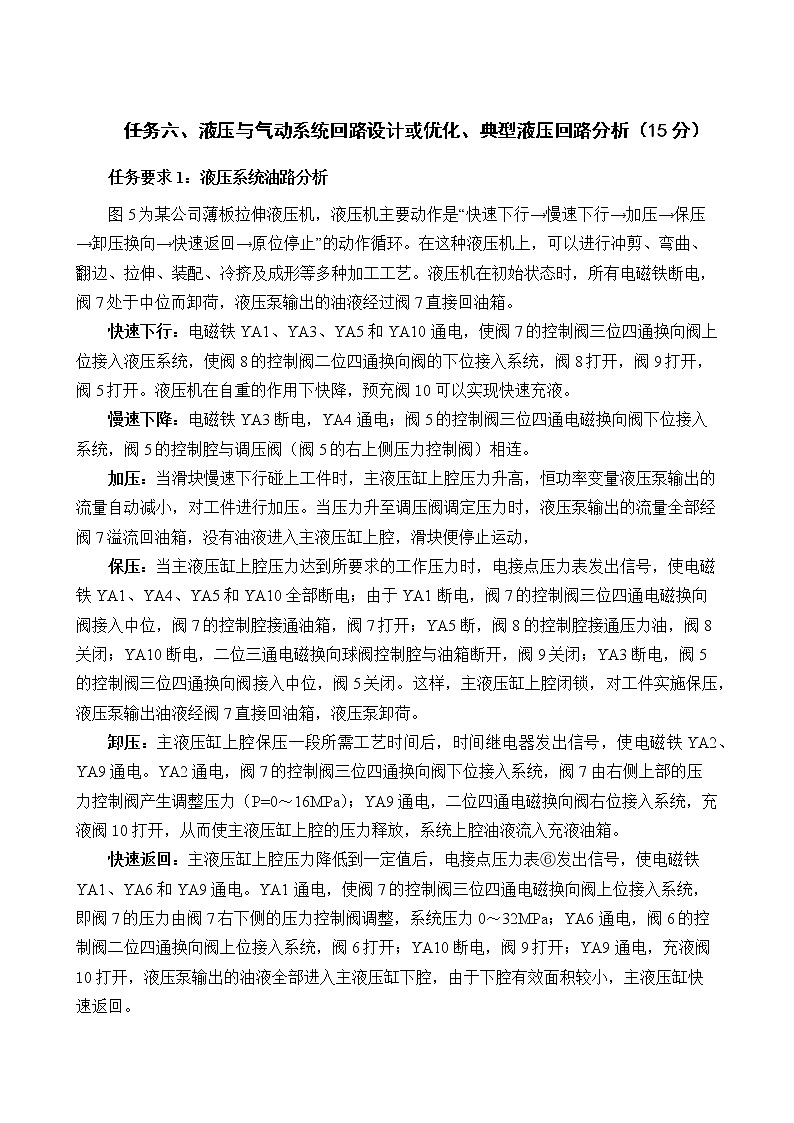
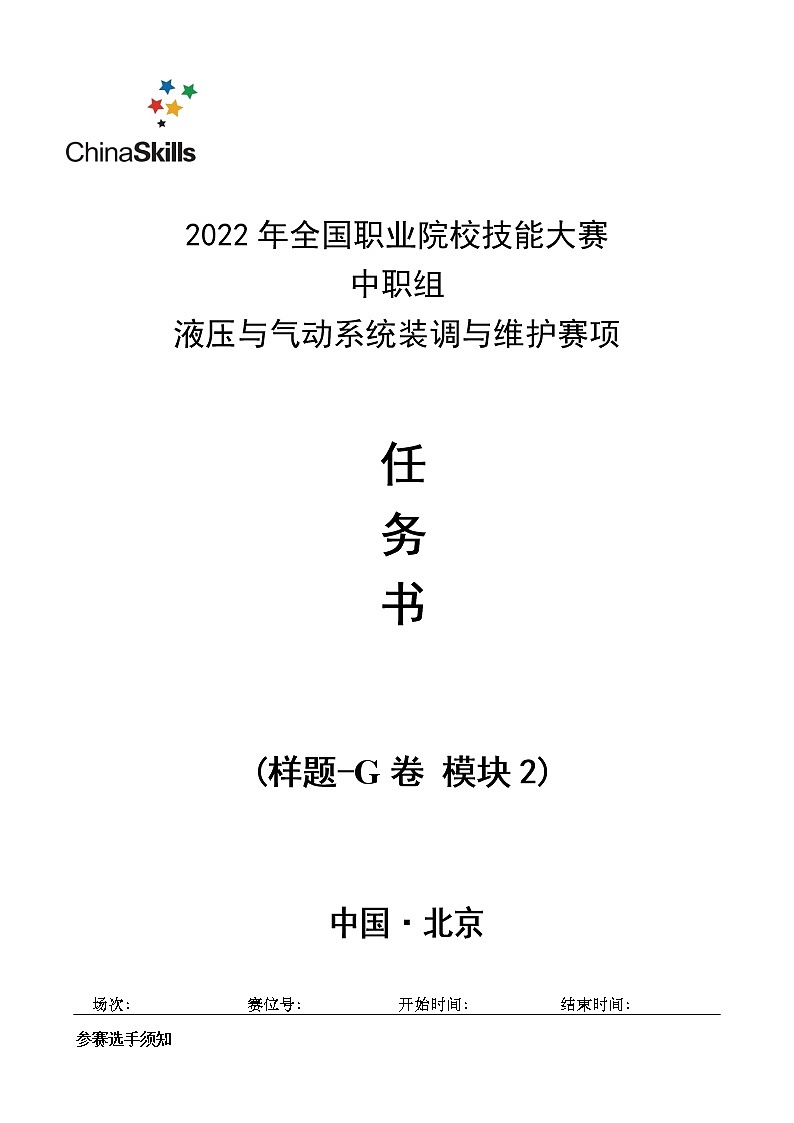
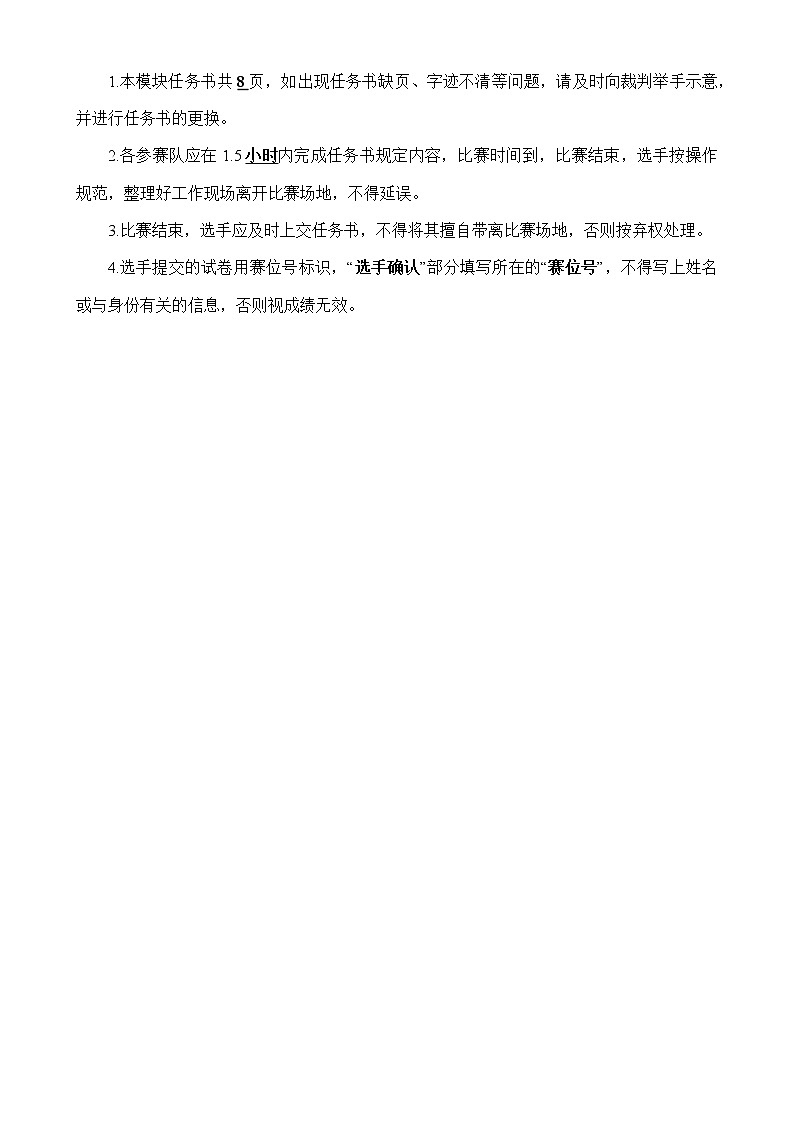
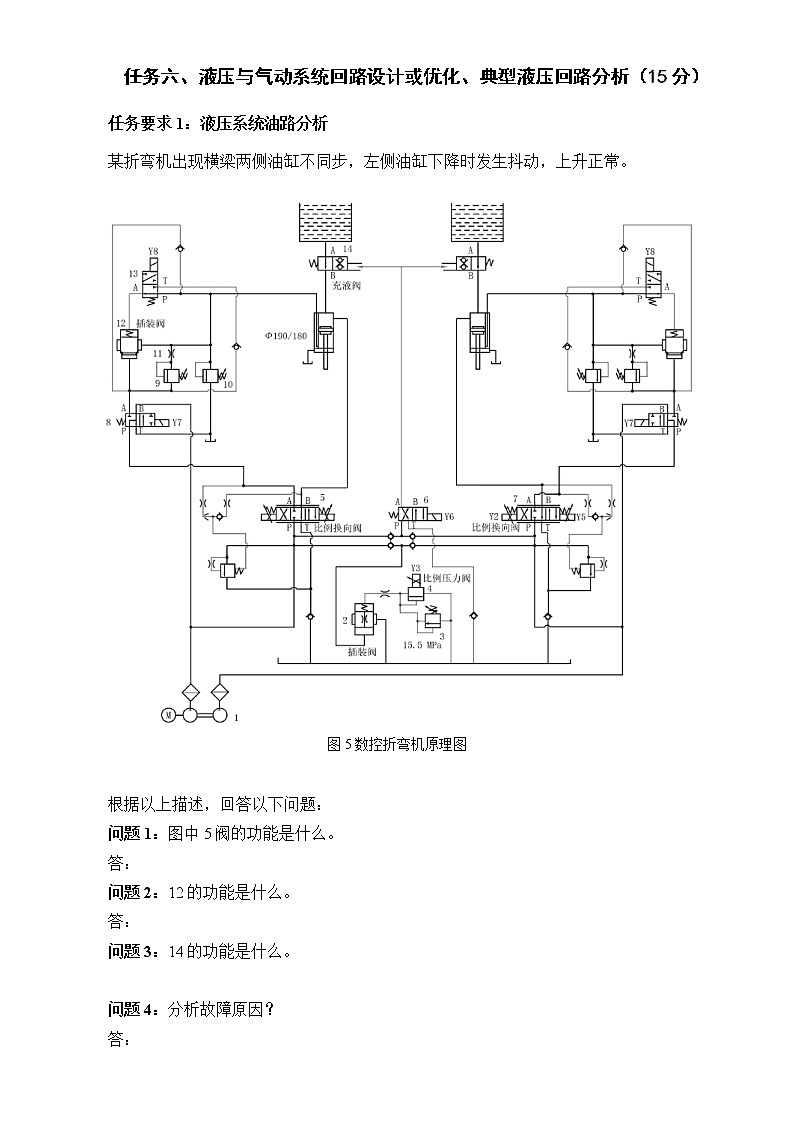
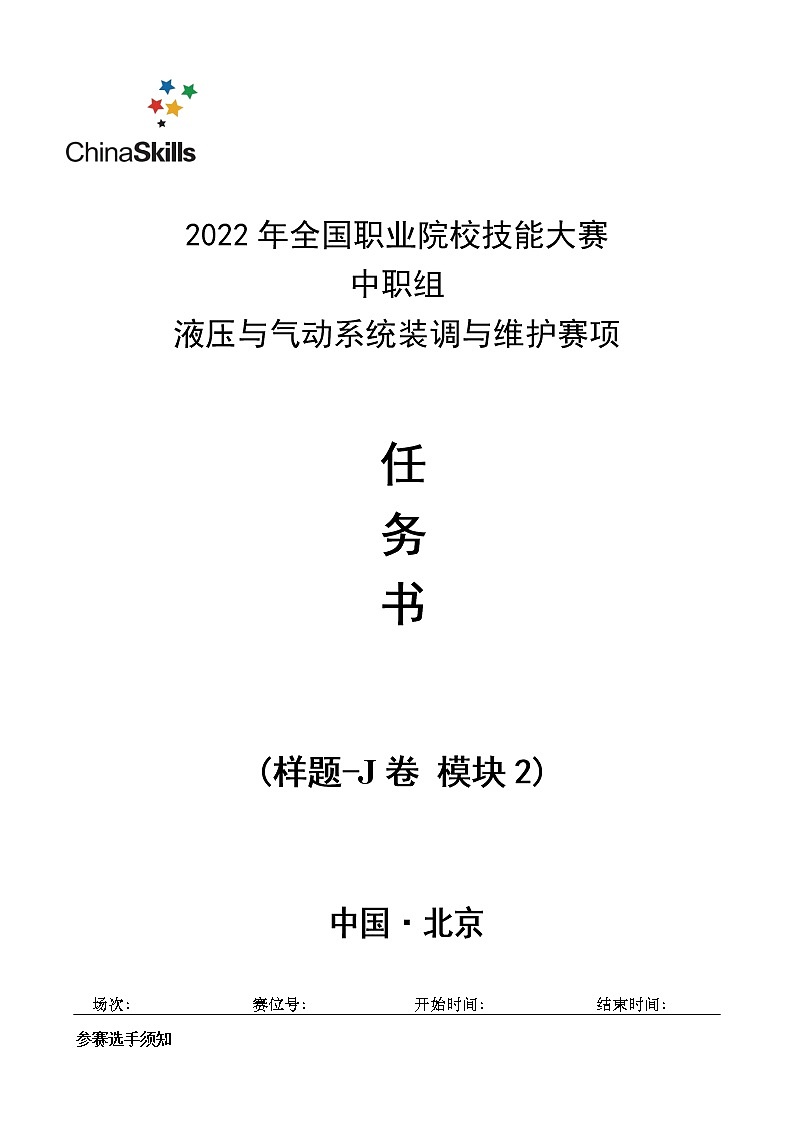
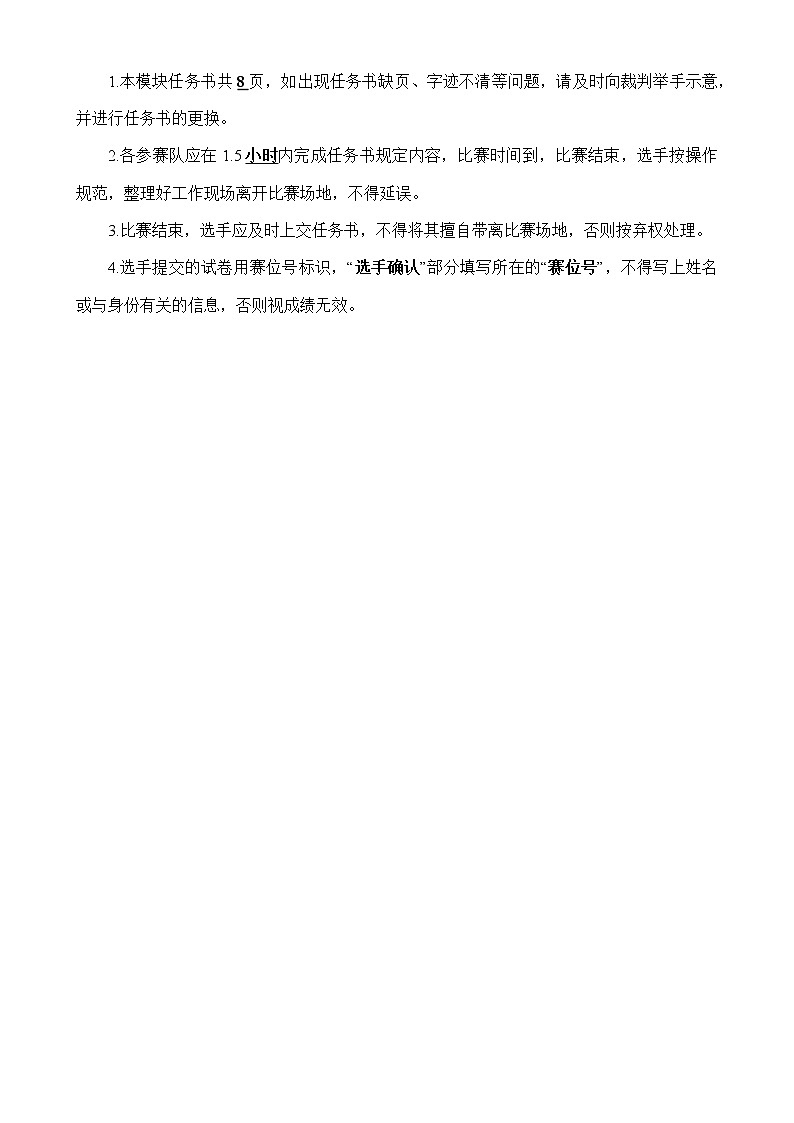
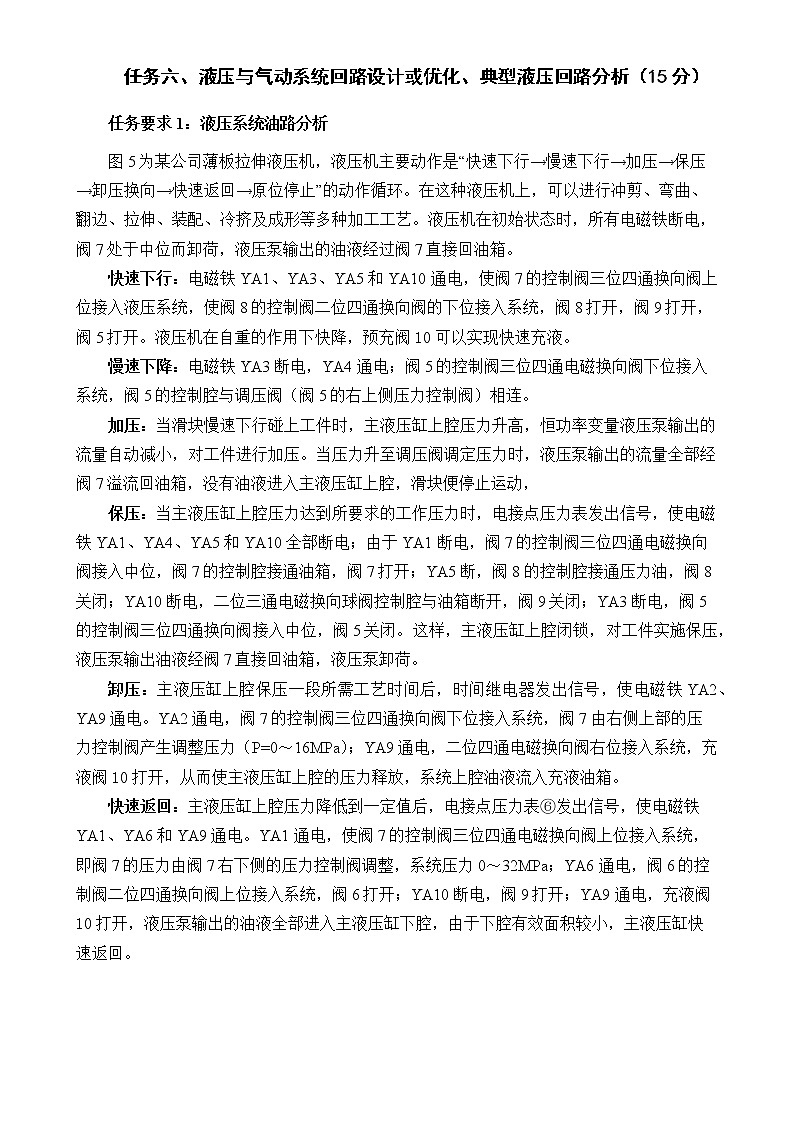
2022年全国职业院校技能大赛中职组 液压与气动系统装调与维护赛项模拟赛题(word版)
展开
2022年全国职业院校技能大赛
中职组
液压与气动系统装调与维护赛项
任
务
书
(样题-H卷 模块1)
中国·北京
场次: 赛位号: 开始时间: 结束时间:
参赛选手须知
1.本模块任务书共19页,如出现任务书缺页、字迹不清等问题,请及时向裁判举手示意,并进行任务书的更换。
2.各参赛队应在7小时内完成本模块任务书规定内容,比赛时间到,比赛结束,选手按操作规范,整理好工作现场离开比赛场地,不得延误。
3.比赛结束,选手应及时上交任务书,不得将其擅自带离比赛场地,否则按弃权处理。
4.选手提交的试卷用赛位号标识,“选手确认”部分填写所在的“赛位号”,不得写上姓名或与身份有关的信息,否则视成绩无效。
5.参赛选手在比赛过程中可提出设备器件更换要求。更换的器件经裁判组检测后,如为非人为损坏,由裁判根据现场情况给予补时;如人为损坏或器件正常,每次扣3分。
6.在竞赛过程中,备注项中有“”标记的,表示选手已完成该项目内容,示意裁判,在裁判的监督下测量出数值并记录测试结果,该数值只有一次测量机会,一经确定不得修改;测试结果不合格也不得修改,并作为该项目的评分依据。
7.系统开始运行时必须得到裁判的允许后,才能通电运行;若装配不完整,则不允许试运行。
8.在测量过程中,如裁判发现选手测量方法或选用工具不合理、不正确,可判定该项目未完成并不得分。
9.所有项目的监督检测时间都纳入竞赛时间,不另行增加时间。
10.未经裁判签名核实的数据都是无效数值,该项目不得分。
11. 程序必须签字确认后,才允许验证任务功能,程序一经确认不得修改。
注意:严禁在泵站运行时,手伸进传输线内调试设备!
竞赛基本要求
1.正确使用工具,操作安全规范。
2.液压和气动元件安装正确无误、系统管路连接牢固、布局美观,电路连接正确、可靠,符合行业相关标准。
3.爱惜赛场的设备和器材,尽量减少耗材的浪费。
4.保持工作台及附近区域干净整洁。
5.竞赛过程中如有异议,可向现场考评人员举手示意,不得扰乱赛场秩序。
6.遵守赛场纪律,尊重考评人员、技术支持人员,服从安排。
任务描述:
本模块通过常用液压气动元件搭建、控制程序编写与人际界面的设计,用于模拟一个完整的工业生产过程,包括上料、物料传输、物料加工、物料堆垛等典型工艺过程,通过液压执行元件的有序动作,观测设计结果。其中上料单元可以采用液动或气动元件实现,物料传输采用液压马达作为动力源,物料加工采用三个液压缸,分别模拟轧制加工、冲压加工,物料堆垛系统采用气动元件实现,堆垛机驱动动力可以采用液压动力或者电机动力(伺服电机或步进电机)。通过程序的编写模拟生产过程的真实情况,包括监控界面、操作模式(手动、自动、单周期等)、报警模式等。
任务一、液压与气动系统回路安装与调试(40分)
(一)工业双泵液压泵站安装与调试
选手根据赛场提供的设备,采用规范的安装及调试工艺,按任务书的要求,完成泵站的安装及工作压力调试。
1.变量叶片泵的安装与调试
要求1:按照图1要求,选择对应的液压元件,完成变量叶片泵系统的安装与调试。
要求2:调试出变量叶片泵的输出压力为4.4MPa,在表1中记录压力值,并举手示意报请裁判验证并签字确认。
要求3:根据要求2,变量叶片泵限压压力应 4.2MPa(填“大于”或“小于”)。
图1 变量叶片泵系统调压回路
表1 变量叶片泵的输出压力确认表
序号
泵 源
功能要求
P2(MPa)
选手确认
(填赛位号)
裁判确认
(签字确认)
备注
1
变量叶片泵
系统压力
2.定量柱塞泵的安装与调试
要求1:按照图2要求,选择对应的液压元件,完成定量柱塞泵系统的安装与调试。
要求2:定量柱塞泵系统采用溢流阀并联控制方式,通过电磁换向阀进行一、二级压力切换,系统回油采用冷却器冷却,根据现场液压泵站配置,将图2补充完整并进行管路搭接。
要求3:调试出定量柱塞泵输出一级压力为5.5MPa,二级压力为3.5MPa,在表2中记录压力表压力值,并举手示意报请裁判签字确认。
图2 定量柱塞泵系统调压回路
表2 定量柱塞泵的输出压力确认表
序号
泵源
功能要求
P2(MPa)
选手确认
(填赛位号)
裁判确认
(签字确认)
备注
1
定量柱塞泵
一级压力
2
二级压力
(二)液压系统回路搭建与调试
根据赛场所提供设备,选手按任务书各液压系统回路的要求,选择适当的液压阀,组建任务书要求的板式回路或叠加回路,完成液压系统安装与调试,注意安装及调试工艺须规范。
图3 全自动轧钢冲压模拟装置液压回路图
1.物料传输单元
本单元采用液压马达通过机械装置,带动传输系统运行,实现物料的传输。
选用叶片泵油路系统供油,物料传输单元油路系统在满足如下要求时,进行液压系统安装与调试,注意安装及调试工艺须规范。
要求1:采用电磁比例换向阀控制液压马达转动方向及转速。
要求2:液压马达具有正、反转过载保护功能。
要求3:选用现场提供的叠加式液压元件及比例液压元件,将物料传输单元液压回路在图3中补充完整,并完成物料传输单元油路系统安装与调试。
要求4:在人机界面上设计P,I,D三个参数的设置窗口。
2.双缸轧制单元
本单元采用液压双缸带动轧辊,实现物料的滚轧。
选用柱塞泵油路系统供油,双缸轧制单元油路系统在满足如下要求时,进行液压系统安装与调试,注意安装及调试工艺须规范。
要求1:换向阀采用三位四通电磁换向阀,换向阀在中位时,液压泵不卸荷,执行机构被锁紧。
要求2:液压双缸下行(或上行)到底,液压缸无杆腔(或有杆腔)可无级电控调压,且系统压力同步变化。
要求3:液压双缸下行采用进油节流调速。
要求4:液压双缸上行采用进油调速,且液压双缸上行速度基本不受负载波动影响。
要求5:选用现场提供的叠加式液压元件及比例液压元件,将双缸轧制单元液压回路在图3中补充完整,并完成双缸轧制单元油路系统安装与调试。
要求6:调试出液压双缸下行到底,无杆腔压力值为5.2MPa,上行到底,有杆腔压力为4.6MPa,压力值填入表5,并举手示意报请裁判签字确认。
3.顶料单元
选用柱塞泵油路系统供油,顶料单元油路系统在满足如下要求时,进行液压系统安装与调试,注意安装及调试工艺须规范。
要求1:换向阀采用二位四通电磁换向阀。
要求2:顶料缸仅上行到底,液压缸无杆腔压力可调,且不影响系统压力。
要求3:顶料单元液压缸上行到底后,压力继电器动作发讯。
要求4:选用现场提供的叠加式液压元件,将顶料单元液压回路在图3中补充完整,并完成顶料单元油路系统安装与调试,固定螺钉拧紧扭矩符合技术要求,扭矩值填入表5,并举手示意报请裁判签字确认。
。
要求5:已知顶料缸缸筒内径尺寸为30mm,活塞杆外径尺寸为20mm,调节相应的液压元件至顶料缸上行模拟最大举升力为2543N(忽略摩擦及自重,π取3.14),并在液压回路图3(c)中找出测压点并标注为P2,同时将液压元件调定的压力值(MPa)填入表5,并举手示意报请裁判签字确认。
要求6:调试出顶料单元液压缸上行到底后,调试出压力继电器动作压力为P2±0.5MPa,动作指示采用蜂鸣器指示,压力继电器动作结果填入表5,并举手示意报请裁判签字确认。
注:顶料缸上行到底,无杆腔压力达到P2±0.5MPa时,蜂鸣器鸣叫。
要求7:根据叠加阀在液压回路中的位置,在表3中填写出顶料单元油路系统中叠加阀名称、叠加阀型号以及画出叠加阀职能符号。
表3 叠加阀在顶料单元油路系统中的位置
3
2
1
0
叠加阀基板
叠加阀位置顺序
叠加阀名称
叠加阀型号
叠加阀职能符号
4.物料冲压单元
选用柱塞泵油路系统供油,物料冲压单元油路系统在满足如下要求时,进行液压系统安装与调试,注意安装及调试工艺须规范。
要求1:换向阀采用三位四通电磁换向阀,换向阀在中位时,液压泵不卸荷,执行机构浮动。
要求2:物料冲压单元油路系统断电时,液压缸能在任意位置可靠锁紧。
要求3:三位四通电磁换向阀电磁铁断电,液压锁保压时,冲压缸无杆腔具有负载冲击保护功能。
要求4:冲压缸仅上行到底,有杆腔压力可调且系统压力同步变化,且电磁阀失电时,有杆腔具有负载冲击保护功能。
要求5:冲压缸上行采用节流阀回油节流调速,且不受溢流阀过载保护压力调节影响。
要求6:冲压缸无杆腔压力采用压力变送器采集。
要求7:选用现场提供的叠加式液压元件,将物料冲压单元液压回路在图3中补充完整,并完成物料冲压单元油路系统安装与调试,固定螺钉拧紧扭矩符合技术要求,扭矩值填入表5,并举手示意报请裁判签字确认。
要求8:调试出冲压缸冲压到底,无杆腔过载保护压力值为4.4MPa,并在液压回路图3(d)中找出测压点并标注为P3,压力值填入表5,并举手示意报请裁判签字确认。
要求9:调试出冲压缸上行到底,有杆腔压力值为4.0MPa,并在液压回路图3(d)中找出测压点并标注为P4,压力值填入表5,并举手示意报请裁判签字确认。
要求10:已知冲压缸缸筒内径尺寸为25mm,活塞杆外径尺寸为18mm,若冲压缸上行速度为25mm/s,则冲压缸有杆腔理论进油流量为 mL/s(四舍五入,保留小数点后1位,π取3.14)。
要求11:根据叠加阀在液压回路中的位置,在表4中填写出物料冲压单元油路系统中叠加阀名称、叠加阀型号以及画出叠加阀职能符号。
表4 叠加阀在物料冲压单元油路系统中的位置
5
4
3
2
1
0
叠加阀基板
叠加阀位置顺序
叠加阀名称
叠加阀型号
叠加阀职能符号
5.液压系统单步调试记录
表5 单步调试参数与功能确认表
序号
任务
结果记录(MPa)
选手确认
(填赛位号)
裁判确认
(签字确认)
备注
1
液压双缸无杆腔压力
2
液压缸有杆腔压力
3
顶料缸无杆腔压力
4
冲压缸无杆腔压力
5
冲压缸有杆腔压力
序号
任务
结果记录(N.m)
选手确认
(填赛位号)
裁判确认
(签字确认)
备注
6
顶料单元固定螺钉拧紧扭矩
7
冲压单元固定螺钉拧紧扭矩
序号
任务
结果记录(“是”或“否”)
选手确认
(填赛位号)
裁判确认
(签字确认)
备注
8
压力继电器动作是否正常(填“是”或“否”)
(三)气动回路安装与调试
1.工作任务1
选手根据赛场提供的设备,采用规范的安装及调试工艺,结合气动回路系统原理图(图4),选用合理的气动阀、气缸、气管及辅件,完成气动系统回路安装与调试。
图4 气动回路系统原理图
任务要求:
根据执行部件位置,合理利用赛场提供的元件,完成气动回路的安装与调试。
排除气动回路中设置的1~2个故障,排除故障并调试完成后,将调试结果填入表6,并举手示意报请裁判签字确认(气动回路能正常运行则判定故障排除)。
表6 气动回路安装及调试确认表
序号
调试任务
气缸动作是否正常
(填“是”或“否”)
选手确认
(填赛位号)
裁判确认
(签字确认)
备注
1
顶料气缸动作
2
推料气缸动作
3
挡料气缸动作
4
真空吸盘动作
5
双轴气缸动作
6
无杆气缸动作
2.工作任务2
任务要求2:继电器控制气动回路搭接与调试
在平台上搭接出1个采用继电器控制的双作用气缸往返动作回路。动作流程为:按下启动按钮→气缸慢速伸出→气缸伸出到位(无杆腔压力0.34MPa)→气控延时阀延时(约3s)→气控延时阀延时时间到→气缸快速排气缩回→气缸缩回到位,时间继电器延时(约3s)→时间继电器延时时间到→气缸再次伸出,动作依次往复循环。根据上述要求,搭接气动及电气控制回路,调试完成后,将调试结果填入表7,并举手示意报请裁判签字确认。
说明:允许使用工作任务1中的电磁换向阀。
表7气动回路设计功能确认表
序号
任务系统
结果记录/MPa
选手确认
(填赛位号)
裁判确认
(签字确认)
备注
1
气缸无杆腔压力
序号
任务系统
动作结果
(填“是”或“否”)
选手确认
(填赛位号)
裁判确认
(签字确认)
备注
1
具有气缸往复
循环动作功能
2
具有慢速伸出功能
3
具有气缸伸出到底
气控延时阀延时功能
4
具有快速排气功能
5
具有气缸缩回到底
时间继电器延时功能
任务二、电气控制回路连接与排故(10分)
选手根据赛场提供的设备,采用规范的安装及调试工艺,选取合适的导线和辅件,完成电气控制回路的连接,并完成各执行部件动作功能测试。
两台PLC选用控制屏模拟控制单元与挂箱(西门子或三菱)模块PLC。
工作任务1:
要求1:根据 I/O表,使用实验导线将液压电磁阀、气动电磁阀与相应控制单元的PLC输入、输出端及模拟量输入、输出端进行连接。
说明:未按照附件1或附件2(I/O分配表)接线,此项分数在程序运行验证中扣除。
要求2:实训导线、通信线的连接、插拔应符合操作规范。
要求3:挂箱面板同一接线柱最多插两层导线。
说明:任务一中继电器控制气动回路搭接与调试除外。
要求4:实训台与挂箱、阀与挂箱之间的连接导线,按不同功能分开进行捆扎,间距为80mm~100mm。
工作任务2:
要求1:根据 I/O表,完成3-4个传感器的安装、接线及调试,安装调试完成后,在表9中填写出安装调试的传感器名称,并将调试结果举手示意报请裁判签字确认。
要求2:在附件3上画出挂箱模块PLC接线图。
表9 传感器安装调试功能确认表
序号
传感器名称
调试结果是否正确
(填“是”或“否”)
选手确认
(填赛位号)
裁判确认
(签字确认)
备注
1
2
3
4
任务三、控制系统PLC程序设计(10分)
根据现场所提供设备及工业气动元件、液压元件及赛场提供的任务书,编写 PLC控制程序,控制液压泵站、物料传输单元、双缸轧制单元、顶料单元、物料冲压单元、下料堆垛单元。把设计好的程序保存到电脑的 “D: \液压与气动系统装调与维护\赛位号\任务三 PLC程序文件夹”下。
任务要求:
要求1:程序注释
编写程序时,相应的输入、输出点及温度、位移、速度、压力、转速变量加上中文注释。
要求2:控制系统
选用控制屏上模拟控制单元PLC与挂箱(西门子或三菱)模块两台PLC组成,两台PLC须通过Modbus RTU网络通信(西门子)或N:N网络通信(三菱)进行数据交换。
要求3:模拟量信号采集及处理功能
① 双缸轧制单元液压双缸位移采集功能:实时监测液压双缸位置变化,并以十进制形式在地址D66(西门子VD66)中显示液压双缸伸出实时位置值,液压双缸伸出到底显示150mm,缩回到底显示0mm,误差±0.5mm。
② 双缸轧制单元液压双缸速度采集功能:实时监测液压双缸速度,并以十进制形式在地址D76(西门子VD76)中显示液压双缸实时速度值。
③ 物料冲压单元液压缸位移采集功能:实时监测冲压缸位置变化,并以十进制形式在地址D86(西门子VD86)中显示冲压缸伸出实时位置值,冲压缸伸出到底显示150mm,缩回到底显示0mm,误差±0.5mm。
④ 物料冲压单元液压缸速度采集功能:实时监测冲压缸速度,并以十进制形式在地址D96(西门子VD96)中显示冲压缸实时速度值。
⑤ 物料冲压单元液压缸压力采集功能:实时监测冲压缸无杆腔压力,并以十进制形式在地址D106(西门子VD106)中显示实时压力值。与压力表示数差值±0.2MPa。
⑥ 温度采集功能:实时监测油箱的温度变化,并以十进制形式在地址D116(西门子VD116)中显示当前温度值,与温度表示数偏差±1℃。
说明:三菱系统为电流信号(4~20mA),西门子系统为电压信号(1~5V)。
要求4:液压马达转速采集功能
实时监测液压马达的转速变化,以十进制形式在地址D126(西门子VD126)中显示当前转速值。
要求5:油箱温度控制功能
泵站启动后,油温高于30℃(达不到30℃则设定比当前温度值小1℃动作),冷却风扇启动。
要求6:泵站保护功能
油过滤器压差保护、液位低保护。当压差发讯信号断开或者液位低信号闭合时,液压泵停机。
要求7:切换功能
通过切换01控制按钮模块上的旋钮开关SA2,可以选择“手动功能”、“单周期运行功能”和“全自动运行功能”。
说明:旋钮开关SA2对应的第1个触点为一组,第2、3个触点同为另一组(自左往右)。
要求8:手动功能
将SA2旋钮开关旋至左位,进入手动功能
① 按钮开关SB6控制柱塞泵启、停。
② 按钮开关SB7控制叶片泵启、停。
③ 按钮开关SB1控制液压马达正转。
④ 按钮开关SB2、SB3分别控制液压双缸伸出、缩回。
⑤ 按钮开关SB4、SB5分别控制冲压缸伸出、缩回。
要求9:停止功能
物料离开上料单元后,按下停止按钮SB1,则系统不会立即停止,继续完成当前物料的加工和堆垛后,停止上料,蜂鸣器以1Hz的频率提示(注:泵站与传送系统不停止)。按下启动按钮SB2后,蜂鸣器停止报警,继续上料运行。
要求10:复位功能
按下SB3按钮,系统进行复位。复位时根据各传感器是否处于初始状态,执行相应的复位动作,系统有15s的运行过程。完成后蜂鸣器以0.5Hz频率提示复位完成,3s后停止鸣叫。
要求11:故障报警功能
现场裁判任意指定选手断开液压双缸或冲压缸对应的PLC输出点,当程序运行检测到该点有输出时,延时2s,蜂鸣器报警。报警形式为每间隔2s,蜂鸣器分别以2Hz鸣叫2声(液压双缸)、3声(冲压缸),该线插上后,报警停止,继续当前动作。
说明:全自动运行中断开1个点,由裁判任意指定
要求12:急停功能
全自动运行过程中,按下01挂箱上的急停按钮QS模拟急停,叶片泵及柱塞泵不停机,柱塞泵系统切换为二级压力,液压马达、液压缸及气动缸均停止动作,真空吸盘若已吸取物料则继续保持吸取状态;急停按钮复位后,继续沿当前加工工序继续进行。
要求13:单步调试功能
SA2旋钮开关旋至中位,进入单步调试功能。每按下一次启动按钮SB2,系统工作一步(叶片泵启动开始,验证到第4步)。
要求14:全自动运行功能
SA2旋钮开关旋至右位,进入全自动运行功能。按下SB2启动按钮后,执行系统工作流程,且进行3块物料的加工。按下启动按钮SB2→叶片泵启动→延时2s→柱塞泵启动→延时2s→泵站控制阀得电→液压马达以35r/min正转→延时2s→液压双缸以25mm/s速度伸出至135mm(第2次140mm,第3次145mm)→顶料气缸伸出→延时2s→推料气缸推出物料→推料气缸到位后缩回(缩回到位,顶料气缸缩回)→冲压单元检测入料→挡料气缸伸出→冲压单元物料到位→液压双缸以30mm/s速度缩回→延时2s →顶料单元液压缸顶起物料→压力继电器发讯→冲压缸冲压→冲压缸冲压到底,压力变送器发讯→延时2s→冲压缸以25mm/s速度缩回→冲压缸缩回到位,顶料缸缩回→液压马达速度切换为55r/min→挡料气缸缩回→下料单元物料检测到位→下料单元双轴气缸伸出→双轴气缸伸出到位→真空吸盘吸取物料→延时2s→双轴气缸缩回到位→无杆气缸右移,右移到位→步进电机由原点上升至第一块物料堆垛位置→真空吸盘关闭,完成第1块物料的堆垛→步进电机退回→无杆气缸左移→无杆气缸左移到位→伺服取料机构X轴及Y轴取料伸出速度为20mm/s±1mm/s,取料缩回速度均为15mm/s±1mm/s,取回物料放入相应的料仓内→液压马达速度切换为35r/min→液压双缸伸出,继续循环顶料、出料、轧制、冲压及堆垛流程,完成剩余2块物料的加工、堆垛和物料入仓。3块物料入仓完成后,液压马达停转→蜂鸣器以1Hz频率鸣叫→变量叶片泵停止→延时2s→泵站控制阀失电→延时2s柱塞泵停止、蜂鸣器停止鸣叫。
要求15:程序确认
选手PLC程序设计完成并下载调试完成各项功能后,在表10中确认程序并举手示意报请裁判签字确认程序。
说明:程序一经确认不得修改,程序签字确认后才允许报请裁判验证表10及表11中的功能。
表10 程序确认表
程序是否确认
(填“是”或“否”)
确认时间
(填当前时间)
选手确认
(填赛位号)
裁判确认
(签字确认)
备注
要求16:功能结果记录
在表11中记录各功能执行情况,并举手示意报请裁判签字确认。
表11 PLC程序功能确认表
序号
任务要求描述
完成情况
(填“是”或“否”)
选手确认
(填赛位号)
裁判确认
(签字确认)
备注
1
液压双缸位移采集功能
伸出到底150mm,缩回到底0mm,误差±0.5mm
2
冲压缸位移采集功能
伸出到底150mm,缩回到底0mm,误差±0.5mm
3
冲压缸压力采集功能
与表压误差±0.2MPa
4
温度采集功能
5
液压马达转速采集功能
6
油箱温度控制功能
7
泵站保护功能
8
柱塞泵按钮开关控制
9
叶片泵按钮开关控制
10
液压马达正转按钮开关控制
11
液压双缸按钮开关控制
12
冲压缸按钮开关控制
13
停止功能
14
复位功能
15
故障报警功能
16
急停功能
17
单步调试功能
任务四、上位机组态(10分)
任务描述:
用设备提供的上位机组态软件MCGS设计组态界面,并与现场可编程控制器连接,实现画面监控。
要求1:建立过程变量。
要求2:设计叶片泵启、停控制功能。
要求3:设计柱塞泵启、停及压力切换控制功能。
要求4:设计液压马达转速实时曲线监控界面,并进行速度监控。
要求5:设计冲压缸位置曲线监控界面,并进行冲压缸位置监控。
要求6:设计步进电机点动控制界面,可进行步进电机速度切换并实时显步进电机转速。
在表12中记录组态功能完成情况,并举手示意报请裁判签字确认。
表12 组态设计与调试功能确认表
序号
任务要求描述
完成情况
(填“是”或“否”)
选手确认
(填赛位号)
裁判确认
(签字确认)
备注
1
叶片泵启、停控制功能
2
柱塞泵启、停控制功能
3
柱塞泵压力切换控制功能
4
液压马达转速实时曲线
5
冲压缸位置实时曲线
6
步进电机点动控制功能
7
步进电机转速切换控制功能
8
步进电机转速显示功能
任务五、整机调试与运行(10分)
根据所提供设备并综合任务一至任务四,完成整机调试与运行。液压系统图见图3,气动系统图见图4。
任务要求:
要求1:叶片泵、柱塞泵依次能正常启动,泵站控制阀得电。
要求2:上料单元顶料气缸、推料缸能依次正常动作,物料能顺利出仓。
要求3:物料传输单元液压马达转速采用PI控制功能。
要求4: 物料传输单元液压马达转速具有35r/min-55r/min-35r/min切换功能,稳定转速误差±2r/min。
要求5:液压双缸伸出位置依次为135mm、140mm、145mm,误差±1mm。
要求6:液压双缸伸出速度25mm/s,误差±2mm/s。
要求7:液压双缸缩回速度30mm/s,误差±2mm/s。
要求8:具有顶料-冲压功能。
要求9:冲压缸缩回速度为25mm/s,误差±2mm/s。
要求10:具有物料搬运、堆垛功能,要求堆垛物料时,物料的下表面与接料台上表面间隙不得超过1cm。
要求11:伺服取料机构X轴及Y轴取料伸出速度为20mm/s±1mm/s,取料缩回速度均为15mm/s±1mm/s。
要求12:整个系统需完成3块物料入仓。
要求13: 3块物料堆垛完成后,蜂鸣器以1Hz频率鸣叫,柱塞泵停止后蜂鸣器停止鸣叫。
要求14:整套系统每个单元工作衔接流畅,不出现任何故障现象。
在表13中记录各单元运行功能,并举手示意报请裁判签字确认。
表13 整机运行与调试确认表
序号
任务要求描述
完成情况
(填“是”或“否”)
选手确认
(填赛位号)
裁判确认
(签字确认)
备注
1
叶片泵、柱塞泵
顺序启动功能
2
顶料-推料出仓功能
3
马达转速PI控制功能
写出P及I的值并在程序中给裁判指出
P: I:
4
液压马达速度切换功能35r/min-55r/min-35r/min稳定转速误差±2r/min
5
双缸滚轧位置135mm,140mm,145mm
误差±1mm(填滚轧位置)
滚轧位置1: mm
滚轧位置2: mm
滚轧位置3: mm
6
液压双缸伸出速度25mm/s
误差±2mm/s
7
液压双缸缩回速度30mm/s
误差±2mm/s
8
顶料-冲压功能
9
冲压缸缩回速度25mm/s
误差±2mm/s
10
物料搬运、堆垛功能
11
伺服取料机构伸出速度20mm/s±1mm/s
12
伺服取料机构缩回速度15mm/s±1mm/s
13
入料完成3块物料
完成 块
(填数字)
14
堆垛完成提醒功能
15
系统工作流畅
附件3
挂箱PLC模块接线图
场次号:
赛位号:
液压与气动系统装调与维护赛项
2022年全国职业院校技能大赛高职组 智能电梯装调与维护赛项模拟赛题(Word版): 这是一份2022年全国职业院校技能大赛高职组 智能电梯装调与维护赛项模拟赛题(Word版),文件包含智能电梯装调与维护赛项赛题A卷doc、智能电梯装调与维护赛项赛题B卷doc、智能电梯装调与维护赛项赛题C卷doc、智能电梯装调与维护赛项赛题D卷doc、智能电梯装调与维护赛项赛题E卷doc、智能电梯装调与维护赛项赛题F卷doc、智能电梯装调与维护赛项赛题G卷doc、智能电梯装调与维护赛项赛题H卷doc、智能电梯装调与维护赛项赛题I卷doc、智能电梯装调与维护赛项赛题J卷doc等10份试卷配套教学资源,其中试卷共170页, 欢迎下载使用。
2022年全国职业院校技能大赛高职组 数控机床装调与技术改造赛项模拟赛题(Word版): 这是一份2022年全国职业院校技能大赛高职组 数控机床装调与技术改造赛项模拟赛题(Word版),文件包含样题1docx、样题10docx、样题2docx、样题3docx、样题4docx、样题5docx、样题6docx、样题7docx、样题8docx、样题9docx、评分标准docx等11份试卷配套教学资源,其中试卷共234页, 欢迎下载使用。
2022年全国职业院校技能大赛中职组 网络布线赛项模拟赛题(word版): 这是一份2022年全国职业院校技能大赛中职组 网络布线赛项模拟赛题(word版),文件包含2022网络布线-赛题1docx、2022网络布线-赛题10docx、2022网络布线-赛题2docx、2022网络布线-赛题3docx、2022网络布线-赛题4docx、2022网络布线-赛题5docx、2022网络布线-赛题6docx、2022网络布线-赛题7docx、2022网络布线-赛题8docx、2022网络布线-赛题9docx、2022网络布线赛项评分标准pdf等11份试卷配套教学资源,其中试卷共353页, 欢迎下载使用。